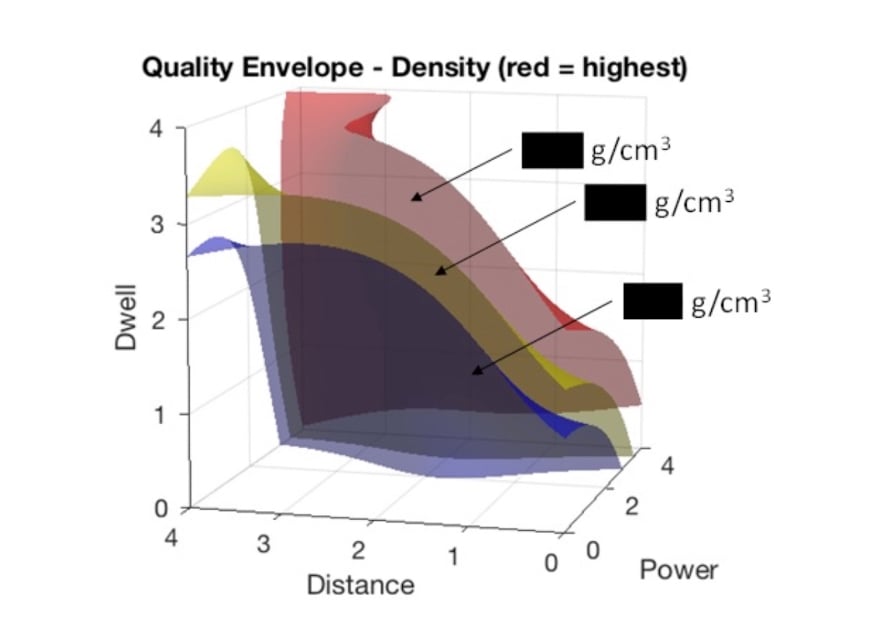
The process of “dialing in” optimal 3D print parameters can be challenging, but how is this best done in a rapidly evolving industrial environment?
Dialing In 3D Printing Parameters
“Dialing in” is the process of gradually tweaking the numerous 3D printing parameters to achieve the optimal quality on subsequent 3D print jobs. It’s a painstakingly tedious process involving iterative 3D prints and inspecting the results of each tweak. Gradually one can hone in on the best settings, or what “seems” to be the best settings. In most cases, 3D print operators simply get to a point where it is “good enough” and call it a day.
It gets worse: if you change the 3D printer in any way, or use a different material, you must start over to identify the best parameters for the new configuration. Sometimes you have to do so even if the model’s geometry changes.
3D Print Profiles
This tedious process is too much for some users, and that can even curtail their 3D printing activities. The reaction from some 3D printer vendors has been to produce pre-made “print profiles” that list the optimal parameters for a given combination of machine and specific material.
That works, and in a sense it is a way to re-use the iteration that’s been done in advance by the manufacturers’ techs.
But print profiles don’t work for highly specialized manufacturing, where the absolute best results are mandatory. In such cases, the operators must perform the tedious iterations to identify the best print parameters.
However, that is problematic for organizations that are hoping to use their 3D printers for speedy manufacturing. You don’t want to wait a week or three for a series of 3D print tests to get those parameters.
Senvol ML
There is a solution to this dilemma: Senvol’s ML system.
This is a machine learning system that combines a massive materials and equipment database with machine learning algorithms to enable prediction of optimal 3D print parameters. The system uses previously completed print data to very quickly find print parameters that fall within an envelope of acceptability.
See the chart at the top? That’s an example of Senvol ML’s output, which shows one of their sample parameter envelopes.
This particular chart uses three key 3D print parameters commonly used in the PBF metal process: dwell time, laser power and distance. As you can see, the density of the resulting metal part can change significantly as these parameters are adjusted.
This chart can be extremely valuable, because tweaking one parameter can affect the others. By enabling a visual of the situation, a 3D printer operator can near-instantly identify the desired solution zone. While this may not always identify the true optimal parameters, it certainly narrows the possibilities down considerably, and that can save a lot of iteration time.
While the power of Senvol ML is significant, it’s not for everyone, as it’s best used in industrial settings where speed is of the essence.
One of Senvol’s recent clients is the United States Army Research Laboratory for a “missile project”. They have not provided a lot of details on this mystery project for obvious reasons, but the point here is that the Army is one organization that indeed needs to develop solutions quickly, and that’s the sweet spot for Senvol ML. There are likely many other potential Senvol ML users in and outside of government.
Unfortunately, I’m not one of them, as I don’t happen to operate an industrial 3D print farm. But a solution of this type would surely be welcomed by more casual 3D printer operators if it was affordable.
Via Senvol