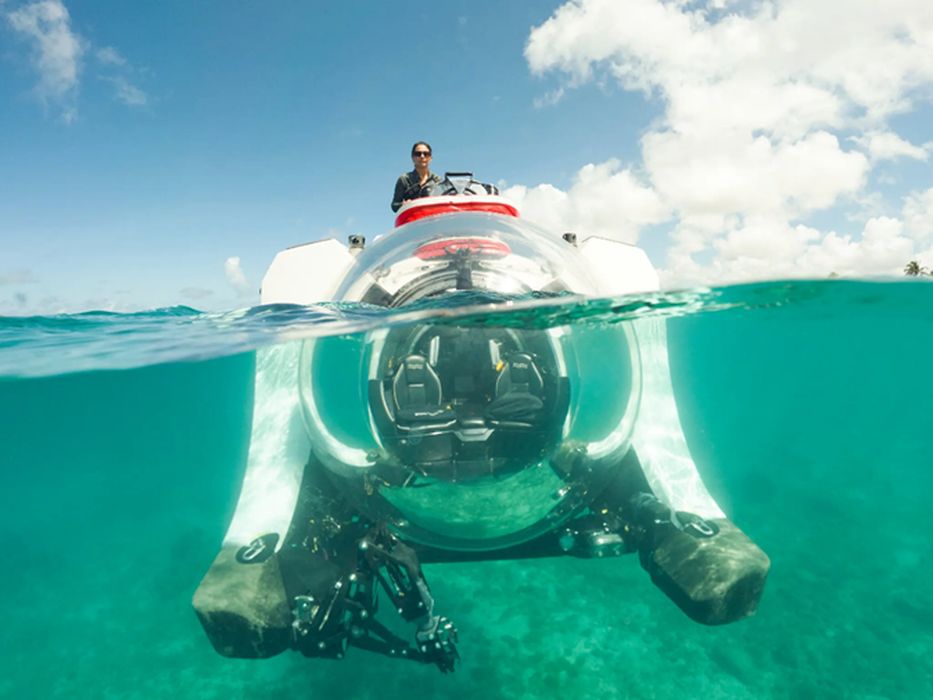
Charles R. Goulding and Preeti Sulibhavi look at the use of 3D printing for manufacturing submersibles.
The race to space has just gone down under. In an emerging exploration trend, adventurous people are now seeking to explore the deep sea in commercial submarines designed for personal travel. There are numerous companies diving into this trend. Many offer submersibles that range in price from US$2-3M.
We have covered military submarines in previous Fabbaloo articles including, Electric Boat submarines, converting the Boeing supply chain to Electric Boat submarines, the US$9.5B Columbia submarine contract, as well as the Australian submarine contract ad 3D printing’s role in all of this.
There is room for 3D printing to be a part of the commercial, personal submarine trend, however. The submersibles, as some are referred to, are often more compact and have more user-friendly features. These qualities fit in well with 3D printing technologies.
In fact, DIVE-LD, a 3D printed sub, was prototyped in 2020. It was supposed to be the prototype for a new generation of autonomous underwater vehicles (AUVs) that would change the accessibility and nature of ocean exploration forever. While things may still be underway, it is hard to ignore the rising demand for under water exploration.
Navies (not only the US, but as we have mentioned other nations) have obviously been seeking 3D printing technologies for some time now because of its durable yet flexible prototyping abilities for new innovative components and replacement parts.
Even luxury vehicle manufacturers such as Aston Martin are banking on this trend. In collaboration with Triton Submarines, Aston Martin is making underwater more luxurious (as depicted above) with its Project Neptune mini sub.
Submarines operate under immense pressure. To keep passengers safe from being crushed, personal subs require stout steel inner hulls to protect against the ocean’s relentless weight. This is referred to as the pressure vessel. AUVs are the underwater version of drones. 3D printing enables AUVs to build around an interior skeleton, as opposed to an expensive airtight piece of construction. This means that the sub can be flooded until the pressure inside equals the pressure outside, and the motors must be protected from the depths. A 3D printed exterior skeleton is added and a 3D printed, mini sub is created.
Thyssenkrupp Marine Systems has 3D printed parts for submarines that received safety and quality approvals for serial production. Thyssenkrupp has been re-engineering old parts using 3D printing because it enables more ideal geometries and is more cost effective. But utilizing 3D printing for serial production of submarine parts is a substantial development.
Fabbaloo has covered 3D printed mini subs in its 3D Printed RC Subnautica piece.
The Research & Development Tax Credit
The now permanent Research and Development (R&D) Tax Credit is available for companies developing new or improved products, processes and/or software.
3D printing can help boost a company’s R&D Tax Credits. Wages for technical employees creating, testing and revising 3D printed prototypes can be included as a percentage of eligible time spent for the R&D Tax Credit. Similarly, when used as a method of improving a process, time spent integrating 3D printing hardware and software counts as an eligible activity. Lastly, when used for modeling and preproduction, the costs of filaments consumed during the development process may also be recovered.
Whether it is used for creating and testing prototypes or for final production, 3D printing is a great indicator that R&D Credit eligible activities are taking place. Companies implementing this technology at any point should consider taking advantage of R&D Tax Credits.
“Sea”-ing is Believing
The human drive for underwater exploration is not new. When Julius Verne penned “Twenty Thousand Leagues Under the Sea,” he probably didn’t expect it to become a reality in the time that it has. What was science fiction is now fact, thanks to advanced technology and 3D printing.