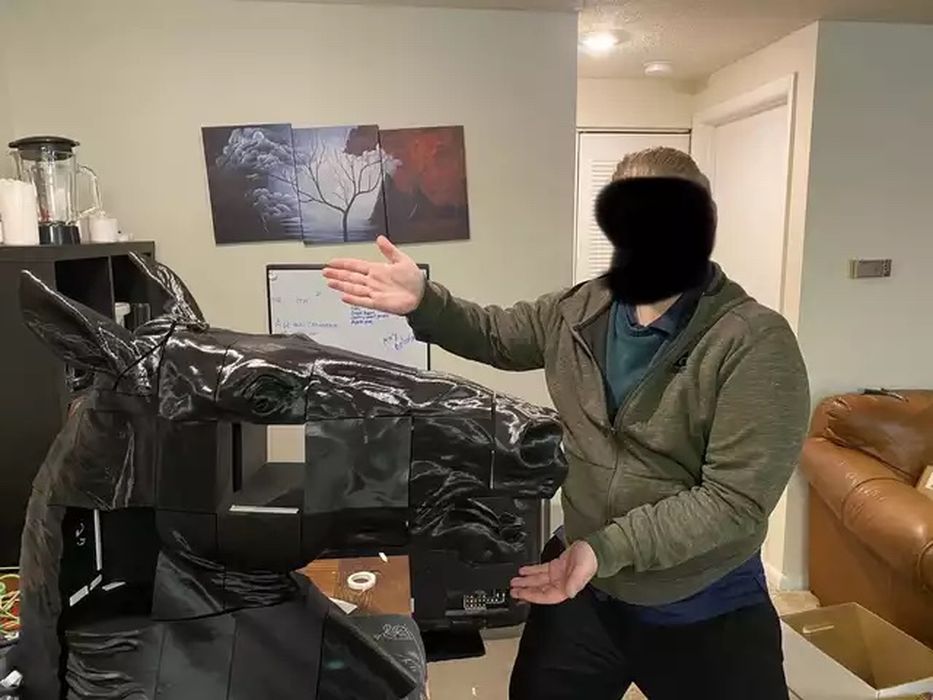
This week’s selection is the Life Size Horse Head by Reddit contributor thepyrodex.
This is a pretty unusual 3D printing project, and one that calls for endurance. thepyrodex certainly has that, as the effort required includes a monstrous amount of 3D printing.
The project was to produce a life-size horse head for a parent. Why do this at all? thepyrodex explains:
“I’m making it for my Dad as he loves to do Cowboy era re-enactments and wanted a prop for a stage that had a full horse head sticking through a window for it and for other uses as a prop later. Also it’s his birthday present. Also I’m stupid and stubborn so once started I’m gonna finish it.”
The approach was to take a “normal” horse 3D model and scale it up to “horse size”. But what exactly is that size? thepyrodex ended up learning more about horse biology:
“I didn’t quite understand when I started, I just took the file and scaled it to the size of a real horse using “average” size specs for horses found online. Also learned that most people are used to ponies and this is the size of a larger horse/plow horse.”
Once scaled, the horse head 3D model was sliced into chunks 3D printable on an Ender 3, the production tool for the project. Evidently thepyrodex did this manually using Microsoft 3D Builder, an incredibly tedious task. thepyrodex should have used a specialized tool for chunking large models, like Luban, which we covered a few years ago.
While this enormous project is still in progress, thepyrodex offered some statistics on the work:
”I’m printing it at 3 walls, 5 top/bottom layers, 5% infill using lines. I’ve currently used about 11 spools for this but only about 8 KG of material as I’ve had a few failed pieces from snapped filament on one, or not paying attention to spool level and having a run out (damn run out sensor didn’t trip) Im planning to weight it at the end and find out total amount in it.”
They’ve been using “off-brands” to lower the cost of filament, which is totally understandable. But that can lead to print failures if crappy filament is put through the machine.
3D printing large objects in this manner is very challenging, not so much due to the printing itself, but rather the endurance required to keep running jobs, day after day. I’m always impressed with anyone that attempts an ultra-large project and succeeds.
This is an ambitious project, and I’m interested to see the final piece, once printed, assembled, glued, sanded and painted. Whew, that’s a lot of work when you think about it.
Via Reddit