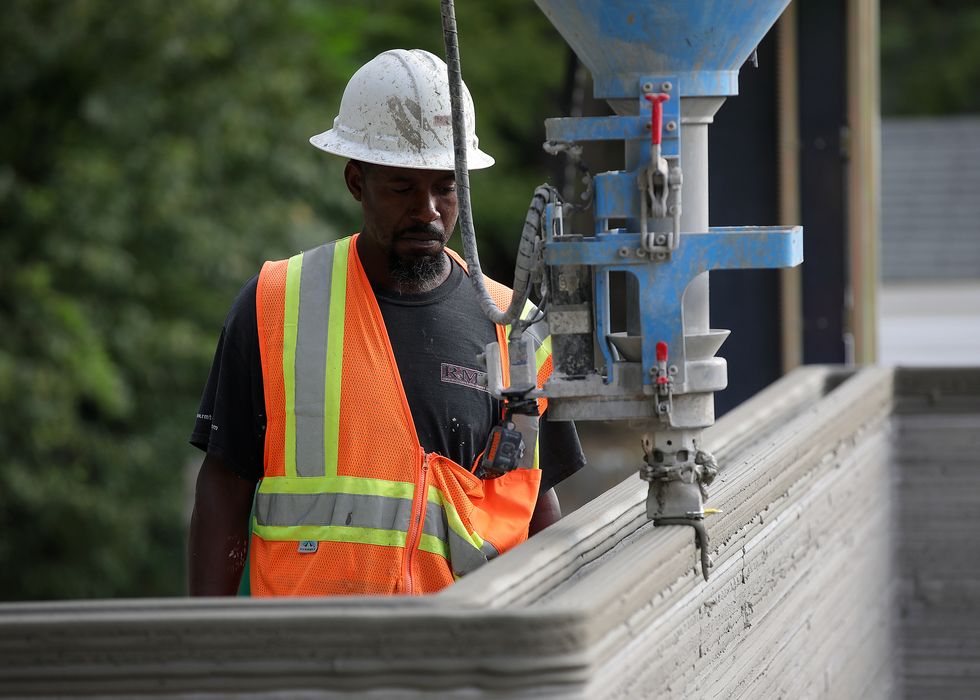
For many years, construction 3D printing has been mostly experimental or demonstrative. Now, that may be changing.
The technology involves performing precise extrusion of concrete, layer-by-layer, to form an exterior structure. It is possible to build walls in this way, and if those walls are together, you have the beginnings of a building.
I say “beginnings”, because the current state of construction 3D printing involves only the concrete portions of a build. The remaining aspects, such as HVAC, plumbing, windows, flooring, surface finishes, electrical, etc., all must be then completed using conventional techniques.
That said, the ability to 3D print concrete walls is advantageous in many ways. It’s possible, for example, to produce walls in a variety of shapes and dimensions. This is different from conventional building techniques that are often influenced by the size of standard building components. In other words, curves are easy with construction 3D printers.
Concrete is also a highly durable material that can withstand storms far better than conventional wood designs. By the way, the rising cost of wood has likely encouraged more builders to consider the use of construction 3D printing.
In spite of these advantages, construction 3D printing has yet to take off. The construction industry is very old, and it will take considerable time for it to adopt the radically new approaches offered by 3D printing.
Several players exist in the industry building their expertise and equipment for construction 3D printing. The two leaders seem to be COBOD and ICON, both of which recently announced projects.
ICON signed a deal to produce no less than 100 3D printed homes (or rather, the concrete portions of them in conjunction with residential building specialist Lennar). For this project they’ll be using ICON’s massive Vulcan II construction 3D printer.
These homes are to be uniquely designed and 3D printed for customers starting next year.
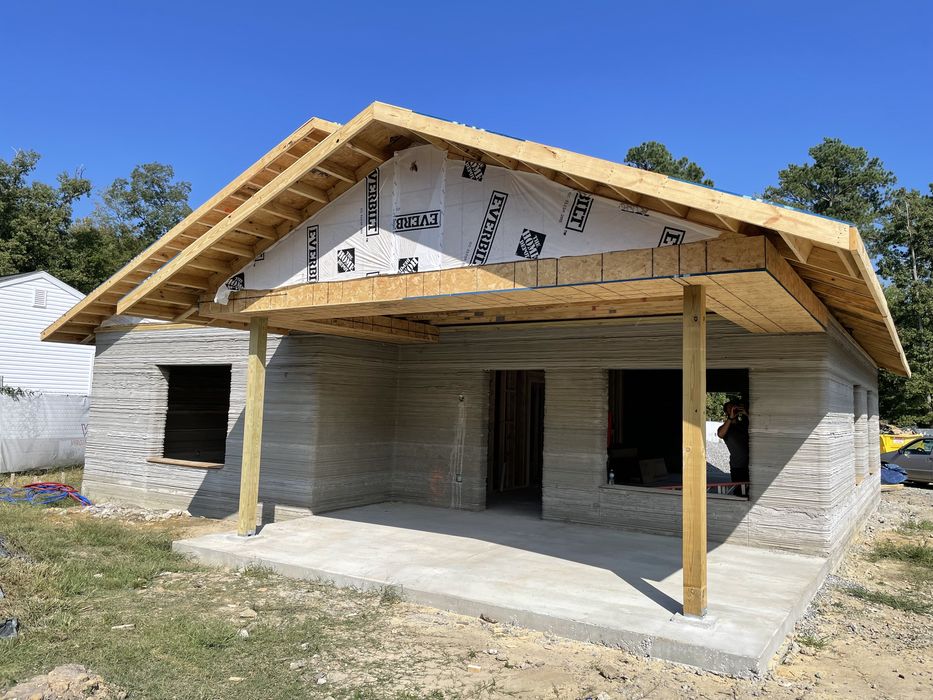
Meanwhile, COBOD announced a series of projects in the US to build a variety of buildings, including:
- A Habitat for Humanity 1740sf (160sm) house in Arizona with PERI Group
- Another Habitat for Humanity house in Virginia with Alquist3D
- A second building in Florida with Printed Farms Florida
COBOD also announced they had partnered with STRABAG to 3D print an office building in Austria. COBOD International’s Founder and General Manager Henrik Lund-Nielsen said:
““We are thrilled to see the office project from PERI and STRABAG come to life in Austria. Since our own 3D printing of the first 3D printed building in Copenhagen back in 2017, The BOD which is an office hotel, nobody else has picked up the gloves when it comes to 3D printing of offices. We hope that the office segment of the market with the Austrian project from PERI and STRABAG will begin to adopt the technology on a larger scale. But why stop there? What about warehouses, retail outlets, and other similar applications?”
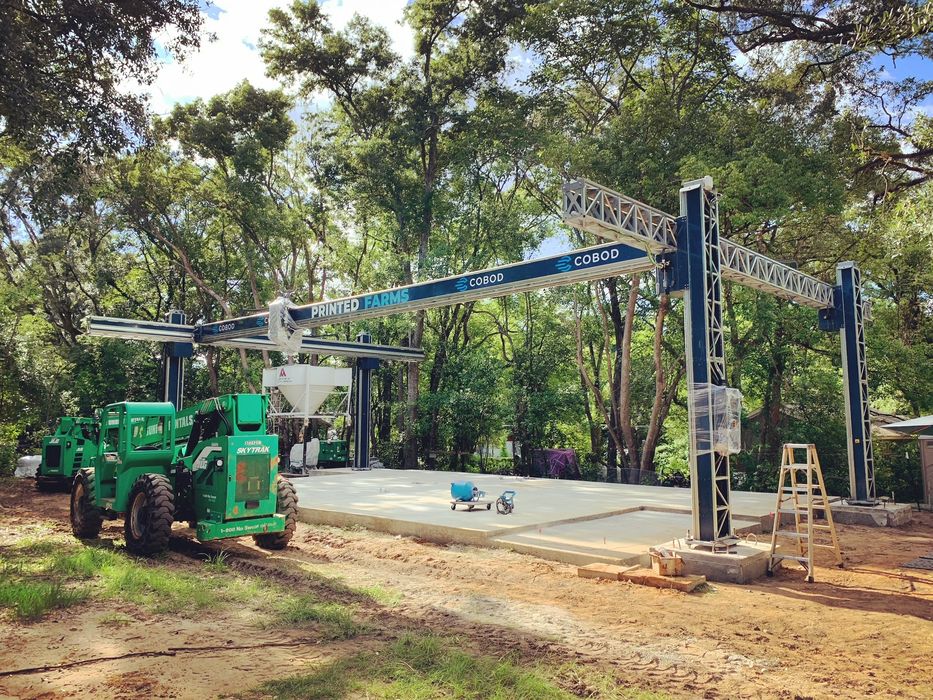
These projects from both companies are certainly tiny when compared to the enormous size of the US construction market, but all big things must start small. It’s likely that as these projects complete and their follow-on projects begin, more people in the construction industry will take notice and potentially begin experimentation.
In the long run it may be that construction 3D printing could prove to be an economical and efficient method of building that’s more commonly used by the industry.
My hope is that more aspects of build projects could be automated, and the vision of a truly 3D printed home could eventually be realized.
But that’s a long way off yet.