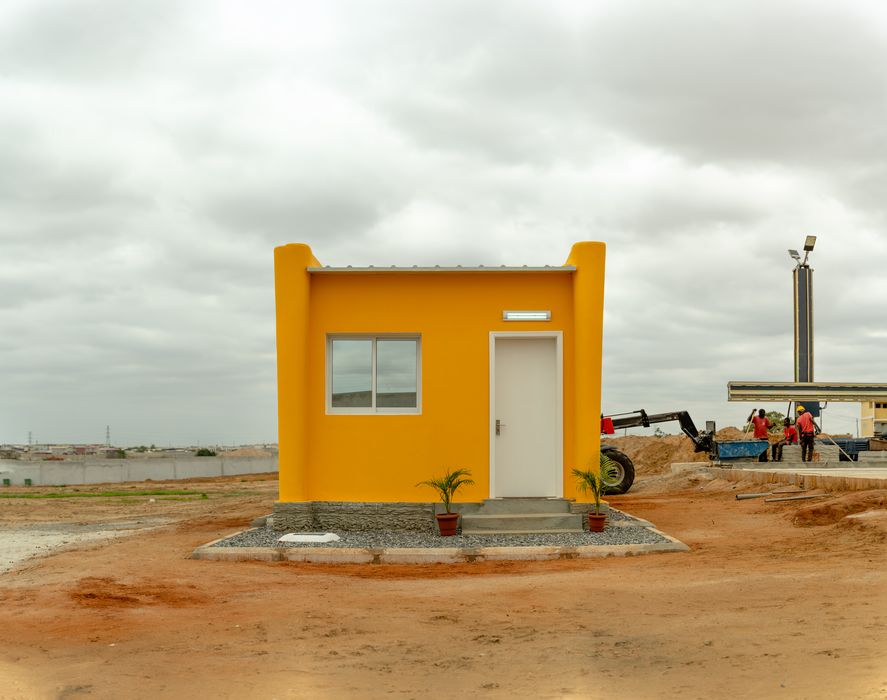
COBOD announced a breakthrough material that could revolutionize the use of construction 3D printing.
Construction 3D printing has been around for several years, but mostly on an experimental or demonstrative basis: projects can be expensive to complete, and have often been subsidized one way or another. It’s been unclear to me whether there is a financial advantage to using 3D printing for the production of building walls, foundations and floors.
There is a reason for this, and it has to do with the materials used. Like polymer 3D printers using the FFF process that tune the materials and extrusion mechanism to ensure proper material flow, the same issue affects construction 3D printers extruding concrete.
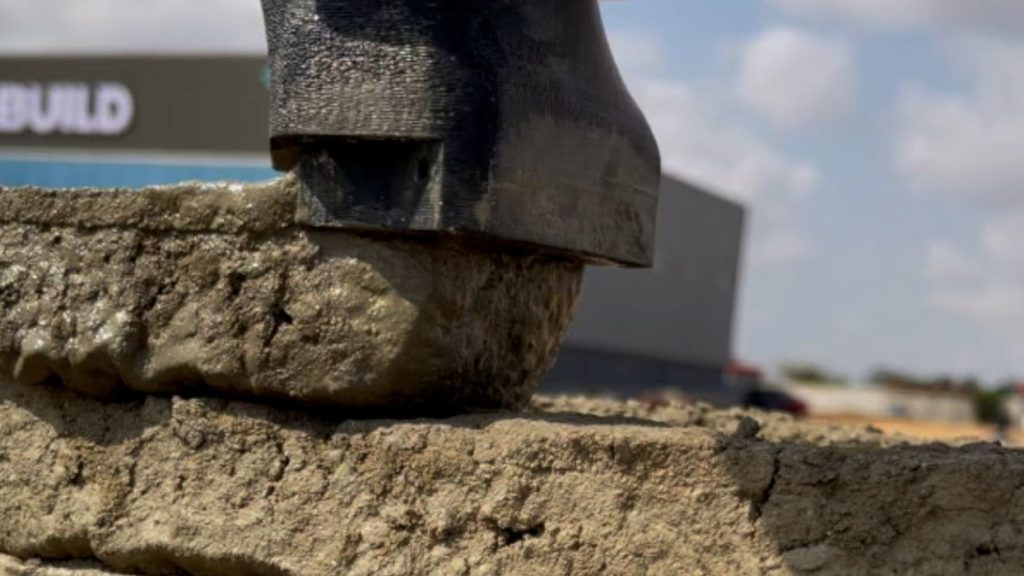
It turns out that common concrete is difficult to extrude for a variety of reasons. Because of this, most concrete extrusion systems actually use dry-mix mortars rather than the usual concrete mixes. These allow smooth flow of material, which is critical when the CNC-controlled gantry moves the extrusion head around. As FFF 3D printer operators would know, interruptions in material generate gaps, blobs and other effects that can ruin a 3D print.
Now imagine a fault of that type when you’re half-way done a three story building print. It’s not as easy as pulling the print off the plate and throwing it in the trash when it weighs many tonnes.
COBOD worked with CEMEX, a large construction materials company on the problem. They developed a new product called D.fab, which allows ANY common concrete to be 3D printed successfully. Here’s how it works:
“The solution from CEMEX and COBOD consists of a system of admixtures, where specific chemicals are introduced at the batching plant and designed to make the concrete fluid and easy to pump. Whereas another admixture, which speeds up curing, is added through the dozing unit at the printhead of COBOD’s printers and makes it possible for the concrete to gain shape instantaneously and buildable. The solution only requires central sourcing of less than 1% of the concrete mix, while more than 99% of the concrete can be based on local available raw materials including the cement, which can come from any cement maker, leading to very significant cost savings compared to 3D printing mortars.”
Why is this important? It’s because the dry mix materials tend to be 5-10X as expensive as regular concrete. This alone puts the price of construction 3D printing out of reach for many projects. It’s also a reason why most construction 3D printing projects are single buildings and not entire neighborhoods.

COBOD and CEMEX partner Power2Build tested D.fab in a project in Angola, where they successfully 3D printed the concrete portions of a 53sm (570sf) house near Luanda, shown at top.
Founder & General Manager of COBOD International Henrik Lund- Nielsen explained the cost effect of the new material:
“When we began 3D construction printing back in 2017, where we 3D printed Europe’s first 3D printed building, we made the concrete recipe ourselves. We had to use a lot of cement to get it to work, with the consequence that our recipe was too expensive and not CO2 friendly. While we have been happy to help various cement and concrete manufacturers develop dry mix 3D printable mortars, we have also insisted on that a solution for making real concrete made from local available materials would be needed for mass application of our technology. We are more than pleased that CEMEX took on the challenge, and proud that we in cooperation could develop the new solution. Prices for materials will come down from the typical 700-900 Euro/m3 for 3D printable mortars to now 60-90 Euro/m3 depending on geographic location. This is equivalent to a reduction in cost of materials of about 90% and is truly a game changer for our industry and the construction industry globally.”
It is unclear which construction 3D printing companies will have access to D.fab. It may be that COBOD has exclusive rights, or it could be that CEMEX will sell the material to any firm.
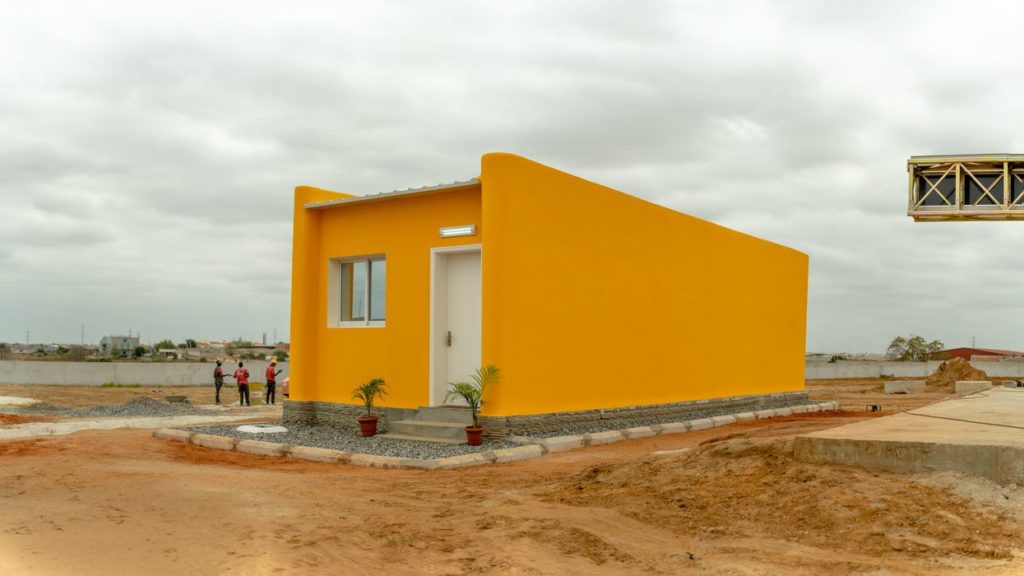
Nevertheless, this is a very important development, as it opens the door to widespread expansion of construction 3D printing. The technology certainly saves on labor, as the machine does a lot of the work, and now there are savings in materials as well.
In the construction industry, cash is king, and the king has spoken.
Via COBOD, CEMEX and Power2Build