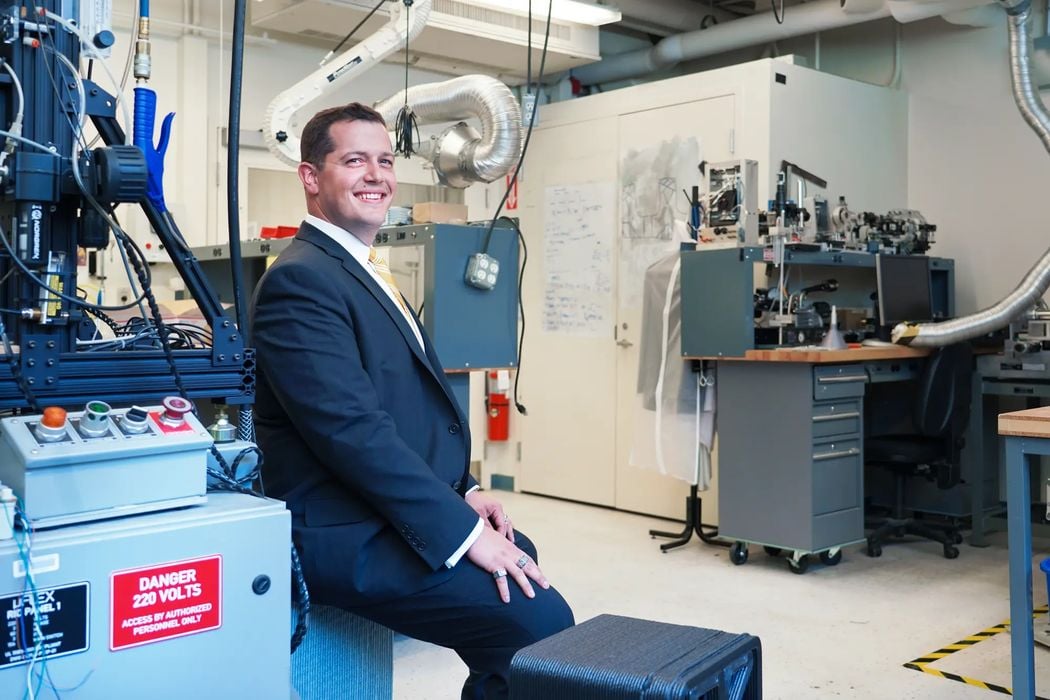
Charles R. Goulding and Preeti Sulibhavi chat with Dr. AJ Perez, a distinguished MIT-trained engineer, entrepreneur, and sustainability advocate.
Dr. AJ Perez, a three-time MIT engineering graduate (SB ‘13, MengM ‘14, PhD ‘23) and recipient of a Sustainable Design Fellowship issued by the Morningside Academy of Design, refers to himself as a lifelong learner. In addition, his team was awarded the Chandler Fellowship to pursue innovative research at MIT aimed at improving the health of our plant. He also holds the distinction as the first PhD at MIT to complete the Sloan School of Management Sustainability certificate program. Dr. Perez is an experienced industrial tech entrepreneur and an impact investor holding a FINRA series 65. We have also covered IndustrialML, which AJ founded and served on the Board of Directors, previously in our interview with Dr. Perez’s colleague and collaborator, Arjun Chandar.
Dr. Perez, or AJ, as he preferred to be called during our interview, has set a goal of helping to solve the global housing crisis in a sustainable and globally equitable way. For this interview, AJ spoke from his experience as a Research Scientist at MIT.
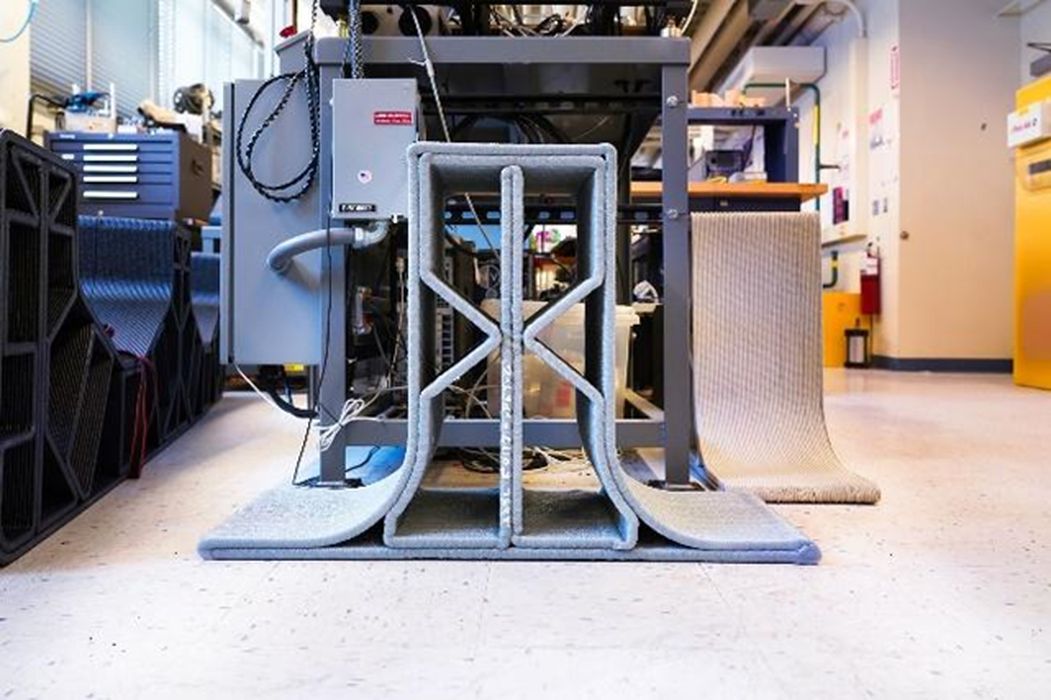
About a decade ago, the UN found that nearly 1.6 billion people lacked adequate housing, globally. That number is larger now, closer to 2 billion. What makes distributive manufacturing using recycled plastics unique is that it brings what is abundant in supply to the demand.
Instead of establishing a select number of large manufacturing facilities in certain pockets of the world that produce large amounts of products and parts, and then distribute them globally to various regions, AJ believes that distributive manufacturing can create smaller, more localized manufacturing sites that use local resources and employ local people.
In the last few decades, plastic has followed humans around the world. To many this recycling conundrum is perceived solely as a pollution problem; but, to AJ, this presented an opportunity to “mine waste.” Plastic waste can be used as raw material for 3D printers to build houses for people in the Caribbean, Southeast Asia, and South America, places that could particularly use the housing infrastructure.
A building has three main components: lighting/electrical, HVAC/mechanical and the structural building envelope. These can be fabricated, component by component, locally.
We have covered companies like Cemex and ICON that 3D print housing with cement, but that involves a material that comes from the earth in certain regions that must then be transported to be used. It is heavy and cumbersome and not readily available everywhere. We have covered “green concrete,” but in AJ’s opinion, that material may reduce the carbon footprint to a certain extent but it adds to local pollution and utilizes much of the region’s scarce local potable water resources. The MIT-HAUS project (pronounced “Meet House”) has two core strategies: prefabricated modules (i.e., walls, stairs, floors, roofs, foundations, etc.) and to focus on materials (i.e., concrete for higher-end, commercial projects or recycled plastics for more economical, residential projects). The key to the success of MIT-HAUS lies in flexibility, or modularity, wherein they can focus on the entire house or even parts of the building for certain projects in certain regions.
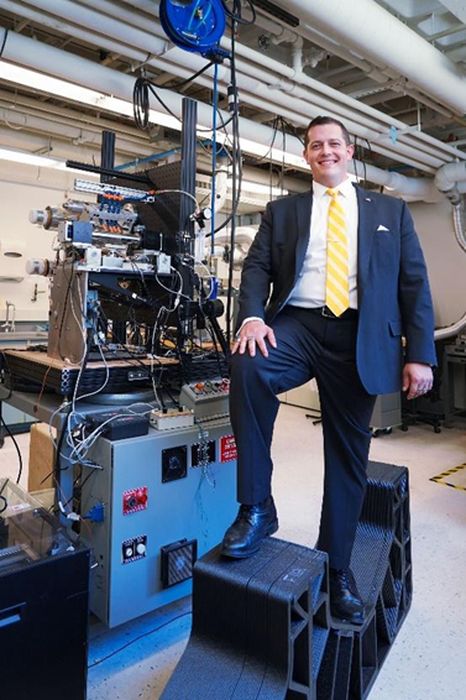
Plastic waste is not a material that must be imported or exported, it is available locally in many regions, particularly shoreline ones, it is easier to transport than cement or wood, and, it is in mass abundance globally. It makes for the perfect material to use to 3D print houses.
According to AJ, the melt-extrusion 3D printers they use to create housing infrastructure from plastic waste are akin to giant “hot-glue” guns. And while throughput is slow now (in contrast to growing demand for housing), the technology is actually there to make this a commercially viable option. The problem is that they need thousands more 3D printers and additive manufacturing facilities than currently exist. This involves more investment and capital.
AJ was clear that he did not want to detract from local economies, but rather improve them. Instead of importing 3D printing of plastic housing infrastructure, AJ prefers to use local construction industry talent and simply change the processes, materials and equipment that they use. That way there is no destruction of local construction industries and potentially, even more jobs can be created in local communities.
Plastic waste can be 3D printed into other infrastructure like roads and bridges, but AJ finds purpose in housing: a house is a home to someone, it is also an asset and improves a person’s economic standing in society. “There’s no place like home,” and the more people that can say that, the more gratification AJ finds in his work.
The Research & Development Tax Credit
The now permanent Research and Development (R&D) Tax Credit is available for companies developing new or improved products, processes and/or software.
3D printing can help boost a company’s R&D Tax Credits. Wages for technical employees creating, testing and revising 3D printed prototypes can be included as a percentage of eligible time spent for the R&D Tax Credit. Similarly, when used as a method of improving a process, time spent integrating 3D printing hardware and software counts as an eligible activity. Lastly, when used for modeling and preproduction, the costs of filaments consumed during the development process may also be recovered.
Whether it is used for creating and testing prototypes or for final production, 3D printing is a great indicator that R&D Credit eligible activities are taking place. Companies implementing this technology at any point should consider taking advantage of R&D Tax Credits.
Conclusion
There is a plastic problem. There is a housing crisis. Thanks to AJ and his team, there is a way to symbiotically approach both problems and create sustainable housing solutions around the world. According to AJ, in the next thirty or forty years, distributive and digital manufacturing methods may yield other strategies (than 3D printing) for using plastic, or other forms of waste, to create infrastructure, globally.
We have to start somewhere.