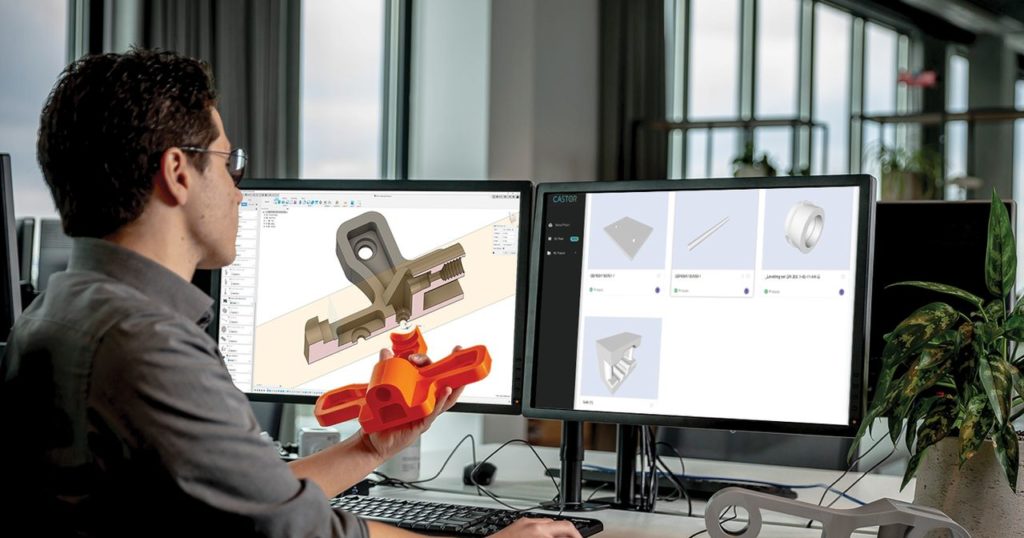
CASTOR and Ultimaker announced an agreement to integrate CASTOR’S screening software into Ultimaker Cura.
CASTOR is an Israel-based software company dedicated to additive manufacturing applications. Specifically they produce a tool that can automatically inventory CAD libraries to determine the suitability of each part for 3D printing.
Their system would examine geometries to, for example, identify if the part has walls that are too thin to be properly produced by a target 3D printer. They also investigate part size and in particular the ability to generate removable support structures.
But their system doesn’t end there. They also can generate a financial analysis to determine if each part can justify production using additive techniques — on a given machine with a specified material.
For older companies with vast libraries of part designs, CASTOR’s toolkit can be a lifesaver.
Imagine a company with thousands, perhaps hundreds of thousands of parts, most of which still must be made available to customers as spares when required. The traditional approach is to make them all in advance and store them until needed, which could be years or even decades later. That’s expensive.
Even worse, the production of those parts is typically done only once when the manufacturing line was set up for production. It just runs a bit longer to make an inventory of spares for all eternity, and then is shut down forever. In other words, spare parts typically have a limit.
In those cases companies are often forced to declare a part or system “unsupported” because they’ve run out of parts.
But what if these parts could be 3D printed on demand? Then you’d only need to keep the CAD model on hand to be able to generate as many parts as required, and sometimes even in the location they are required. This approach is called “Digital Inventory”, and is increasingly popular due to its flexibility and efficiency.
Back to that company with thousands of parts. Faced with a conversion to a digital inventory, they would normally have to hire a small army of CAD specialists to manually examine each part design and make a decision on its additive future. That is incredibly expensive and time-consuming, and is the reason many companies have not yet taken the step into digital inventory.
Enter CASTOR, which is able to do this automatically. Well, it’s not perfect, but it can quickly qualify many parts, leaving only a few requiring manual inspection. It’s a powerful concept that likely will be used by most manufacturers in the long-term.
Ultimaker’s Digital Factory is their online platform for additive production. The cloud-based tool allows management of all Ultimaker equipment regardless of location, and dispatching of jobs via print queues. It’s a way for a company to have a single central point of management for all their (Ultimaker) 3D printing activities.
The new integration will permit direct export of parts identified by CASTOR into the Digital Factory. This integration will clip out quite a few manual steps involved in moving models into a spot where they can be readily 3D printed.
You might not think this is a big saving, but consider the typical use of this sequence in a digital inventory scenario. Moving the parts manually would take, say, five minutes each. Now imagine you have to do this 48,000 times for all the parts identified for the new digital inventory. I think you can see how powerful this integration could be.
For CASTOR, this integration makes their product much more active and critical, as it becomes part of a larger automated workflow for digital inventories.
For Ultimaker this is also a sweet deal, as it is likely to flood the Digital Factory with plenty of new inventory to print. You know what that means: more printers and material will be required.
Via Ultimaker