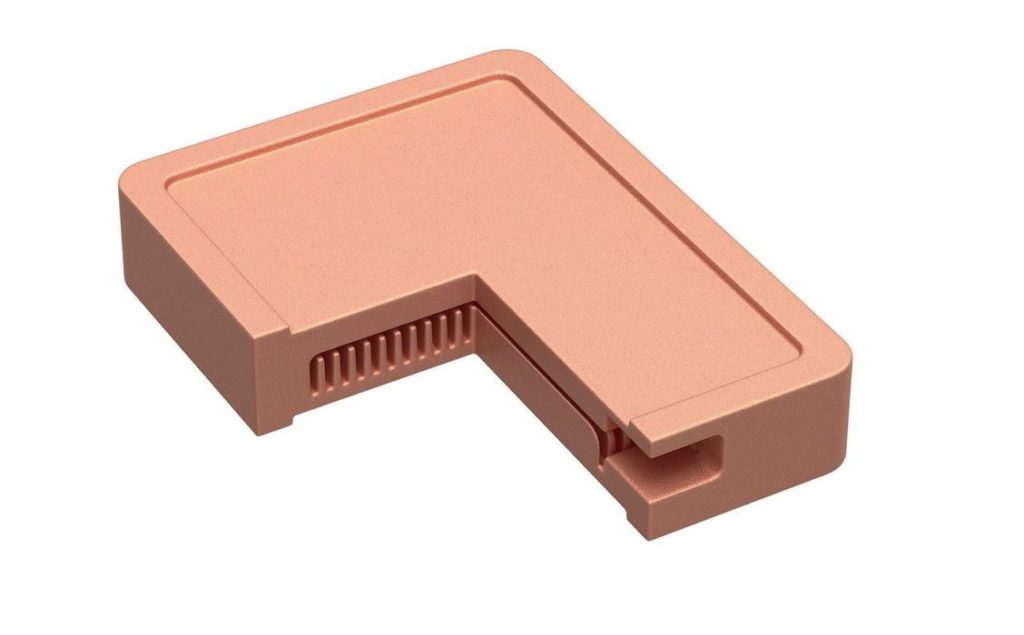
Desktop Metal announced the qualification of a pure copper material for their Production system.
Copper is a highly desirable material in the AM industry as it provides a number of very useful engineering properties, including electric and heat conductivity.
This makes it ideal for applications where electrons or heat is being transferred. Heat exchangers, antennae and similar components are what’s at issue here, as 3D printing can allow them to be produced in highly complex geometries that can be far more effective than the simpler structures achievable with traditional manufacturing methods.
So why isn’t everyone 3D printing copper objects?
It’s because it’s a very problematic material for most common metal 3D printing processes. The standard laser PBF or electron beam PBF processes inject tremendous amounts of energy into the print bed, and copper has such a high energy transfer that the heat dissipates into the surrounding area, messing up the print.
These processes cannot properly 3D print copper, so alternative metal 3D printing processes must be used. One of them is binder jetting, which just happens to be the process used by Desktop Metal’s Production system.
In a binder jet system the part is printed “cold”, and a binder holds the metal particles together temporarily. Later a sintering process removes the binder and fuses the metal particles together all at once.
It’s thus very possible to 3D print copper and similarly conductive materials on binder jet systems without issue.
However, for proper production applications materials must be certified before a manufacturer would make products for clients with them. That’s exactly what Desktop metal has done here: they have certified a copper material for use in their Production system. They explain:
“Desktop Metal’s materials science team has qualified and fully characterized commercially pure copper (C10300) printed on Production System technology with greater than 99.95 percent purity, enabling excellent thermal and electrical conductivity. Manufacturers can now print copper parts on the Production System with significant geometric complexity in a single step instead of brazing multiple conventionally produced copper components together, eliminating a time-intensive and expensive process prone to error and waste. With the geometric freedom enabled by binder jetting, engineers can also explore new, high-performance designs not possible with conventional manufacturing methods, such as the lattice structures and conformal cooling channels to improve heat transfer.”
In the example at top, we can see a copper part that includes a complex interior structure. This part could be quite difficult to produce using conventional making methods, but is quite easy to 3D print, particularly with a binder jet system that provides support to the object during printing.
Desktop Metal said copper was the most requested material from their clients, and it seems they have been able to meet that need.
Going forward, it is likely that some manufacturers might pick up a Production system to enable larger-scale production of complex copper parts. That’s a capability few manufacturers would have, making for a potentially highly profitable venture.
Via Desktop Metal