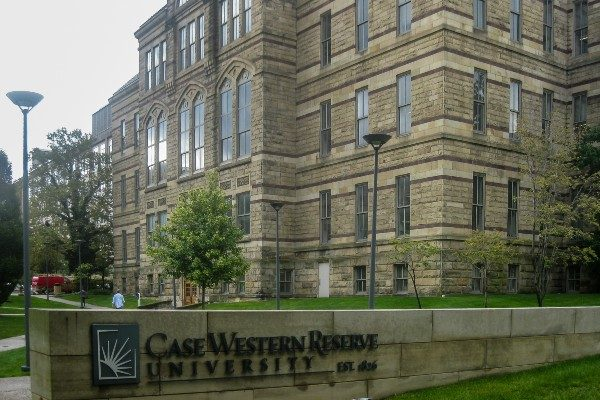
Charles R. Goulding and Joseph Castine consider a leading research university’s work in advancing 3D printing materials.
Case Western Reserve University (CWRU) is a research university located in Cleveland, OH. It was created in 1967 when two of the area’s premier institutes, Western Reserve University and Case Institute of Technology, merged to create Case Western Reserve University. The university’s most popular major is Biomedical Engineering, which ranks 16th among United States undergraduate biomedical engineering programs, with the overall undergraduate engineering rank being 42nd. This prestigious university has a diversity of research interests – and some of their professors have a special interest in helping further the already booming 3D printing industry.
While the first 3D printer was invented way back in 1983, recently the industry has experienced massive growth. The current market size of the industry in 2020 was $16 billion, and the projected market share by 2024 is nearly $41 billion reflected by its expected compounded annual growth rate of 26.4%. Within the 3D printing industry, advancements are made every day and CWRU has some professors that are at the forefront of structural improvements for 3D printing through the application of biology in printing materials.
3D Printing Elastic Foam Advancements
Foam Reprocessing Cycle [Source: ACS]
Within their 3D printing interests, CWRU professors do extensive research on printable elastic foams. Through their research studies on these foam materials, the professors have found that through direct ink writing (DIW) of these foams there are extensive tunable properties of the foams. By dispersion of sodium chloride among the silicone precursors, it was determined that the 3D rubber exhibits ultra elasticity, with near-zero stress under 90% compression or 1000 compression cycles.
Through their research CWRU was also able to determine that by using nanoclay, carbon black, and polymers in an organic solvent, the resulting 3D foam has good compressibility and elasticity while also being able to conduct electricity. Also proving useful as a gas sensing device as exposure to volatile organics causes the foam to swell.
Structural Improvements in 3D Printing
With respect to the structural integrity of the 3D printing materials themselves, CWRU research professors have conducted diverse research on different methods of strengthening the printing material itself. Within the realm of structural toughening research has been conducted on the use of surfactant-complex Chitosan in which the results of tensile modulus, tensile strength, yield stress, and strain-at-failure improvements of 45%, 40%, 32%, and 68% higher respectively than neat Polymethacrylate.
Advancements in 3D Printing Composites
The use of composites in 3D printing has widespread application in enhancing certain desirable qualities of the plastics being used. Selective laser sintering (SLS) is a process by which a laser is used to heat powders to the extent that they can be combined into a solid or porous mass. Through the use of SLS with polyamide-12 and carbon black powders, research has been conducted to determine the resulting material’s properties. The research has found that by SLS with up to 3% carbon black powder with polyamide-12 the printing material has increased thermal stability causing higher degradation temperatures. Further research into 3D printing composites has been conducted to determine the optimal parameters of polymer composite usage in order to foster a better cost to performance ratio for these composite plastics.
Companies that engage in 3D printing processes that include research into material structure and composite profiles may be eligible for the R&D tax credit.
The Research & Development Tax Credit
Whether it’s used for creating and testing prototypes or for final production, 3D printing is a great indicator that R&D Credit eligible activities are taking place. Companies implementing this technology at any point should consider taking advantage of R&D Tax Credits.
Enacted in 1981, the now permanent Federal Research and Development (R&D) Tax Credit allows a credit that typically ranges from 4%-7% of eligible spending for new and improved products and processes. Qualified research must meet the following four criteria:
- Must be technological in nature
- Must be a component of the taxpayer’s business
- Must represent R&D in the experimental sense and generally includes all such costs related to the development or improvement of a product or process
- Must eliminate uncertainty through a process of experimentation that considers one or more alternatives
Eligible costs include US employee wages, cost of supplies consumed in the R&D process, cost of pre-production testing, US contract research expenses, and certain costs associated with developing a patent.
On December 18, 2015, President Obama signed the PATH Act, making the R&D Tax Credit permanent. Beginning in 2016, the R&D credit can be used to offset Alternative Minimum tax for companies with revenue below $50MM and, startup businesses can obtain up to $250,000 per year in payroll tax cash rebates.
Conclusion
CWRU is fostering a research environment where its professors are encouraged to research emerging and rapidly expanding technologies, including 3D printing. The research that these professors are conducting is on the cutting edge of 3D printing advancements. Their research may prove crucial in propelling 3D printing towards mainstream production applications by advancing material stability, structure, and cost.