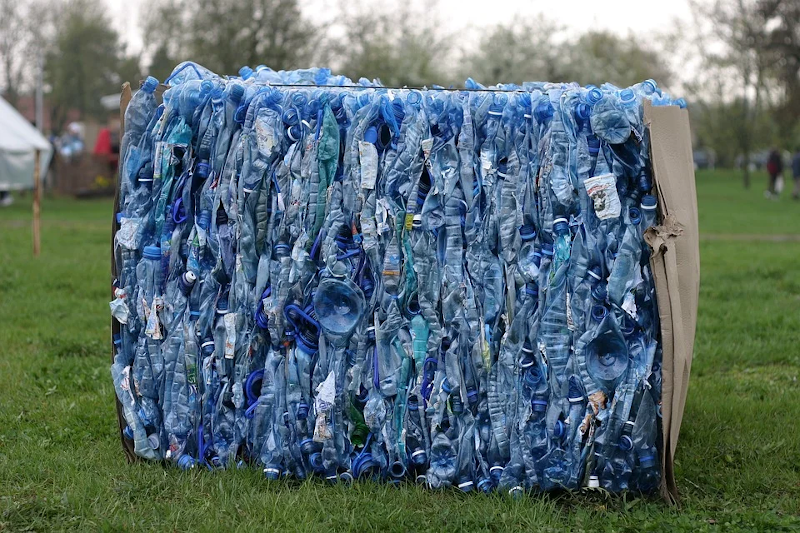
Charles R. Goulding and Joseph Castine examine the role of plastics recycling efforts in impacting 3D printing materials availability and pricing.
In 2021, global plastic production is ever increasing despite heightened concerns from cradle to grave. Each year there is an estimated 8 million metric tons of plastic that enter the planet’s oceans, which is an addition to the estimated 150 million metric tons that are already present. Many believe that the solution to this crisis is increased recycling efforts. Not only is this not a panacea, but traditional recycling methods often result in lower quality plastic grades that make them unsuitable for use with foods and beverages. But what if there was a way to recycle these plastics in a manner that would not cause them to degrade?
INEOS Chemical Recycling Initiatives
This is what INEOS hopes to do with their new plastic recycling process. This process is among several new and innovative chemical recycling processes whereby the plastics are broken down into basic chemicals or oils. These raw materials can then be reformed into new plastics that do not contain the impurities or degraded quality of traditionally recycled plastics.
INEOS, which has teamed up with some partners in the US and Europe, claims that the production of polystyrene by chemical recycling can reduce greenhouse gas emissions by half. Not only would this be an incredible development in the greenhouse gas space, but this large production of polystyrene could be beneficial to 3D printing. Polystyrene, though brittle, has been successfully used in some 3D printing applications with great success.
Other Chemical Companies Backing These Initiatives
Some consumer brands are pledging to reduce their usage of virgin plastics. These developments in chemical recycling coincide with these pledges, and these recycled chemicals could prove crucial in helping reduce the usage of virgin plastics. Companies like Chevron Philips Chemical and BASF are investing in these chemical recycling processes. Chevron Philips Chemical recently began the production on a commercial scale of chemically recycled polyethylene which is the most common plastic resin.
Plastic Energy is another company that has begun to innovate within this space. They are a UK-based startup company that has innovated upon these chemical recycling processes. They have two production facilities located in Spain. These facilities have reactors that are fed with low-quality plastic refuse, the resultant product contains up to three-quarters of reusable hydrocarbon oils, which can be used in place of naphtha in plastic feedstocks.
With companies like BASF throwing their weight behind these chemical recycling practices, it is presumable that these plastics will be used in the latest innovations including 3D printing. In recent years there has been a trend at BSF of committing more and more resources towards 3D printing innovation. BASF has continually made improvements upon 3D printing filaments, introducing new materials, and more structurally sound materials over the years. In the coming years, we could likely see the chemical giant create printing materials with these recycled chemical compounds.
Impact on 3D Printing
With these newly developed chemical recycling practices, there could be an increase in sourcing for 3D printing materials. This could be the result of a large influx of chemically recycled plastics entering the market. The end result could be lower costs of 3D printing materials. Any companies engaging in the development and design of new products using 3D printing should consider taking the R&D Tax Credit.
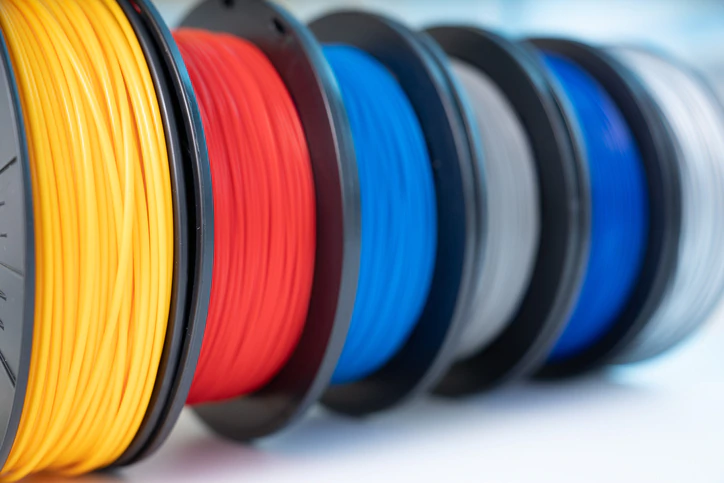
The Research & Development Tax Credit
Enacted in 1981, the now permanent Federal Research and Development Tax Credit allows a credit that typically ranges from 4%-7% of eligible spending for new and improved products and processes. Qualified research must meet the following four criteria:
- Must be technological in nature;
- Must be a component of the taxpayer’s business;
- Must represent R&D in the experimental sense and generally includes all such costs related to the development or improvement of a product or process;
- Must eliminate uncertainty through a process of experimentation that considers one or more alternatives.
Eligible costs include US employee wages, cost of supplies consumed in the R&D process, cost of pre-production testing, US contract research expenses, and certain costs associated with developing a patent.
On December 18, 2015, President Obama signed the PATH Act, making the R&D Tax Credit permanent. Since 2016, the R&D credit has been used to offset Alternative Minimum Tax (AMT) for companies with revenue below $50MM and, startup businesses can obtain up to $250,000 per year in payroll tax cash rebates.
Conclusion
With these new developments in chemical recycling plastics, the future of the plastics industry looks brighter than ever. With these advancements not only will the number of virgin plastics decrease, but it also provides a way to divert plastics from landfills and the planet’s oceans.