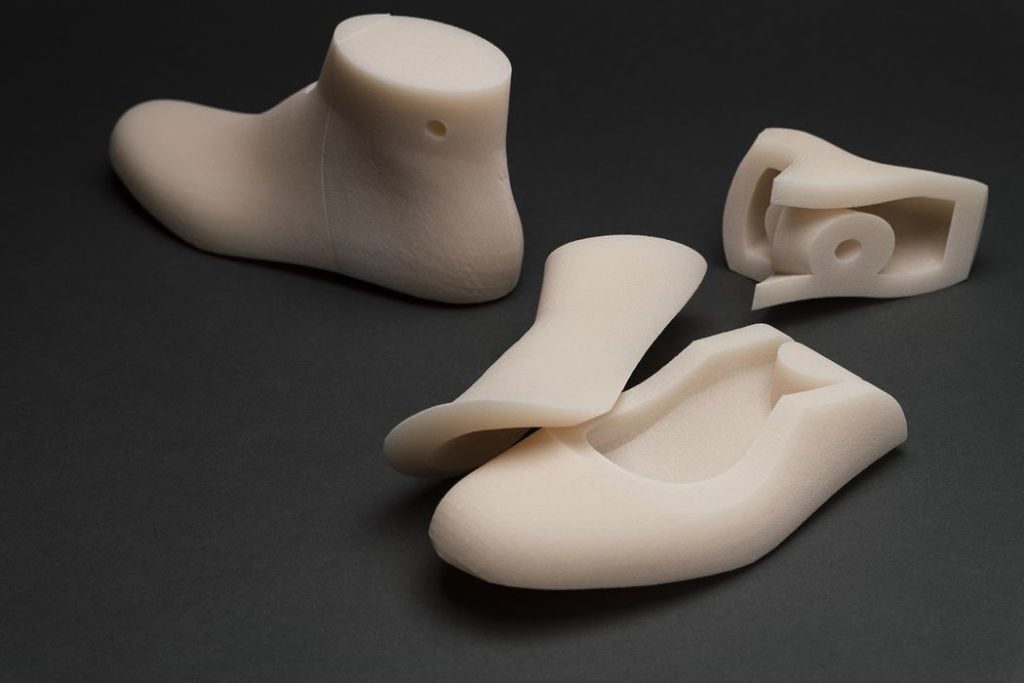
A collaboration between multiple providers has created a way for shoemakers to quickly produce customized shoe lasts.
A shoe last is a 3D representation of a foot, and is used by shoemakers and manufacturers for production of custom footwear. The components comprising the shoe are wrapped around the last, ensuring they end up in the correct shape.
Lasts must be made from strong materials to withstand the mechanical forces of production, and also must maintain their geometry when exposed to wet materials, like leather, during production. For this reason traditional lasts were made from metal or strong woods.
Lasts are also used by shoemakers during shoe repair activities, and sometimes even by consumers as a means to maintain the shape of a shoe while in long-term storage. I think I have a couple in my closet doing that right now.
But these days customization is the rage, powered by the automation of 3D printing. An increasing number of consumer products are leveraging 3D printing to create products uniquely designed to fit the buyer and no one else.
We’ve seen this approach used in several areas, including prosthetics, footwear and eyewear, and now there’s another application for shoemakers: custom made lasts.
However, producing such an item is much harder than you’d imagine. There are multiple steps involved, including capturing a suitable 3D scan, generating a useful 3D model, printing and post-processing the model, and finally shipping to the client.
Those tasks were recently taken on by a collaboration between several 3D industry parties: PROTIQ, Forward AM and trinckle. Each had a specific role in the solution.
PROTIQ is an additive manufacturing service providing an online marketplace for industrial products, as well as general 3D print services. They operate a wide range of 3D printing equipment, including devices from EOS, Farsoon, RICOH, 3D Systems, Formlabs, Photocentric, DMB, Stratasys and even some of their own design.
trinckle is a German firm that has developed sophisticated software engines to generate custom 3D models from input data and parameters. While they don’t do the 3D printing themselves, they can produce unique 3D models for given industrial scenarios.
Forward AM is the 3D printing solutions arm of BASF. They work with clients to help determine additive solutions, including selection or even development of new additive materials.
These three parties together brought enough expertise to solve this challenge. BASF’s Forward AM provided a new powdered TPU material for SLS 3D printing that matched the characteristics required for the lasts. PROTIQ explained:
“The key to this is the TPU plastic, which on the one hand offers the required properties of wood, and on the other hand is elastic, has a firm hold and is extremely light.”
The 3D model generation component was provided by trinckle, whose Paramate system did the job. This software has been used to create custom 3D models for several applications in other areas, such as copper heat exchangers or robot grippers.
Finally, PROTIQ provides the actual production element of the sequence by 3D printing the models on their SLS equipment.
You can try out the custom 3D printed last system yourself. You may not happen to have the necessary DinA3 or DinA4 foot scan data handy, but they do provide sample data so you can see how the process works.
For shoemakers and shoe manufacturers this service could be of great interest because it can produce effective lasts far faster than can be done using traditional approaches. While digital production has been around for a while, few shoemakers have the necessary 3D software or skills to produce last models. The new PROTIQ system cuts out all that complexity and transforms the process into a few button touches.
I’m interested in this type of collaboration because it brings 3D technology to users in a way that allows them to succeed. It makes no sense to hope for “everyone” to use 3D printing; it’s simply too hard for most people to do. We need more solutions of this type where industry and consumers can access the technology in an easy manner.
Via trinckle, PROTIQ and Forward AM