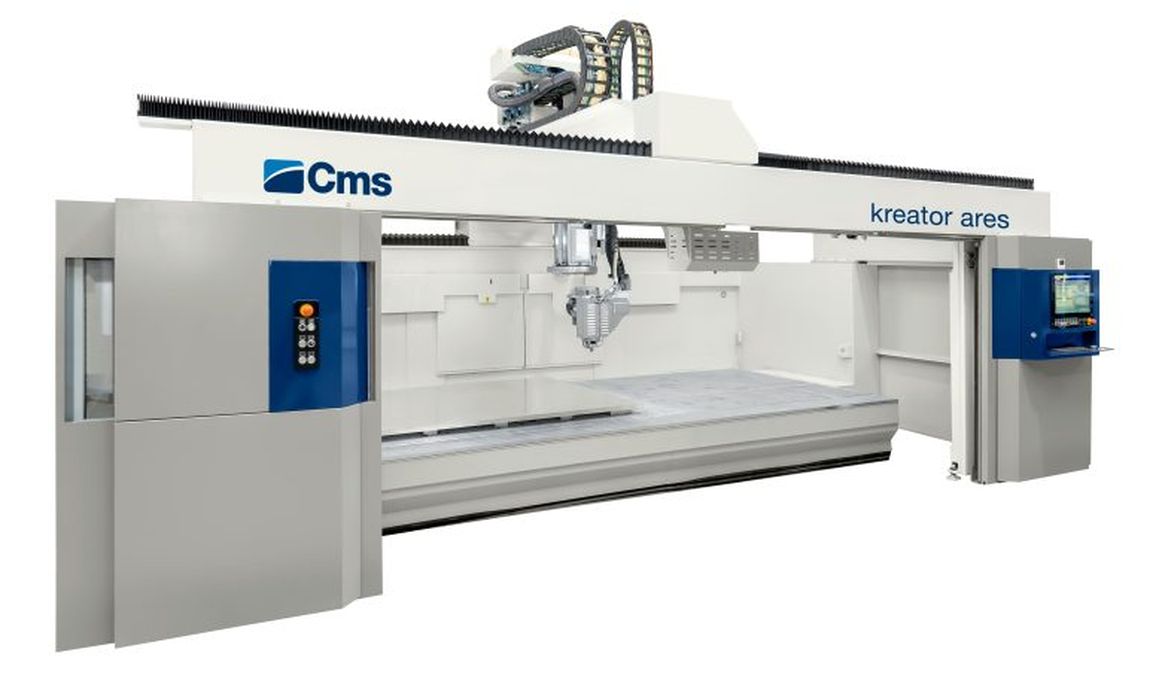
Developed in partnership with Fraunhofer IWU, the CMS Kreator can now deposit up to 100 kg of material per hour.
Industrial machine manufacturer CMS SpA is among a small group of companies leading the charge for large-format additive manufacturing. The company’s most recent hardware release, an update on the CMS Kreator, is at the cutting edge of this segment, combining rapid extrusion capabilities and 5-axis milling to produce large structures with tight tolerances, all while minimizing material waste and accelerating production times. CMS’ latest upgrades to its system, as we’ll see in more detail, include more extruder options and a larger build volume.
What CMS Kreator brings to the table
The powerful hybrid system was developed in cooperation with the Fraunhofer Institute for Machine Tools and Forming Technology (IWU) and is based on the institute’s Screw Extrusion Additive Manufacturing (SEAM) process. This AM method uses thermoplastic granules to reduce material costs and is reportedly up to eight times faster than conventional 3D printing technologies.
The CMS Kreator combines the benefits of SEAM with a highly versatile build capability. That is, the hybrid machine’s print head can print vertically (0°) and horizontally (90°), as well as at a 45° angle. The milling component is then employed to transform the near-net-shape prints into large-scale parts with excellent tolerances.
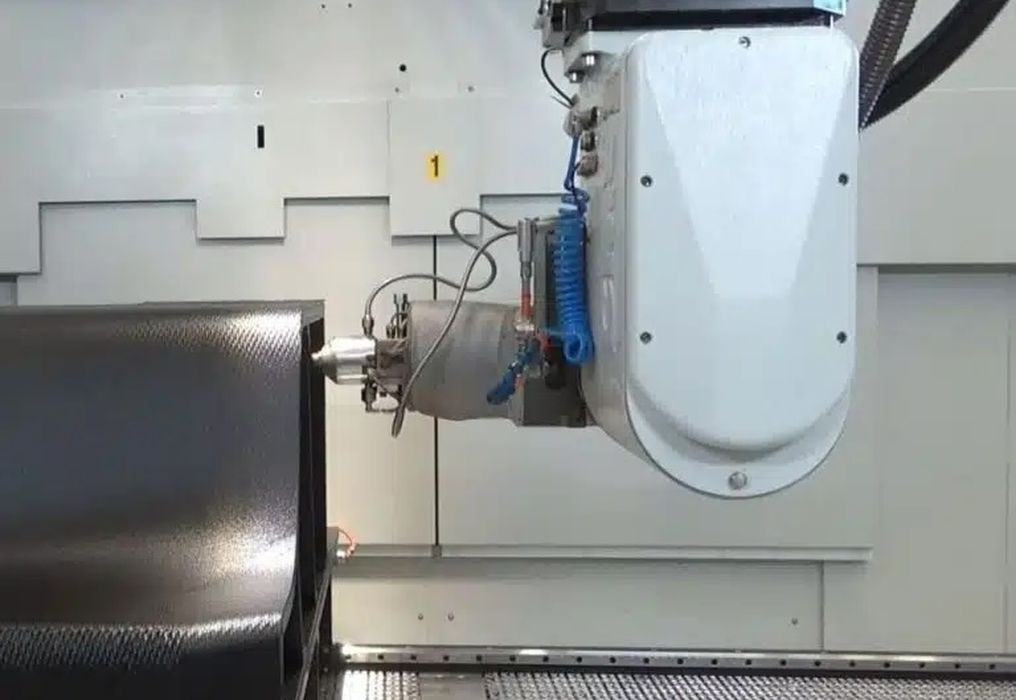
In terms of scale, the machine can be configured to print parts in the range of 3 x 2 x 1 meters to 10 x 8.5 x 2.5 meters, significantly larger than the previous iteration of the CMS Kreator. In the spirit of adaptability, the CMS Kreator can also be fitted with different sizes of extruder, allowing users to choose to print at rates of 10 kg/hour all the way up to 100 kg/hour.
CMS adds that its hybrid LFAM solution can print at speeds of up to 16 m/min, making it faster than competing large-format extrusion systems. This is possible thanks to a new slicing software developed specifically for CMS’ platform. CMS says: “The new slicing software…simplifies the process and temperature control, thereby reducing printing times and improving production workflow.”
The speed of the system and the ability to increase extrusion volume not only boost productivity for end users, they also contribute to the system’s sustainable edge. Because parts can be built up faster, the energy expended per part is minimized. Moreover, CMS says its system can cut material waste by at least 81% compared to current manufacturing technologies.
On the topic of materials, the CMS Kreator can reach extrusion temperatures up to 450°, which opens up many material possibilities. According to the company, the printer can process thermoplastic granules made from PLA, PP, PET, PA, ABS, PC, PEI and PESU, among others. The printer’s pellet feedstocks are also typically reinforced with discontinuous glass or carbon fibers for additional strength. If a specific material is required, CMS can collaborate to test a new material on its platform through the CMS Kreator Additive Lab.