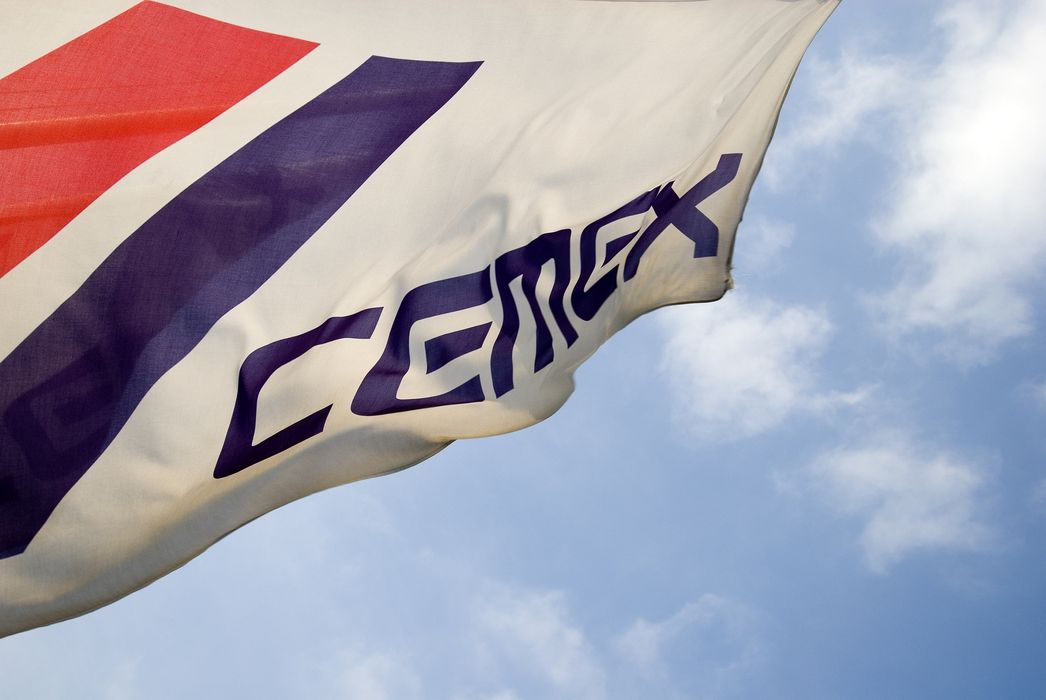
Charles R. Goulding and Andressa Bonafe speak to Ibon Iribar about ongoing developments and applications of construction 3D printing at Cemex.
Curious to know more about the current landscape of construction 3D printing, we had the opportunity to talk to Ibon Iribar, Investment and Open Innovation Advisor at Cemex Ventures. Cemex is a global construction materials company committed to building a better future through sustainable products and solutions. With a revenue of US$15.6 billion, the Mexican multinational offers cement, ready-mix concrete, aggregates, and urbanization solutions in growing markets around the world, powered by a workforce of over 43 thousand employees.
Having worked at Cemex Ventures for nearly 6 years, Ibon deeply explores and analyzes advanced technologies for the construction industry and helps identify investment and business development opportunities with new startups, corporations, and organizations in the construction technology ecosystem across multiple markets. Ibon leads the efforts for the industry’s biggest challenge for construction startups, Cemex Ventures’ Construction Startup Competition. He works year-round searching for the most innovative and promising solutions to invest in or collaborate with, supporting startups’ development and boosting their growth within the built environment.
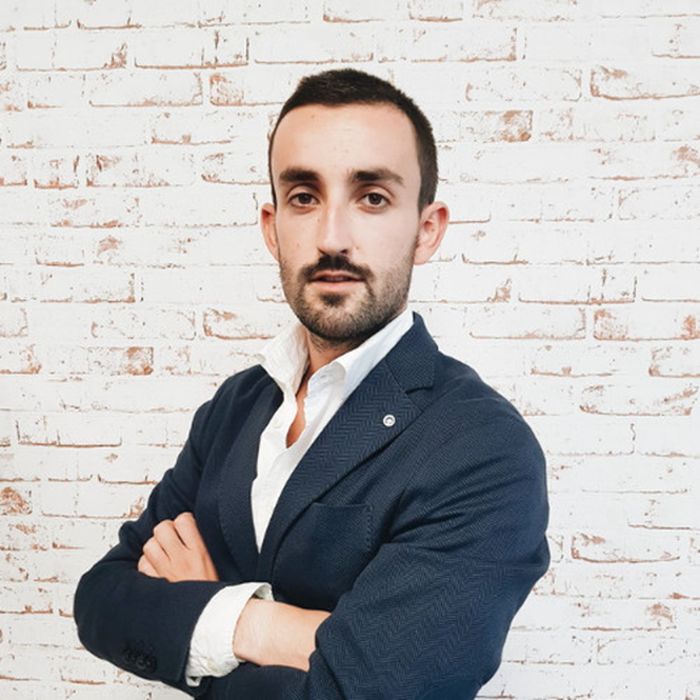
Ibon has been working with 3D construction printing at Cemex Ventures since its early days in 2017. He has been responsible for analyzing everything related to additive manufacturing, understanding all the technological options, how they work, and how different players behave within this ecosystem. This means taking a big-picture view from an entrepreneurial perspective, but also from the perspective of investors, general contractors, and consumers.
He also worked on the analysis and due diligence related to Cemex Ventures’ first collaboration with and investment in 3D printing – in mid-2022, the corporate venture capital and open innovation unit announced an expanded partnership with COBOD, a global leader in construction-grade 3D printers. Thanks to the efforts from Cemex’s corporate venture capital, it’s Global Research & Development department was able to work closely with COBOD on the development of a proprietary admixtures family called D.fab, which allows conventional concrete to be efficiently tailored for 3D printing construction. Besides additive manufacturing, he has worked with material optimization topics, including construction, demolition, and excavation waste management.
Having such a comprehensive perspective on the construction industry, what would you say are the most promising areas for 3D printing and the biggest challenges to the more widespread adoption of this technology?
We see a lot of potential in 3D printing for housing applications, which is not limited to what we understand as pure building, such as the structural elements and walls. We also see the potential for printing prefabricated elements or elements for façades, which can be printed off-site and taken to the job site. Even though there are opportunities in infrastructure elements, urban furniture, etc., we think that the biggest market is in the housing sector.
As far as challenges, I think the biggest and the most urgent one is the adoption and implementation of friendly regulations. For now, we only have the case of the United Arab Emirates that have established a fixed percentage of buildings that should be built using 3D printing by 2030. Another interesting geography from a regulation perspective is the Netherlands, where they have developed not only houses but also some iconic structural prototypes.
We have seen a lot of companies claiming that they have printed the first house, the first one-story building, two-story building, or the first school, etc. However, what we haven’t seen or what hasn’t been communicated yet is that people are already living in these buildings. We haven’t seen the next step after the first claim. I believe that’s because of the lack of strong legislation or regulation in a lot of countries. In the US, for instance, each state has its own building codes and building regulations but, as far as I know, there is not one common or standard building code or even a regulation for 3D-printed buildings.
The second challenge that I will highlight is to change the mindset of the consumer when it comes to adopting the technology or buying a 3D-printed house. As I said before, this sort of construction is still identified as a “cookie cutter” solution and is often not aesthetically pleasing.
Finally, the third challenge pertains to the deficiency of materials and mixes, which need to be more efficient and sustainable. There are a lot of options to explore, including glass waste, and different sorts of fibers from other industries, such as those from tires. We have seen startups that have tested new materials and mixes and, while the performance is good, they don’t make sense economically. We need to make materials more efficient but also economically viable as well.
We know that Cemex has focused on developing materials for 3D printing applications. Could you tell us more about this process?
Our efforts related to materials have been linked to the research and development initiative with COBOD. When we started the analysis and started talking with different players in the ecosystem, we realized that they have considerable challenges coordinating the various aspects of a 3D printing project. They often have multiple, simultaneous responsibilities as not only the owners of equipment, but also the ones in charge of material and mix preparation, and the construction phase. There is a lot happening at the same time, which prevents them from focusing on any particular area.
In the case of COBOD, we saw that their outstanding performance in machine manufacturing could be enhanced by a greater focus on material optimization. They were already one of the few companies actually printing concrete instead of the most commonly used mortar-based mixes. After a few months of cooperation, we launched D.fab in late 2021. COBOD’s first projects using this material were located in Angola and Oman. We’ve recently started working on projects in other Cemex geographies, such as the US and the UK, and we would like to expand that footprint even further.
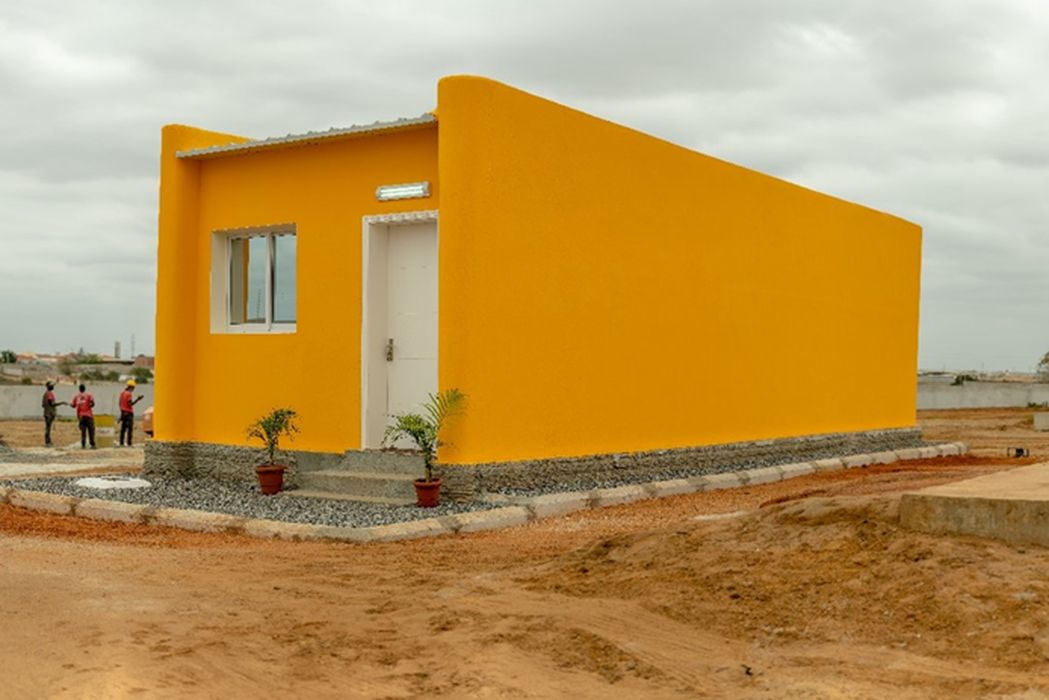
Overall, we think that even if 3D printing does not replace traditional construction, many benefits can still be reaped. For this reason, we wanted to position Cemex as a reliable and promising partner for 3D printing projects and that’s why we decided to develop D.fab.
Cemex has an impressive strategy to face the challenges of affordable housing in Mexico. Could you tell us how 3D printing plays into that?
We are committed to tackling the housing crisis and promoting affordable housing, especially in one of the most challenging regions to do that, which is Latin America. When it comes to 3D printing, however, the truth is that a person who is going to buy a house is often not willing to buy a 3D-printed house because this technology is identified as somewhat unaesthetic or as a rapid response to natural disasters, accidents, etc. Now we’re starting to see some projects that are implementing 3D printing combined with other traditional techniques, which is something promising in the housing market.
What about sustainability? How does 3D printing relate to Cemex’s commitment to sustainable practices?
Our progress is largely driven by our sustainability goals, especially our efforts to decrease the carbon footprint of all the scope one emissions, which are the ones that we are emitting when manufacturing our own materials and products. So in that sense, we have developed a lot of project partnerships and investments in the decarbonization space, especially for carbon capture, utilization, storage, alternative fuels, and hydrogen-related solutions.
Another branch, under the umbrella of sustainability, is circularity and waste management. We are analyzing options to introduce waste source components in the mixes for 3D printing, which would be a potential next step. Cemex already has a family of products and projects based on waste components called Regenera. We see that certain markets have been more friendly towards this type of material.
When it comes to scope two and three emissions 3D printing can help reduce both the use of machinery that consume fossil fuels and the efforts needed to move materials from the factory to the job site. This could have a great benefit from a footprint perspective in the short and long run.
Conclusion
Our conversation with Ibon gave us an interesting view of how one of the largest players in the global construction industry has been involved with 3D printing. His unique expertise and big-picture perspective helped shed light on opportunities and challenges for the more widespread adoption of additive manufacturing in construction.