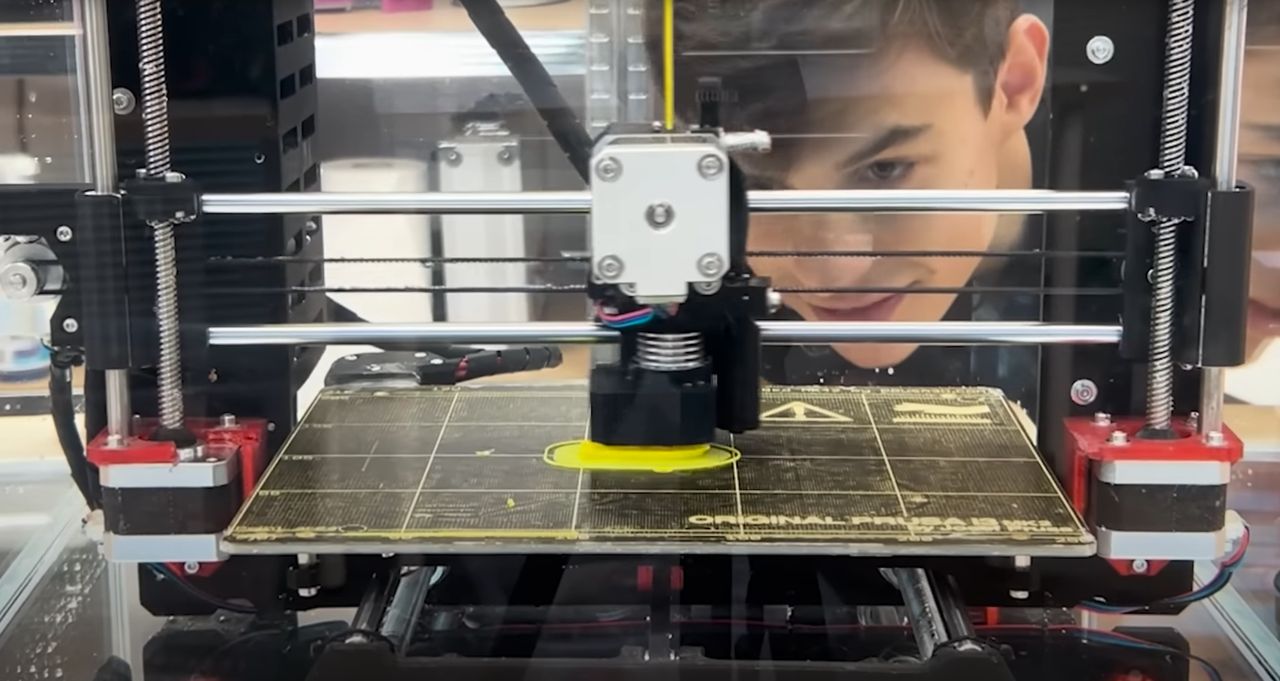
Some folks have built an underwater 3D printer — that actually works!
CPSdrone is a YouTube channel that details their experiments in building underwater drones. Many of their projects involve 3D printing, particularly for the drone housings.
Recently they published a video where they took their underwater skills to an entirely new (or deeper?) level: making a standard FFF 3D printer operate while completely submerged.
When I saw the title of this video, I was quite skeptical and expected to see a dramatic and electrically shocking outcome. But I was wrong, these guys actually made it work!
How on Earth is this even possible? Surely there will be electrical shorts, corrosion and thermal effects? What did they do to make this work?
They took a stock desktop FFF 3D printer and made a series of modifications, including:
- Motors: opened up and covered all contacts with waterproof epoxy
- Endstops: replaced with waterproof equivalents
- Heatbed: connectors covered with epoxy
- Bearings: replaced with plastic equivalents
- Display: mounted externally
- Portions of the frame: replaced with plastic equivalent
- Power supply: Placed in waterproof case and mounted externally
- Extruder: Cooling fans removed (water cools instead!)
- Hot end: Heat block sealed in silicone with a special “container” around it
- Spool: mounted above the printer to avoid getting it wet prematurely
- Controller: board sealed in box with deep coating of epoxy
At this point they had converted the device into a waterproof mode. They decided to use deionized water to ensure there was less chance of electrical issues.
The printer was placed underwater, and surprisingly, it actually worked! The print stuck to the bed, and layers were successfully deposited.
However, the life expectancy of the silicone around the hot end wasn’t sufficient, and it had to be repacked with a different high temperature silicone. They were able to print a #3DBenchy, and it came out quite well.
However, the layer adhesion was rather poor, and the prints delaminate easily. That’s because the water cooled the layers very efficiently, and subsequent layers would be deposited on cold prior layers.
They also found the underwater printer had superior performance for overhangs, which were cooled easily by the water. Bridging also worked very well.
Why do this at all? The experiment was to determine whether the powerful cooling provided by the water could offer a better solution. It seems they succeeded in the experiment, but ran into a variety of other problems. For example, prints were full of water in side the hollow interior!
My thought is that these issues could be overcome with more tweaks and modified equipment.
Their goal is to have the printer working underwater in a swimming pool, which is quite ambitious. They converted the printer into a fully wireless mode by sealing up the exterior items like the display, and went into the pool.
An unexpected issue was that the spool kept coming off the machine, likely because it was somewhat buoyant in the water and easily dislodged. They also found their silicone modifications didn’t last very long.
In all this was a worthy experiment that I don’t believe anyone had previously attempted. We now know it is possible to make underwater 3D printers, and I’m wondering if any company would take on this concept and develop a commercial version?