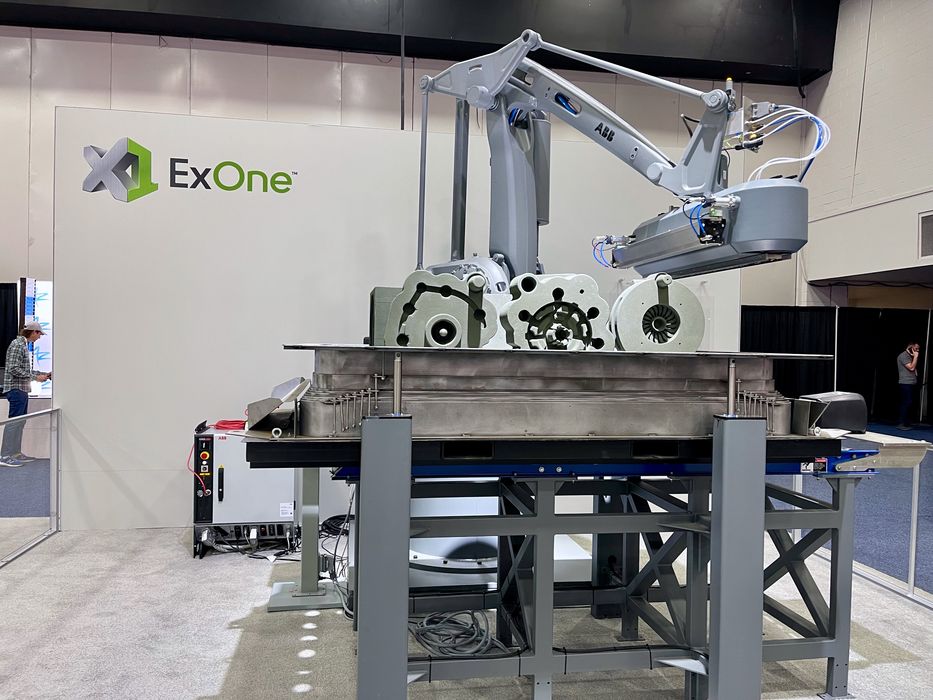
Desktop Metal is now leveraging all those corporate acquisitions they’ve made over the past couple of years.
The company, which began as a producer of an affordable metal 3D printer (hence their name), now boasts of multiple 3D printing processes and both prototyping and production capabilities.
This is in large part due to their rather aggressive set of acquisitions over the past while. So far, they’ve acquired:
There’s likely even more going on behind the scenes we haven’t yet heard about from Desktop Metal.
Acquiring companies isn’t something done just for fun. There are precise strategies involved that drive these deals to completion.
One strategy often active during an acquisition is to consolidate operations. This happens when two or more companies are doing basically the same operations. The joint set of customers is then moved under a single operation and money is saved by shutting down the excess operations.
That’s not what Desktop Metal is doing here.
Instead, Desktop Metal is using the second strategy type used during acquisitions: complementing. Here we have a case of acquired companies NOT doing the same thing, but in fact are performing complementary operations. The theory is that the sum is greater than the parts.
But is Desktop Metal actually doing this?
Up to now the most visible step in consolidation I’ve seen from Desktop Metal has been a bit of rebranding, where they ditched the EnvisionTEC brand and replaced it with ETEC. They’ve also rebranded some of the ExOne products. I’m sure there are more things happening at the company, such as administrative consolidations, but we don’t get to know much about that.
Lately, however, it seems the “complementary” aspect of the acquisitions seems to be having fruit.
Desktop Metal introduced an unusual device, the S-Max Flex. This is a combination of technologies from both Desktop Metal and the former ExOne, which produced sand 3D printers.
The idea here seems to be to use the robotic system from ExOne and combine it with Desktop Metal technology to create a far less expensive sand printing system for producing metal objects.
The result is a system that reduces the price foundries would pay for metal 3D printing from over a US$1M, to about half.
This is of particular interest to the foundry market in the West, because they are under significant demand for products as a result of the supply chain breakdown. Manufacturers are increasingly seeking local or regional suppliers, rather than relying on overseas providers that are now often unreliable and expensive.
Foundries would like to take up this demand, but there’s a simultaneous shortage of workers, which makes it extremely challenging for these companies to succeed. However, Desktop Metal’s S-Max Flex’s robotic approach may reduce the need for staff and provide a cost effective solution.
A representative from Desktop Metal told me:
“It’s the hottest thing seen in foundries this year!”
What’s even more interesting is that this printing concept is scalable: it can be made as large as a robot can reach. Thus, if customers want an even bigger build volume, Desktop Metal need only get bigger robots.
Why wasn’t this done previously? The problem is that when companies are separate they hold their own intellectual property and any technological combinations require complex, lengthy contractual negotiations that usually don’t happen. But when under a single umbrella, Desktop Metal in this case, it’s simply something that gets done.
I’m hoping to see more interesting tech combinations from Desktop Metal in the future.
Via Desktop Metal and ExOne