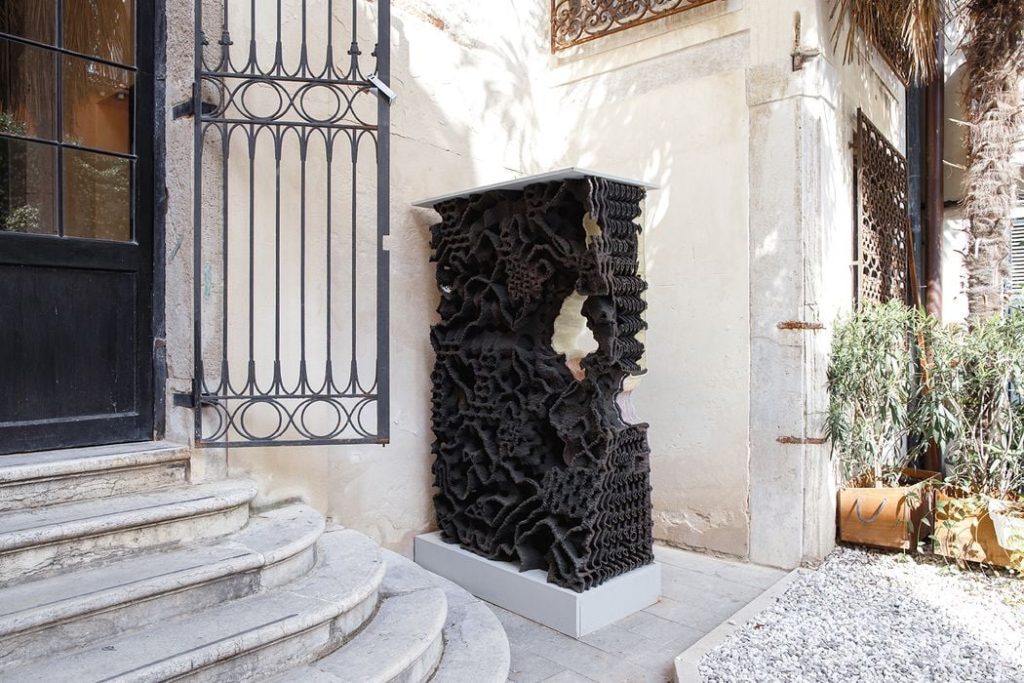
This week’s selection is the Meristem Wall by David Andreen and Ana Goidea.
The Meristem Wall is an outdoor 3D printed piece that has a unique and highly complex design. The two Swedish architects sought to leverage 3D printing technology in an innovative manner for this project. Both work with the bioDigital Matter Lab at Lund University.
Andreen explains:
“While 3d printed architecture is a hot topic today, almost all commercial applications focus on efficiency, speed and cost reduction. We believe that 3D printing can be revolutionary in the construction industry but this requires a complete rethink of the what as well as the how.“
Goidea adds:
“3D printing brings two distinct advantages to the construction industry: the ability to create parts of high formal complexity, and the fact that every part produced can be unique. It becomes possible to create building envelopes that passively harness the local micro-climates by storing heat and humidity, driving airflows through convection, and similar mechanisms.”
That’s certainly evident in the unusual geometry of the Meristem Wall.
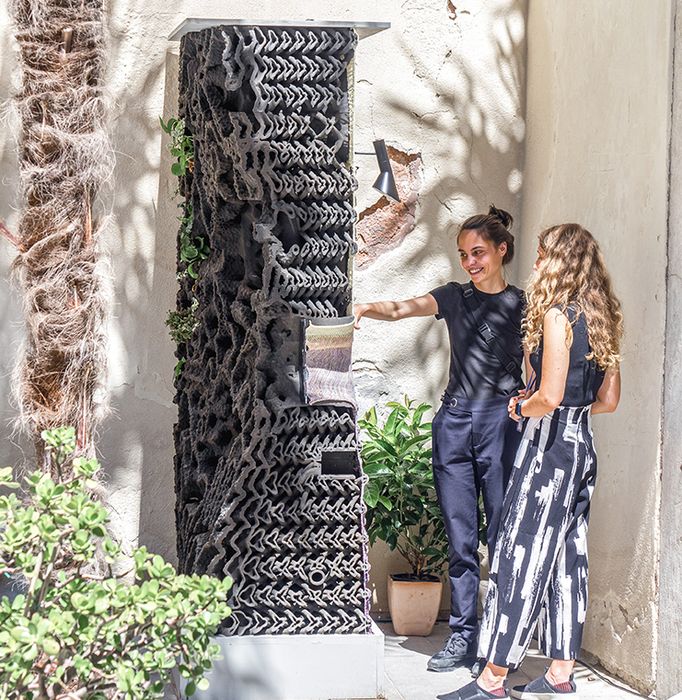
The wall is not only geometrically complex, but it provides quite a number of practical functions:
- Structural support of self-weight (could be extended to carry additional load)
- Integrated electricity and light fixtures using industry standard equipment
- Integrated water pipes using industry standard equipment (PEX tubing)
- Windows
- Distributed ventilation system controlling heat storage and internal moisture levels. Embedded actuators and sensors for control, without moving parts
- Rainwater run-off
- An exterior wall zone that acts as a diverse wildlife habitat
- Air filtration
- Interior fabric surface
The resulting design was able to achieve all this value, demonstrating the extreme capability of 3D printing technology when pushed to the absolute limit. Traditional design would have required separate components for many of these functions, yet here it’s possible to combine them all in one design.
The two-year project to design and produce the 1250 x 2100 x 700 mm object required the collaboration of Sandhelden, who previously has been awarded our Design of the Week, and voxeljet, who provided the 3D printing equipment for the job. Specifically, a VX4000, one of the largest 3D printers available, was used for the print.
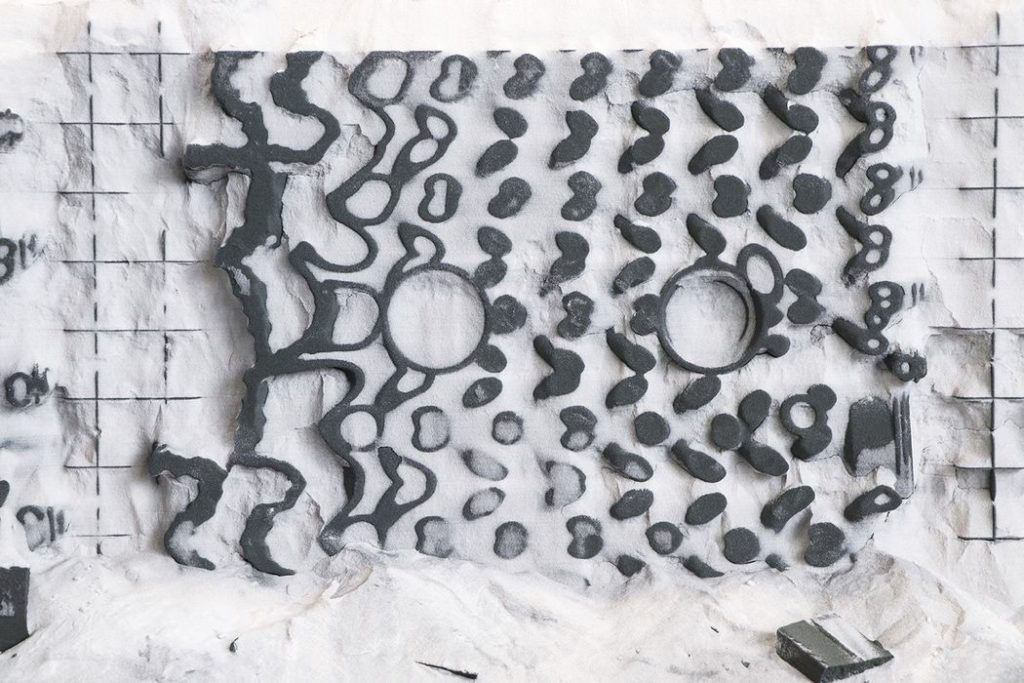
voxeljet product manager Tobias Gruen explained how the print was made:
“The main challenge for us was the high degree of complexity with the fine inner structures and tubes. Since we print in a sand bed, this means, that after the printing process is completed, we have to remove all the unprinted sand from the bonded structures. So, when we print structures with cavities, that means they are always filled with unprinted sand. To ease up this unpacking and finishing process we printed 21 individual pieces which made the finishing and handling of the parts much easier. The data was sliced by David and Ana at the suitable intersections so that the parts could later be assembled. For us it was a great experiment to explore how thin we can print and handle the filigree structures. With this project we really tested the boundaries of complexity for our technology.”
The sand 3D print produced by voxeljet was then infused with an epoxy resin to provide hardness and durability.
This project is quite unique, but it shouldn’t be. It shows how a complex design can be achieved using 3D printers that have been available for years. The implication here is that the missing element has been design, which the two architects have clearly demonstrated.
Via Sandhelden and voxeljet