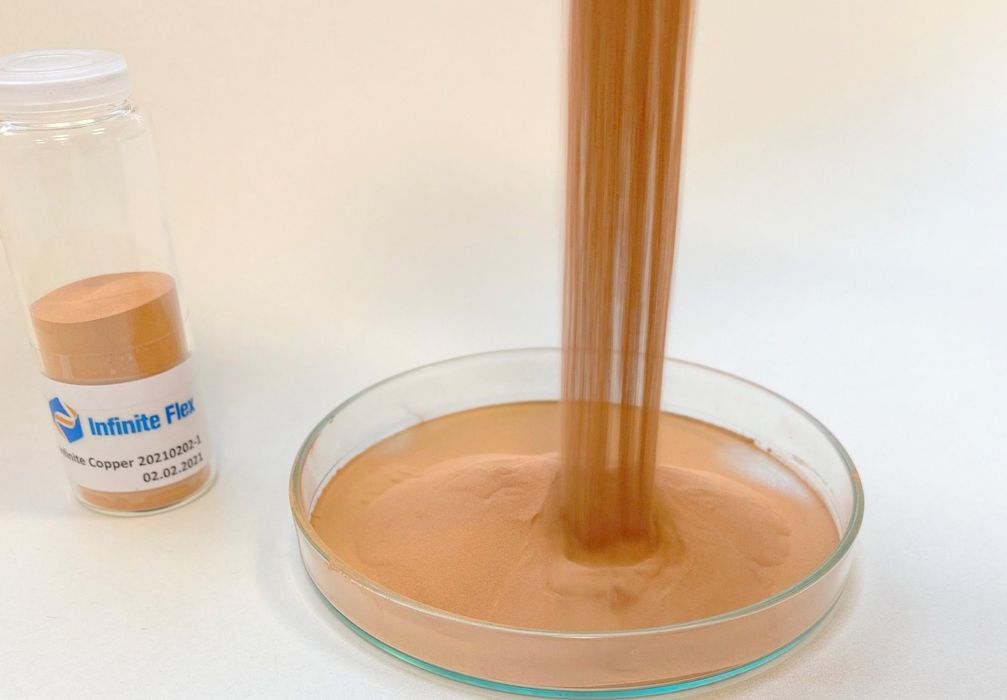
A German company announced a new copper powder that can be more easily 3D printed.
3D printed copper items are quite rare. This is because copper isn’t easily 3D printed with the most common metal 3D printing process, PBF. It turns out that copper is usually terrible in PBF systems because the thermal conductivity of copper is quite high. This causes heat to leak all over, corrupting the print. In addition, the copper tends to reflect the high energy around the build chamber.
That’s a shame, because 3D printed copper items can be extraordinarily useful in a variety of electrical, thermal and hydraulic applications that take advantage of that very conductivity.
Certain custom copper alloys have been 3D printed. However, they tend to decrease the conductivity to allow printing, but at the same time compromise thermal functionality of the printed part.
Some alternative 3D printing processes have been able to 3D print copper. For example, SPEE3D’s process uses molecular bonding at supersonic extrusion speeds can achieve this. However, that process has other limitations that preclude the production of complex geometry small copper objects.
Now there could be a change: Infinite Flex, based near Frankfurt, announced “the world’s first pure copper powder that can be easily processed in with standard SLM system.” They call it “INFINITE POWDER Cu 01”.
Infinite Flex said:
“With these outstanding properties, it is now possible to use the advantages of additive manufacturing for highly conductive copper components. High-end applications such as heat exchangers, induction coils and components in the electronics industry are now becoming reality.”
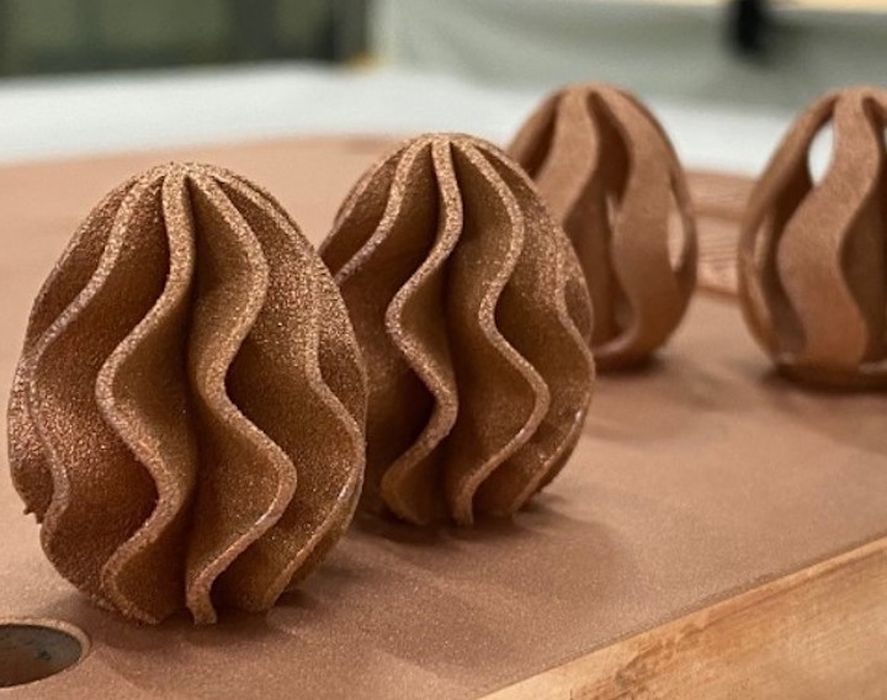
They have also apparently successfully tested INFINITE POWDER Cu 01 on two different and commonly used PBF systems, the EOS M290 and the Trumpf TruPrint 1000. These systems are used worldwide by many manufacturers and service bureaus. In addition, if the material works on these systems, it is very likely to work on many similar machines from these two providers and others.
Infinite Flex did not explain how they’ve made this material work successfully on this equipment. However, we can speculate as to what they might have done.
I suspect they produced an alloy that dampens the reflectivity of the copper to avoid one of the copper issues. However, to maintain the copper print properties, they have to retain much of the thermal conductivity in the material.
How could they have overcome the thermal conductivity problem? It is likely Infinite Flex very carefully tuned the print job parameters to minimize thermal leakage. By lowering the energy to the minimum to achieve powder fusion, it may be that use of this copper powder could take longer than other more easily 3D printed metals.
Nevertheless, the ability to 3D print objects in copper could be a very big deal. There is significant demand for highly complex copper objects that can more efficiently transfer heat, capture electrical signals and more, but there have been few ways to make these parts. At least up until now.
I’m pretty certain there will be a number of organizations testing this new copper material very soon.
Via Infinite Flex