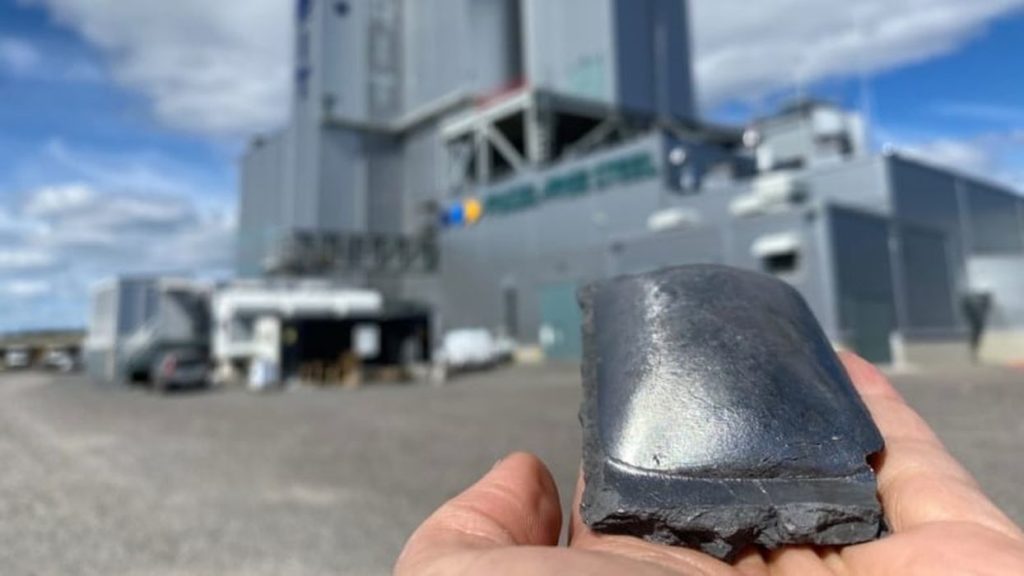
There’s been an explosion in the popularity of metal additive manufacturing, and that means more use of steel.
Steel is one of the key metals used in metal 3D printing, along with titanium and nickel alloys. Most metal additive operations use powder processes, although some use wire-based processes.
Regardless of whether powder or wire is used, the steel has to come from somewhere. Unfortunately, most of that steel is sourced using climate-unfriendly methods.
The process for making steel typically follows a time-tested process. Wikipedia explains:
“Steelmaking is the process of producing steel from iron ore and/or scrap. In steelmaking, impurities such as nitrogen, silicon, phosphorus, sulfur and excess carbon (the most important impurity) are removed from the sourced iron, and alloying elements such as manganese, nickel, chromium, carbon and vanadium are added to produce different grades of steel.”
However, there’s a catch, as Wikipedia continues:
“Steelmaking is one of the most carbon emission intensive industries in the world. As of 2020, steelmaking is estimated to be responsible for 7 to 9 per cent of all direct fossil fuel greenhouse gas emissions.”
That is a staggering amount of carbon being released into the atmosphere, and it’s because the blast furnaces often use fossil fuels for heat, and “coke”, a type of coal, is used as an ingredient. Both of these cause tremendous amounts of CO2 to be emitted when steel is produced.
The climate emergency demands that civilization keeps to a very rigid carbon budget, meaning there is a known and fixed amount of CO2 that can be released into the atmosphere before we go past the point of no return. To that end, industries such as steelmaking will have to shift into more greener processes.
That change is happening. According to a report on CBC, a Swedish company, HYBRIT, has produced the first samples of ore-based steel using no fossil fuels.
Instead of burning fossil fuels for heat, the new system uses electricity, which can be obtained from renewable sources. The process also uses hydrogen to replace coke in the steelmaking process.
The result of this process could be described as “green steel”, a product the same as normal steel, yet made entirely from renewable energy.
Certainly the first uses of the new green steel will be conventional. In fact, the report indicates that Volvo will be among the first manufacturers to make use of green steel, with prototype vehicles to be produced this year.
It’s inevitable that green steel will eventually make its way into powder form for use with AM systems. There may be powder manufacturers ready to experiment with green steel even today, and I would not be at all surprised to see an AM powder manufacturer marketing “green steel powder” soon.
This development then shifts focus to the AM operators, who, at least for the next while, will soon have a choice of using “green” or “black” powder.
I suspect some operations will adopt the new green steel materials and make it very clear to their customers and prospects that they have done so.
The magic of clean, green products will follow down the chain of production, all the way to the end user, who can then honestly state their products are made green.
Via CBC