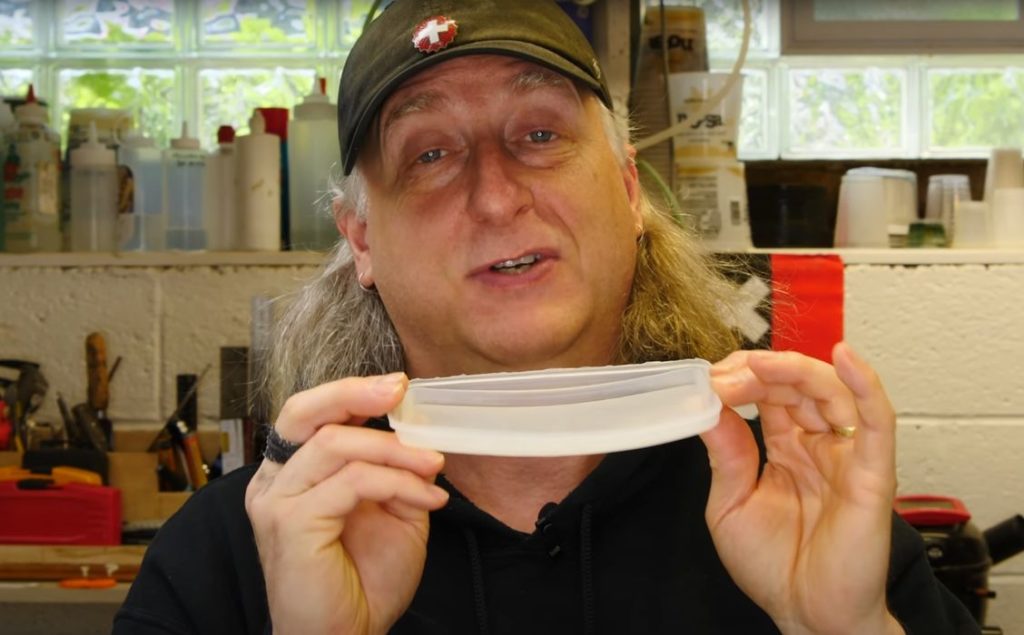
This week’s selection is the Collapsible Silicone Container by YouTuber Eric Strebel.
Strebel is a professional maker often building unusual projects for clients, and many of his endeavors are published online in short explanatory videos.
Strebel’s primary activity is producing molded objects, very often using 3D printed molds. While he’s clearly an expert at this process, his most recent project almost stymied him: making a collapsible silicone container.
Apparently a client requested a silicone object that could collapse down into a much smaller volume when not in use.
Easy, Strebel thought. Just make a two-part mold and cast some soft silicone. The softness of the material would easily allow the object to fold up.
No.
That’s not what happened. The cast container retained its “open” position and would not collapse unless forced, upon which it would expand automatically.
Strebel thought perhaps a software material would help.
It did not.
He then embarked on an epic iteration sequence in which he tried many different combinations of material and part design variations. After literally dozens of attempts, Strebel managed to figure out how collapsible silicone containers can be successfully made.
The answer turns out to be a very precise form of mold design and an unusual post-casting technique that Strebel realized would help the process. I won’t give away the details, but I encourage you to watch his fascinating video.
At each iteration, Strebel had to 3D print new variations of the mold after redesigning it in Autodesk Fusion 360. While the number of iterations here — and the many days involved — may seem extreme, it really isn’t.
It demonstrates the value of iteration, and of course persistence. Knowing that such collapsible objects do exist, Strebel fought through designs and materials to arrive at a successful conclusion.
The next time you are designing a 3D printed part, remember the value of iteration. It will work the next time, I promise!
Via YouTube