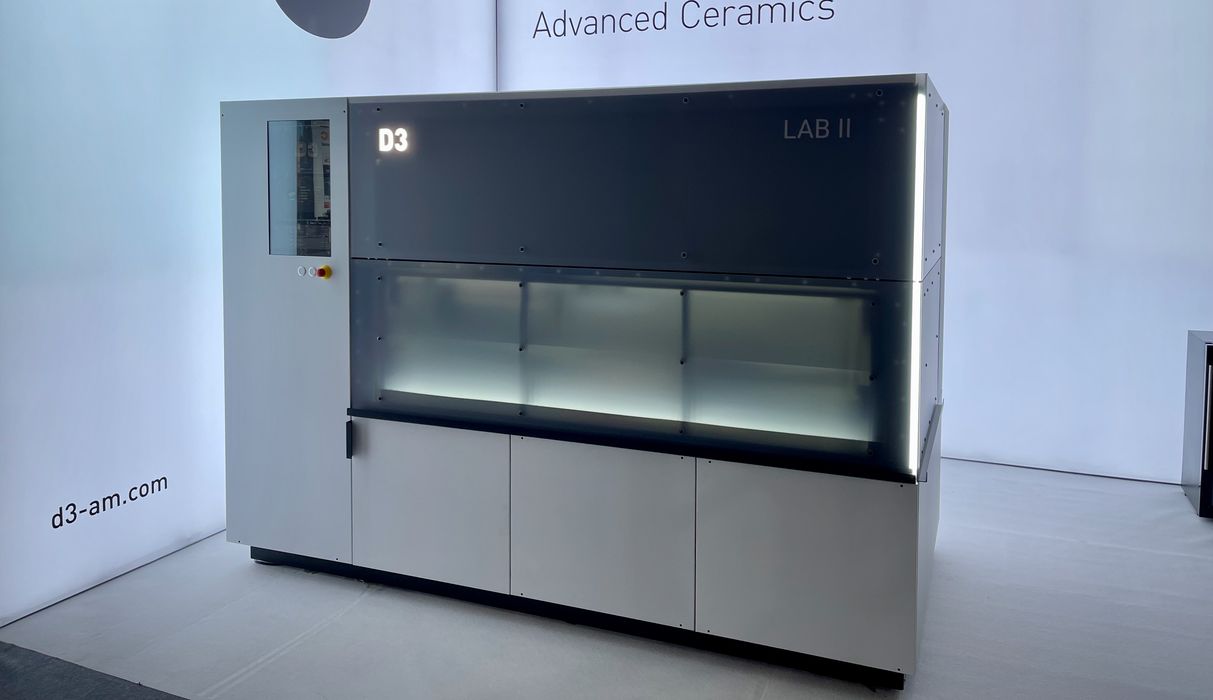
D3 is a new company producing an unusual industrial ceramic 3D printer, the Lab II.
You may not have heard of the company, as they are quite new. However, they’re not exactly a startup. Instead, they are a member of the Durst Group, a large Italian operation that began business decades ago producing printing products. Today the company produces a wide range of industrial inkjet devices, and recently decided to get into the additive manufacturing market by launching D3.
Their 3D printing process is called micro particle jetting, or “MPJ”. It uses a specialized inkjet printhead, no doubt derived from the company’s vast experience in that area.
The material is a custom mix of plain water, ceramic particles in suspension, and a tiny bit of binder. D3 representatives insisted there is “nearly no binder!”. It’s a “water paste”, as they describe it.
The printing process involves swinging the inkjet printhead over the print surface, selectively dropping material.
They didn’t explain to us how support materials work, but I presume there is a second material that is ink-jetted in non-part regions that will be removed later.
That’s quite similar to binder jet systems from other manufacturers, but then there’s a difference.
Most binder jet systems require tricky chemical and/or heat treatments to remove the binder from the green part. Here that’s not required because, remember, there’s “nearly no binder!”.
Instead the green part simply requires a “few hours to dry”, and then it can be sintered in a furnace to solidify the part. Essentially D3 is printing a brown part right away, and skipping the green step entirely.
They told us the printhead can print voxels of size 0.063mm, which enables very detailed resolution. The Lab II’s build volume is apparently 500 x 240 x 120 mm, enabling the ability to produce rather large parts.
The technology appears to be quite scalable, as one would only need to stretch the machine to expand the build volume. It is also quite fast, because inkjet printing is a well-established technology that can work very quickly. This means that the Lab II could very likely be a production-capable device.
The water paste approach is being used for ceramic materials by D3 at this time. It seems to me that it could also be used for metal printing, but D3 told us they are focusing on ceramics at this time. That’s likely because there are few ceramic solutions on the market, while the metal printing space is quite competitive. That’s a good strategy for a new 3D printer manufacturer.
The parts we saw were quite good and exhibited excellent quality.
The huge build volume of the machine should enable manufacturers to produce highly unusual large ceramic parts for industrial applications. However, it may be that this tech is so new D3 will have to spend time with manufacturers to identify these new applications.
Via D3