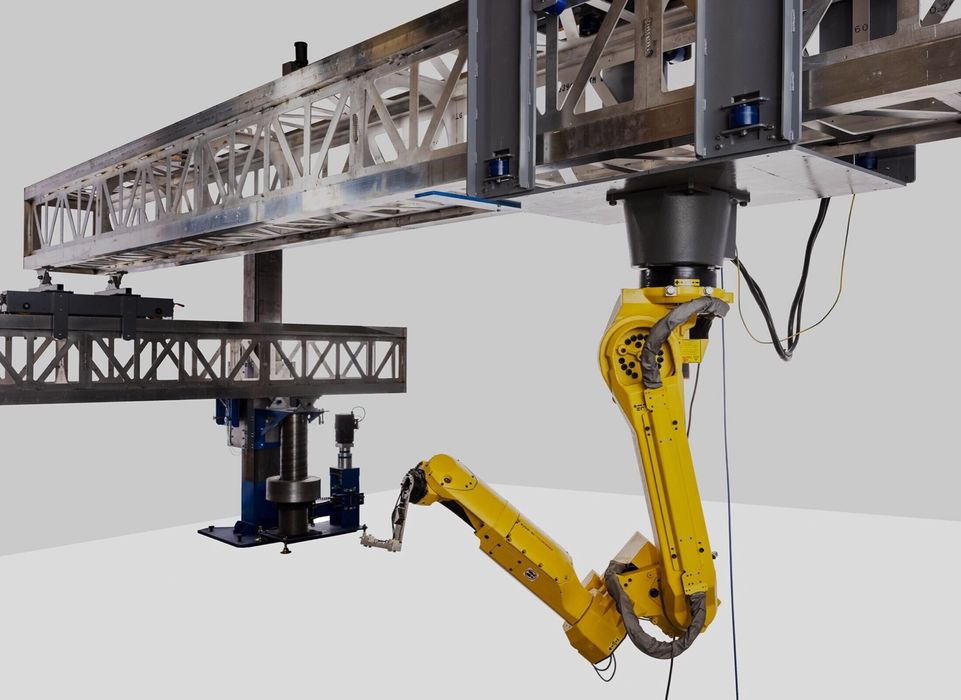
A California company seems to have figured out how to take construction 3D printing to the next level.
While construction 3D printing is not new, it has been incredibly mis-portrayed in the media. The technology to date consists of various forms of concrete extrusion and has considerable constraints on design and scale. Essentially, construction 3D printing of today consists of producing the foundation and walls of a structure and not much else. The rest is left to conventional trades people for traditional installation.
The result is that the concrete portions of the build are sped up and perhaps more economical, but the rest of the project is entirely traditional. While the media talks of “3D printing homes in 24 hours”, this is never the case. Even worse, some in the construction 3D printing industry encourage this type of mis-reporting.
Now there may be a company that is going beyond mere concrete 3D printing and taking on those other traditional build roles.
Diamond Age 3D, who recently received a US$8M investment from a group of venture capital investors, has proposed a new style of construction 3D printing that at first glance appears much more comprehensive than current construction 3D printing.
The company uses a gantry system with robotic arm to completely produce a home on site, unlike Mighty Buildings, which makes the homes at a factory and ships them to the site.
The first step in Diamond Age’s process is to 3D print the concrete portions of the structure. This appears to be near-identical to the methods used by several other construction 3D printer manufacturers.
Then it gets interesting. Rather than tearing down the gantry and moving on to another site, the gantry and robotic arm are re-used for more functionality. How is this done?
With toolheads!
The Diamond Age robotic arm is able to use a “suite of 26 robotic tools.” Look at this image from Diamond Age that shows icons for some of the 26 tools:
I can see drills, cutters, edgers, scanners, grabbers, bulldozer blades and others I cannot identify. And that image has only eleven of 26 different tools apparently available.
Their plan is to swap in tools in a sequence that gradually builds the home. For example, we can see in their promotional video a partial list of some of the steps that can be done by the system:
- Wall scan
- Exterior paint
- Interior wall finish
- Interior wall paint
- Cabinet / Fixture attach rails
- Floor scan
- Flooring install
- Roof truss place & attach
- Purlins / bracing
- Roof sheathing
- Roof scan
- Roof paper / felt apply
- Paper detail / trim
- Roof shingle install
- Roof ridge vent install
- Detail – trim
There is obviously much more we can’t see yet, but I think you can get the idea they are doing far more than just concrete extrusion here.
But what’s this about a “wall scan”? It turns out that after the concrete extrusion is completed, they 3D scan the entire structure as built and that replaces the original CAD 3D model for subsequent steps. This should make that work more accurate.
This is the promotional video from Diamond Age:
One very interesting aspect of their process is how they handle overhangs. The problem is that concrete is a terrible material for extrusion, as it requires 100% support underneath. This means you cannot 3D print window holes, for example, without stopping the print and inserting a board to hold up the next layer of concrete. Competing construction 3D printers typically use that approach, which requires the printer to stop while manual intervention takes place.
Meanwhile, Diamond Age takes on that issue completely differently: they 3D print the entire structure without holes, and then in a subsequent step a cutting blade wielded by the robot simply cuts holes where needed.
This produces some amount of wasted concrete, but would vastly speed up the extrusion process. Other construction 3D printer options cannot do this because they don’t have the ability to change toolheads.
Diamond Age explained their build process has a 12 day cycle, from start to finish, and that this supposedly reduces the labor cost by 55%. That is a figure very different from that provided by the other construction 3D printer manufacturers whose statistics relate ONLY to the concrete extrusion portions of the build. Here, Diamond Age is talking about ALL the steps.
With seven gantry systems operating in leapfrog fashion, they say they can produce up to 250 homes within a single year.
This is a highly impressive concept that I’ve been waiting for a long time to see. I may still be waiting, however, as this is merely a concept at this stage, and there are surely many details to be worked through by Diamond Age. You’ll note their video shows only a rendering of the concept.
But the new US$8M investment provides some confidence they may be able to make this fly.
Via Diamond Age and TechCrunch