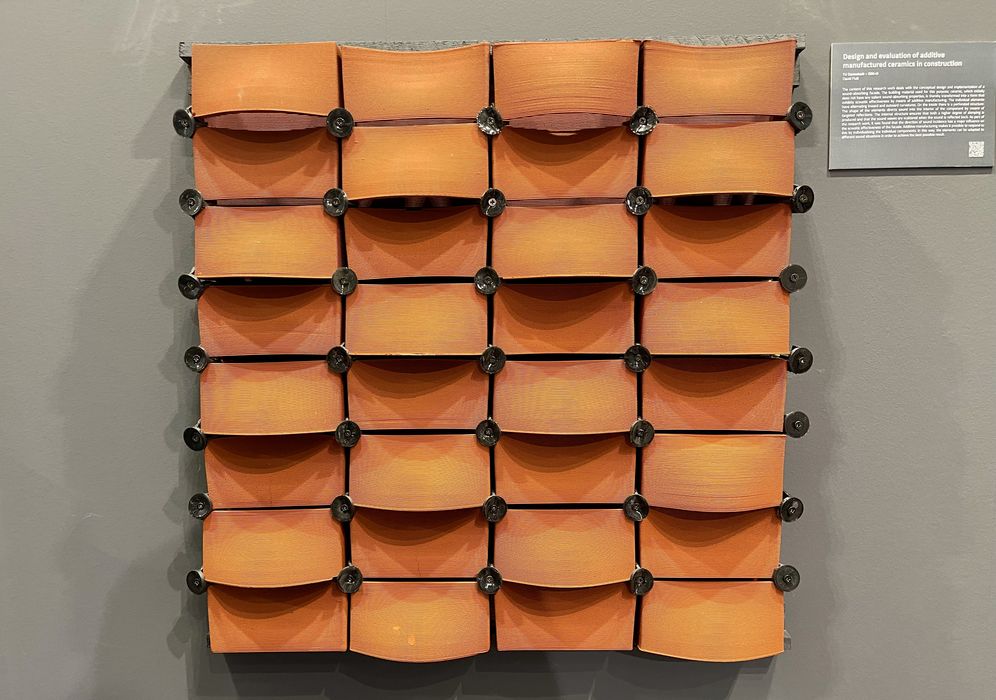
This week’s selection is the Sound Absorbing Facade by David Fluß of TU Darmstadt.
A sound absorbing facade? What’s that for?
If you’ve ever worked in an office that didn’t account for sound echoes, you’d know exactly what this is for. Typical office surfaces, such as hard walls, glass and non-carpeted floors reflect sound quite well. This can make for incredibly noisy spaces, so sound absorbing materials are used. In fact, there are companies that specialize in optimizing sound in this way.
The typical materials used are carpets, which soak up much of the sound waves, as well as drop-down ceilings that have sound absorbing tiles. In extreme cases it’s sometimes necessary to install sound absorbing panels on the walls, particularly in glass-filled offices.
All of these materials are “fuzzy”. Carpet is soft, ceilings tiles are made of sound absorbent material, etc.
Here we have something very different, yet it serves the same purpose.
It’s a 3D printed wall facade that is sound absorbent — but it is not “fuzzy”. It’s rock solid, like most 3D prints. In fact, it’s actually 3D printed ceramic material.
Fluß explains how this works:
”The building material used for this purpose, ceramic, which initially does not have any salient sound-absorbing properties, is thereby transformed into a form that exhibits acoustic effectiveness by means of additive manufacturing. The individual elements have alternating inward and outward curvatures. On the inside there is a perforated structure.
The shape of the elements directs sound into the interior of the component by means of targeted reflections. The internal structure ensures that both a higher degree of damping is produced and that the sound waves are scattered when the sound is reflected back. As part of the research work, it was found that the direction of sound incidence has a major influence on the acoustic effectiveness of the facade.”
This is quite an interesting development, as it means it is possible to design 3D printed buildings that can include customized sound control directly in the building structure. There would be no need for additional acoustic accoutrements.
This potentially takes a further step into actual 3D printed homes. Up to now for all practical purposes “3D printed homes” means that the concrete bits were printed instead of poured. The rest of the construction is done using standard trades and tools.
But now we can knock off the sound absorption steps of those trades. I’m hoping further research can continue to integrate construction requirements into printable models, reducing the effort to build homes in the future.
Via TU Darmstadt