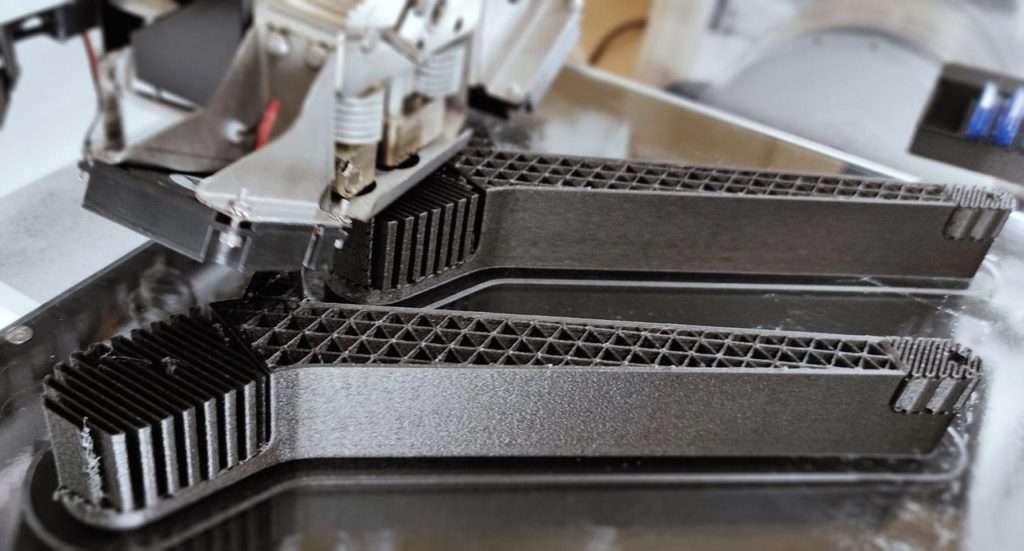
I’m looking at a new project by Anisoprint where parts for a proposed lunar rover were produced.
Anisoprint is a Luxembourg-based 3D printer manufacturer that specializes in continuous carbon fiber 3D printing. This is actually quite rare, even though you may frequently hear the words “carbon fiber 3D printing”.
Continuous Carbon Fiber 3D Printing
That’s because the most common form of “carbon fiber” 3D printing is done with chopped carbon fiber mixed in with polymers. The chopped segments must, by definition, be smaller than the nozzle diameter, otherwise clogs will occur. This composite material is significantly stronger than plain polymer prints, but is nothing compared to continuous carbon fiber.
Carbon fibers are among the strongest materials known to exist, where tight molecular bonds are made from carbon atom to carbon atom in a long series. But how could you 3D print a long fiber?
That’s the process designed by Anisoprint and a very few other 3D printer manufacturers. Basically, their equipment involves a second toolhead that can spin out and cut a long strand of carbon fiber that is laid into the polymer portion of the print.
The trick is to orient the carbon fibers in such a way as to take maximum advantage of their strength. By doing so, it is possible to 3D print incredibly strong objects — objects that are also very lightweight.
Continuous Carbon Fiber 3D Space Applications
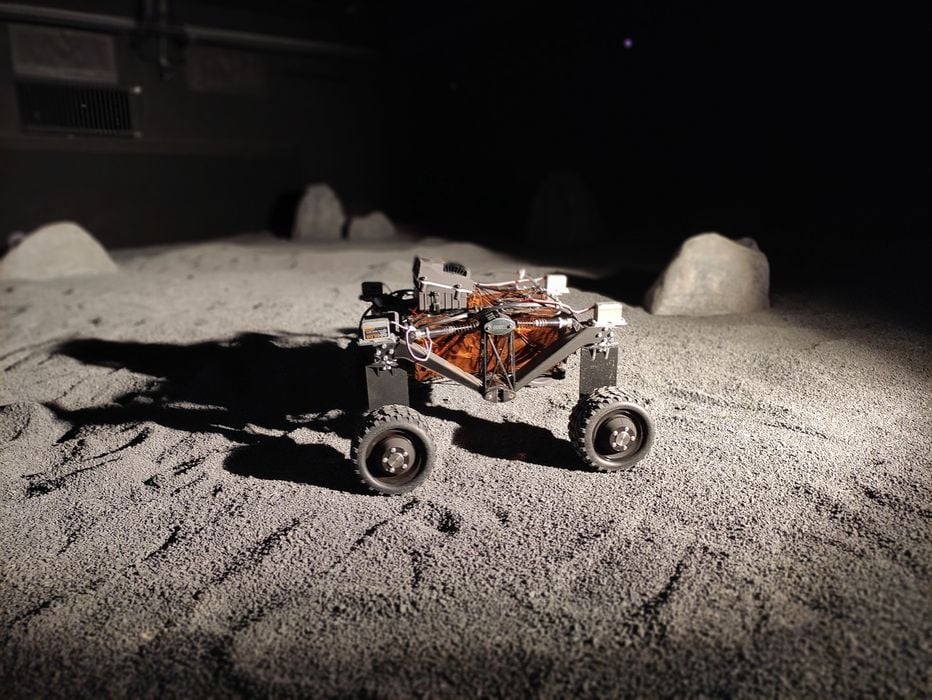
This technology was tested during a demonstration at the University of Luxembourg last week, where a student team explored designs for a proposed lunar rover.
Anisoprint explains the objectives of the project:
“The advantages of continuous fiber reinforced composites, flexible material choice, high durability and small weight, pave the way to a number of industrial uses where mass counts. Aerospace is one of such industries, as extra mass creates a lot of expenditure due to fuel consumption and many other factors. With the rover, the main challenge was to make a robot with a mass under four kilograms, and 3D printed composites was an ideal option, so the team turned to anisoprinting for light weight and high strength.”
Two parts of the lunar rover design were remodeled to enable them to take advantage of the continuous carbon fiber technology, a wheel mount and a control arm.
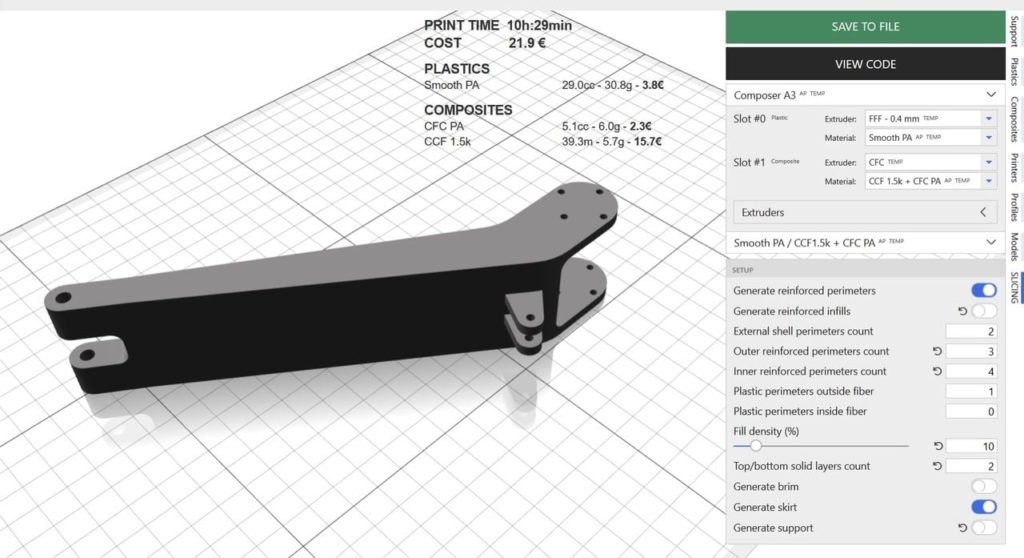
This may seem strange: why redesign a part? Why not just print it with the continuous carbon fiber? Anisoprint engineer Aleksey Ivanov explains why:
“Application cases we deal with primarily come from areas where isotropic materials proved ineffective, which means we always change the design for anisotropic reinforcement, both geometry and weight count here. Composite 3D printing has a large potential for aerospace, and we help people explore it and get maximum benefit from the technology.”
The resulting parts were impressive: the control arm weighed only 64 grams, and the wheel mount was 24 grams. Both parts used continuous carbon fiber and had only 15% infill, which would seem quite small for a mechanical part undergoing stress without carbon fiber reinforcement.
This is a fascinating experiment that may eventually lead to new aerospace capabilities.
Space applications put a very high premium on weight advantages, and the use of continuous carbon fiber could, in some cases, replace equivalent but heavy metal parts. Weight savings of that type can reduce project costs or increase capabilities by allowing the saved weight to be used for other purposes.
But weight is only one factor. Space applications must also undergo incredibly extreme environments, with huge operating temperature ranges, radiation of many types and mechanical stresses.
But at least we have started the investigation.
Via Anisoprint