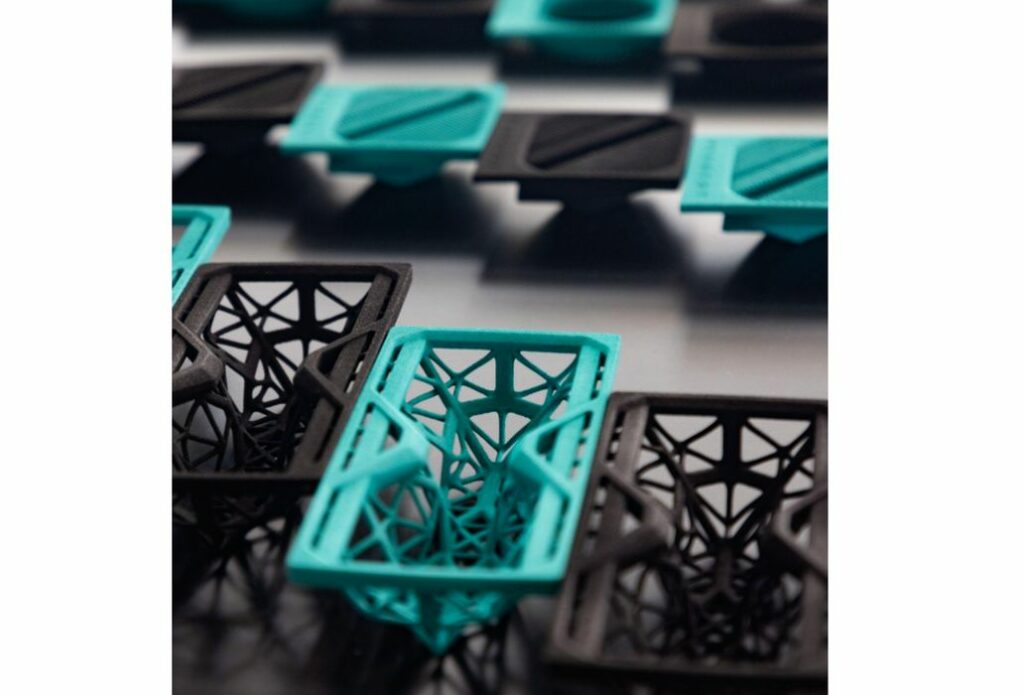
Mass personalization and customization could be the catalysts for industrial change and the adoption of 3D printing for production.
The story of product development has long been the idea of prototyping until a product was ready for production. And production meant making as many pieces as possible while spending as little as possible to provide your business or invention with a healthy margin.
In the world of manufacturing, this is known as low-mix, high-volume. The older methods of manufacturing were about finding the middle ground between achieving mass production and retaining quality. As technology changes and manufacturing methods adapt, so does the market.
It’s definitely the chicken or the egg scenario when exploring which came first, market demand or product innovation, but it can’t be denied that production has to adapt regardless. Currently, market demand has trended toward the opposite of the low-mix, high-volume production of the past. Mass personalization, or high-mix, low-volume production, is slowly overtaking traditional methods of production and will continue to do so thanks to automation and additive manufacturing.
3D Printing for Production Is Just Taking Hold
Additive manufacturing technology was first developed over 30 years ago. Since then, the technology has found its way into many industries and niche markets, but it has never really been a force of change for real manufacturing or production—until recently.
Several roadblocks have slowed the adoption of 3D printing for production. Much of the challenge has been part quality, precision, or time for production. The additive manufacturing industry is slowly changing the way industries think about this method of manufacturing.
While a few early adopters and enthusiasts have recognized the value of additive manufacturing, the recent COVID-19 pandemic set the wheels in motion for a number of companies. Supply chain disruption and a changing workforce helped mobilize the digital manufacturing community, and many companies were forced to recognize what 3D printing could do.
Wayne Davey, HP’s global head of 3D Printing Solutions Go-to-Market, says, “The past two years the traditional supply chain has left many industries frustrated when they were unable to move goods quickly.”
Developing new supply chain strategies using advanced 3D printing solutions is one way to accelerate the transformation, making the traditional supply chain more efficient and flexible. Davey used Nissan as an example because the company is using HP’s technology to produce 3D-printed replacement parts for older cars. Leveraging what it is learning by creating parts for older cars will help inform future design and development with additive technologies.
Mass Personalization Is Driven By Data
As products become easier to make, personalization or customization can begin to take off. With tools like production-capable 3D printers, we are no longer relegated to fitting into a box that is restrained by manufacturing techniques. Organic shapes are the bane of any machinist and/or require machine tools that get exponentially expensive as you add more degrees of movement. Additive has been the answer to fill that gap, but only recently has it emerged as a viable production tool.
Davey says, “3D printing is about more than simply competing for cost and speed optimizations of the same product. The true potential of 3D is realized when engineers can develop products which cannot be manufactured today, by taking advantage of rapid prototyping and translating them into full scale production of final parts using data-driven insights.”
Because 3D printing excels at high-mix, low-volume production, the data-driven design can be truly harnessed. With 3D printing, unique geometries and nested structures can be created with ease, meaning parts can be truly unique to their function.
We’ve all experienced the frustration of trying to find a nut to fit an odd-sized bolt. Maybe you’ve had to special order components to fit that take ages to arrive. Combine those frustrations with the supply chain challenges experienced during the COVID-19 pandemic and you have a recipe for a burned-out engineer, a terrible product, or both.
In this sense, additive can provide customization opportunities. In the past, those opportunities often resulted in frustrations again when moving from prototyping to production. Now that the capabilities of 3D printing are becoming more realistic for real manufacturing, it opens the door to product development that we’ve never seen.
Davey adds, “A great example of this is HP’s partnership with Cobra Golf and Parmatech, where a first of its kind, limited edition, 3D-printed putter is being manufactured commercially using HP Metal Jet. The KING Supersport-35 putter features a thin exoskeleton braced by lattice beams—entirely different from traditional putters made with solid chunks of metal.”
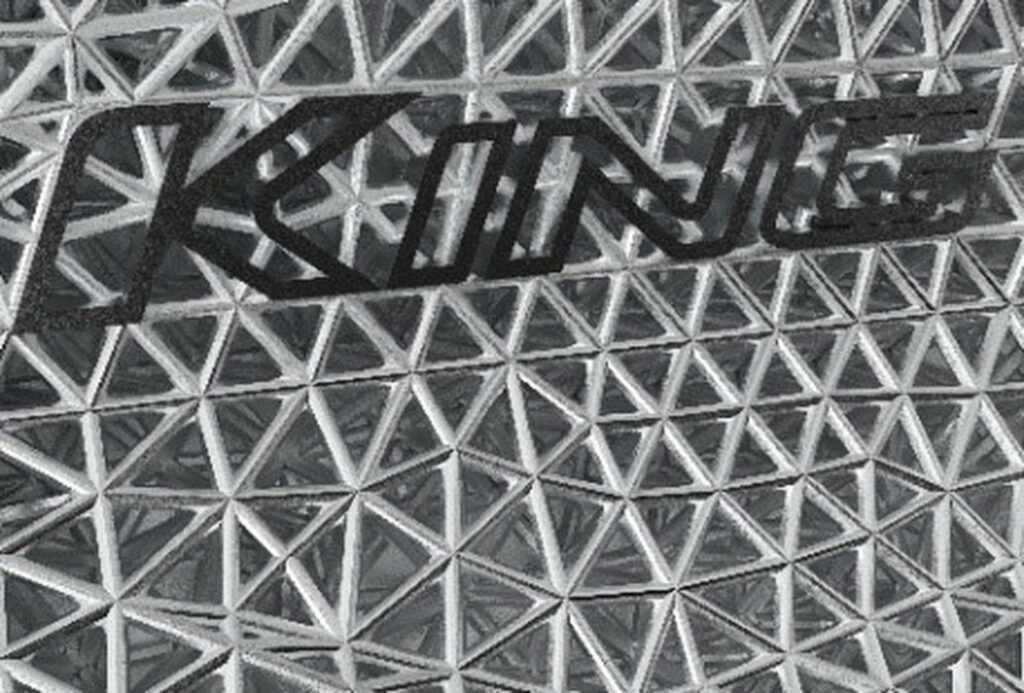
Cobra Golf is, in fact, using 3D printing for three oversized models in a product line called the King 3D Printed Series. The additive technology allows the company to create a nylon lattice cartridge to optimize weight distribution for high “moment of inertia” and stability.
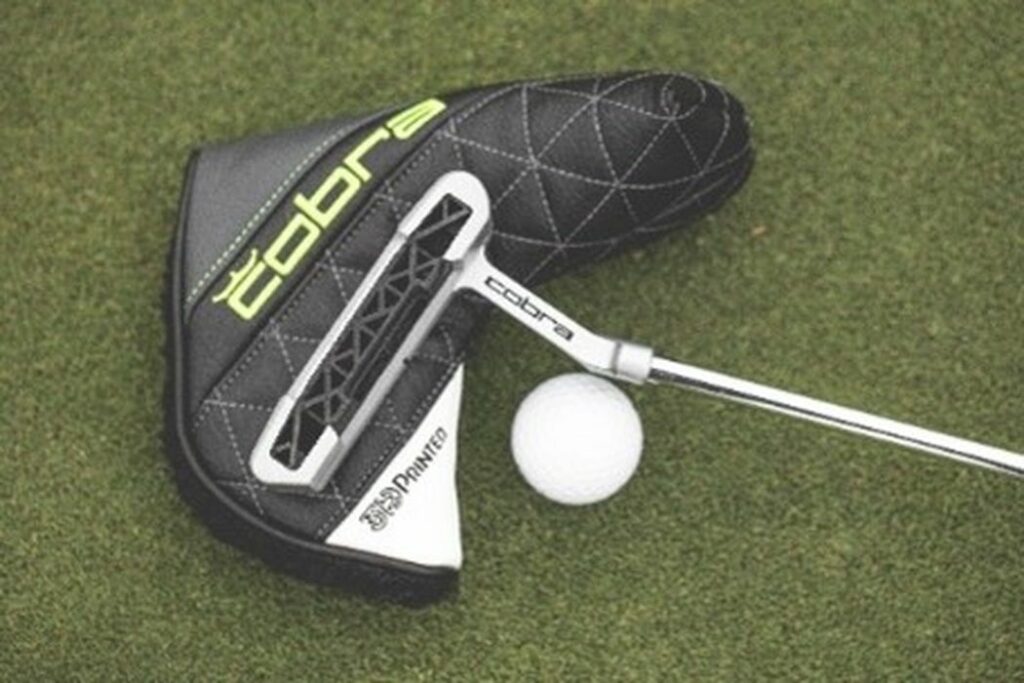
HP is working to leverage data to create a better understanding of design and market needs, which the company believes will lead to technology that makes it easier to apply machine learning. This concept will allow designers and manufacturers to gain a greater understanding of the part lifecycle as well as the end user, which will lead to better parts with improved design. “The entire end-to-end lifecycle, from supply chain to the useful life of a part, will be streamlined with the ability to analyze and leverage insights in a manageable, automated way,” Davey says.
Read the rest of this story at ENGINEERING.com