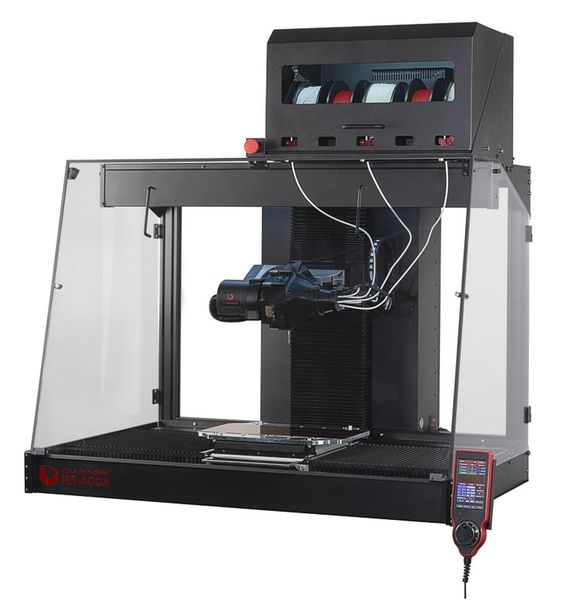
Diabase Engineering announced a big upgrade for their line of hybrid 3D printing / CNC milling devices with the new H5-400A.
The Colorado-based company has been producing hybrid equipment for some years now, with the most recent machine we’ve seen being the multi-material H unit from 2019.
These machines by can be equipped with a CNC mill of three, four or even five axes of motion. The 5-axis system in particular will be able to handle tricky geometries that are beyond the reach of three and four axis systems. One of the axes is rotational, so you can easily produce cylindrical objects of all types.
The spindle speed can range up to 12,000 RPM, which is decently fast and should allow the H5-400A to work on a wide variety of materials.
The new H5-400A inherits many of the characteristics of the earlier designs, but improves by adding several new features.
The most notable and visible feature is the enclosure. Previously the H-series were open format, or with a transparent plastic cover. However, the H5-400A’s enclosure is a bit different: it’s designed for easy maintenance.
This is actually quite an important point for two reasons: first, 3D printers tend to break a lot and frequently require maintenance that’s buried deep inside the machine, and secondly, some competitive enclosures seem to have been designed more with aesthetic reasons than practical features. In other words, it can sometimes be quite difficult to get access to some enclosed 3D printers: “some disassembly / reassembly required!”
That’s definitely not the case with the H5-400A, which not only allows you to lower the hinged sides down for easy access, but you can also remove them entirely. I can’t say I’ve ever seen a more accessible enclosed 3D printer design.
The H-series also includes a dry box for storing filament spools securely, and it’s located above the build chamber. However, on the new H5-400A the dry box now opens from the front. This is a very practical decision, because it eliminates the need for clearance behind the machine and thus significantly reduces the footprint.
The CNC milling operation causes the need for a feature that’s not found on typical 3D printers: a chip box! This is a receptacle for the bits that are torn off objects by the milling head, and they have to go somewhere.
I’ve seen other multi-tool devices completely forget about this problem, and the inevitable result is a massive pile of debris all over the inside of the machine. That’s not good because small bits can get tangled up in motion belts, bearings or other mechanical components and cause failures or quality issues. It baffles me why so many multi-tool 3D printer designers don’t consider this an issue.
Meanwhile, the H5-400A has taken all this into account and incorporated a “large” chip pan and shrouding at the bottom of the machine. It also makes use of compressed air to help corral these bits during milling operations.
The H5-400A also includes some specialized firmware tuning to allow for faster operational speeds as well as more automated calibrations. By the way, those calibrations include the CNC milling subsystem, including the rotary axis.
The new motion system on the H5-400A allows for a bigger build volume of up to 416 x 186 x 375 mm, which is quite large. There’s even a 1.2mm nozzle option to enable rapid 3D printing of larger parts.
I’m impressed with the maturity of this design; the upgrades are all quite practical and indicate attention paid to the needs of machine operators. It’s refreshing to see such practicality at work. If you’re looking for a practical multi-tool 3D printer, please check out the Diabase Engineering H5-400A.
Via Diabase