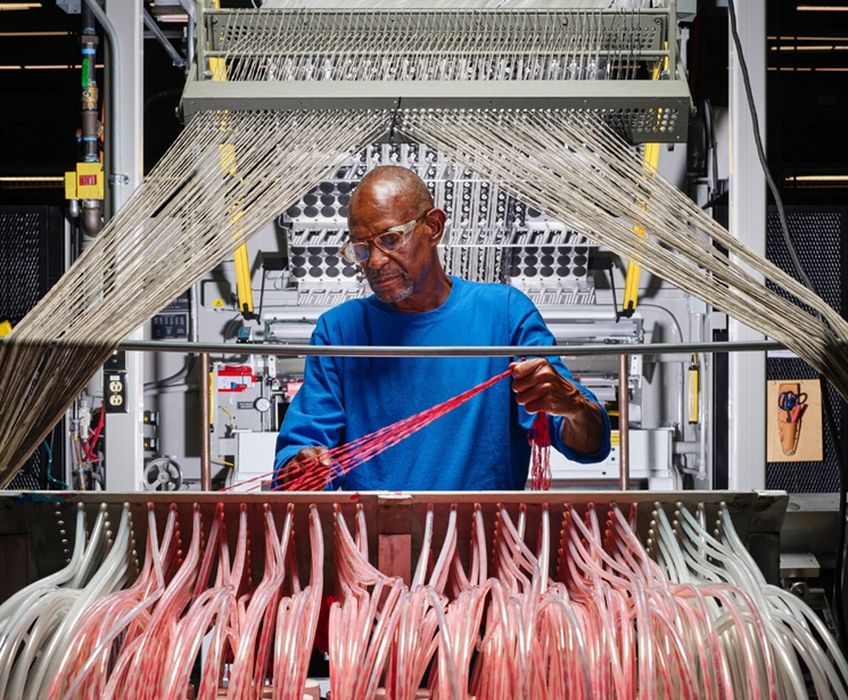
Charles R. Goulding and Joseph Castine examine how additive manufacturing might assist with carbon capture technologies.
CarbonTech is a wide variety of products that can be made from CO and CO2 emissions captured from power plants, biomass or direct air capture.
These products have been rising in prevalence over the past few years as the efforts to reduce carbon emissions have increased.
One of the leading manufacturers of CarbonTech products includes global flooring manufacturer Interface, Inc. It’s more than likely you have interacted with an Interface product if you have ever found yourself in an airport terminal, corporate hallway, or CVS Pharmacy. One of their main products is commercial carpeting, which contributes an immense amount of carbon to the environment through its production. For example ,in the mid-1990s Interface calculated that a square meter of carpeting was responsible for releasing about 20kg of CO2, whereas that same carpet now accounts for only for ~300 grams per square meter with Interface’s new developments. This means that the carpet utilizes more CO2 gas than the fabrication process produces, a remarkable development. The new carpet is comprised of recycled vinyl material, processed biomatter, infused with latex created from smokestack exhaust, and finally topped with salvaged nylon.
Noah Deich, a founder at nonprofit think tank Carbon180, aims to rethink carbon. He sees the market for CarbonTech products reaching an immense US$6T globally. The global cement industry is a global producer of 2.6 billion metric tons (2,204M lbs.) or about 7% of all global carbon emissions. Within this industry there are several startup companies aiming to develop low-carbon cement and are attracting some lofty investors including Bill Gates’ Breakthrough Energy, Amazon’s Climate Pledge Fund and venture capitalist John Doerr of Kleiner Perkins.
Some of the other companies entering into this field include large cement companies like Holcim (which has been 3D printing homes in Africa) and HeidelbergCement.
Within the cement industry, approximately 70% of the carbon emissions are a result of the cement-making process, and the remaining 30% comes from the energy to heat the kilns. Over the past few decades, as energy has become more efficient, carbon emissions have been reduced by approximately 20% via more energy-efficient kiln processes.
Ian Riley, CEO of the World Cement Association, believes another 30% of the emissions can be reduced through traditional means like more efficient processes, but that still leaves 70% which needs to be remediated.
CarbonCure, a Canadian company, has come up with a solution for some of these carbon emissions in the cement industry. They have developed a process wherein CO2 from factory emissions is captured and injected into the concrete mixture, effectively mineralizing the CO2, while also decreasing emissions by a further 5-8%.
Other industries are also starting to invest more money into CarbonTech products to reduce carbon emissions including some companies in the fuel industry. One of these companies, LanzaTech, has for over a decade been working on genetically engineering bacteria that can digest carbon gases and produce fuels like ethanol.
Carbon capture is also a prevalent methodology of carbon emissions reduction in industrial applications. This process is used to capture the carbon emissions which are produced from coal-fired power plants to either reuse or store those CO2 emissions.
In 2020, Oak Ridge National Laboratory developed a circular device that proved crucial in the cooling of absorption columns. The process of absorbing CO2 is not perfectly efficient and often produces excessive amounts of heat throughout the process. This process would use a complex aluminum component that integrated the functionality of both carbon capture and heat exchange which the team realized could be produced via additive manufacturing. This component utilizes several small channels to enhance the carbon capture within these columns, increasing the efficiency of the absorption columns. ORNL says that the device can capture up to 20% of CO2 in optimum conditions whereas, in the typical situation carbon capture will be around 15%.
These new concrete production processes could prove to be very useful in the concrete additive manufacturing sphere. Companies like SIKA have begun to develop low waste concrete additive manufacturing processes, coupled with the low waste products addition of low carbon production processes could help propel this concrete manufacturing into the mainstream. Other companies have also utilized these concrete additive manufacturing techniques to build communities, including ICON who has utilized this technology to produce 3D printed communities in Tabasco, Mexico using local materials to produce their concrete mixture. Integrating this low waste concrete with low carbon concrete processes could prove vital in the future of our planet.
Companies engaging in 3D printing and other additive manufacturing research techniques may be eligible for the R&D Tax Credit.
The Research & Development Tax Credit
The now permanent Research and Development (R&D) Tax Credit is available for companies developing new or improved products, processes and/or software.
3D printing can help boost a company’s R&D Tax Credits. Wages for technical employees creating, testing and revising 3D printed prototypes can be included as a percentage of eligible time spent for the R&D Tax Credit. Similarly, when used as a method of improving a process, time spent integrating 3D printing hardware and software counts as an eligible activity. Lastly, when used for modeling and preproduction, the costs of filaments consumed during the development process may also be recovered.
Whether it is used for creating and testing prototypes or for final production, 3D printing is a great indicator that R&D Credit eligible activities are taking place. Companies implementing this technology at any point should consider taking advantage of R&D Tax Credits.