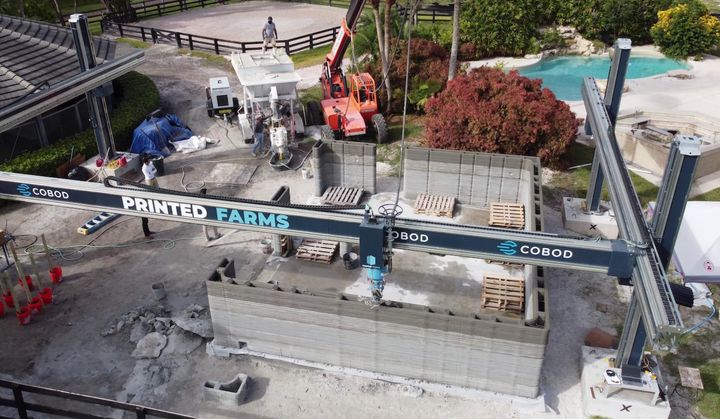
Three announcements foreshadow increased construction 3D printing in the US.
Construction 3D printing is a relatively new field with very few players involved. In fact the field has previously been populated with rather suspicious companies and overly exaggerated technical claims, but that seems to be calmed these days.
Construction 3D Printing Background
Early entrants would mislead mass media with astounding claims of “3D printing a home in 24 hours”, or similar impossible stories. The truth is that most of today’s construction 3D printers are essentially giant RepRap 3D printers that use concrete extrusion instead of polymer filament. They are able to 3D print walls, foundations and some other concrete structures, but can’t do flooring, roofs, windows, HVAC, plumbing, etc. All of that must still be done by conventional trades.
That said, the ability to 3D print the concrete portions does offer several advantages:
- It can be less expensive because there is less labor required (no formworks need to be built)
- It can be faster (again, no need to wait for formworks)
- It can offer the possibility of unusual geometries at no extra cost (because formworks again)
- It can be done consistently (no interruptions by manual labor forces, as is the case in some countries)
But there are challenges. It remains to be seen whether construction 3D printers can lay down proper concrete in colder temperatures. The quality of the concrete has been questioned, as some mixes have reduced the gravel component significantly to ensure proper flow through the system, which could weaken the concrete. Many experimental construction 3D prints cannot obtain occupancy permits from regulators due to these sorts of issues.
Some companies seem to be overcoming these difficulties and have actually obtained permits for their work. Recently, there have been three examples in the US, a country where there seems to have been less construction 3D printing activity than some other regions.
SQ4D Construction 3D Printing
One is SQ4D’s announcement of the “world’s largest permitted 3D printed home”, which is apparently now on the market if you care to buy it (1400sf, US$299,999 in Riverhead NY). Of course, the entire home is NOT 3D printed; just the walls are extruded.
SQ4D claims the cost of construction is “50% cheaper”, but I suspect they refer to the cost of the concrete portion of the project. Roofing, windows, electrical, etc. will all still cost the same as they do in any other project.
Nevertheless, this is an actual (partially) 3D printed home that is for sale. Still for sale, I should point out.
Mighty Buildings 3D Printed Homes
A second announcement from California’s Mighty Buildings indicates they’ve raised a staggering US$40M Series B investment round. That’s a huge pile of cash that should be able to set sail on deploying their technology into more regions.
Their approach is a bit different in that they 3D print standardized home designs in a factory, and then ship them to the building site mostly complete. They also use a Corian-like thermoset composite material, rather than concrete. So far they have completed and installed five projects, with two about to be delivered. They say they have another 20 in the works.
COBOD Enters US
Meanwhile, Denmark-based COBOD is finally making a move into the US. The company has been busily executing projects in Denmark, India, Africa, and Germany, as well as unique wind turbine tower mounts.
Based on their now-extensive experience in construction 3D printing, COBOD is apparently ready to enter the US market. Their first stop appears to be Florida, where they’ve partnered with a new construction startup company, Printed Farms, who have built a storage unit. Their next project will be “two intercoastal villas”.
COBOD’s powerful BOD2 construction 3D printer is a very capable device, able to 3D print three-story concrete buildings.
I think COBOD may have the better strategy here, as they seem to be partnering with local construction companies and supplying their equipment and 3D printing expertise. This enables them to scale globally, as they can leverage their partners’ knowledge of local building codes and practices.
If that’s the case, then I can see COBOD quickly licensing their BOD2 technology to many different local construction companies in the US. This would mean we’d soon see a great many more 3D printed buildings.
That’s great news, but I really want someone to invent a machine to automate the rest of the construction process.
Via CNN, COBOD, Mighty Buildings and SQ4D