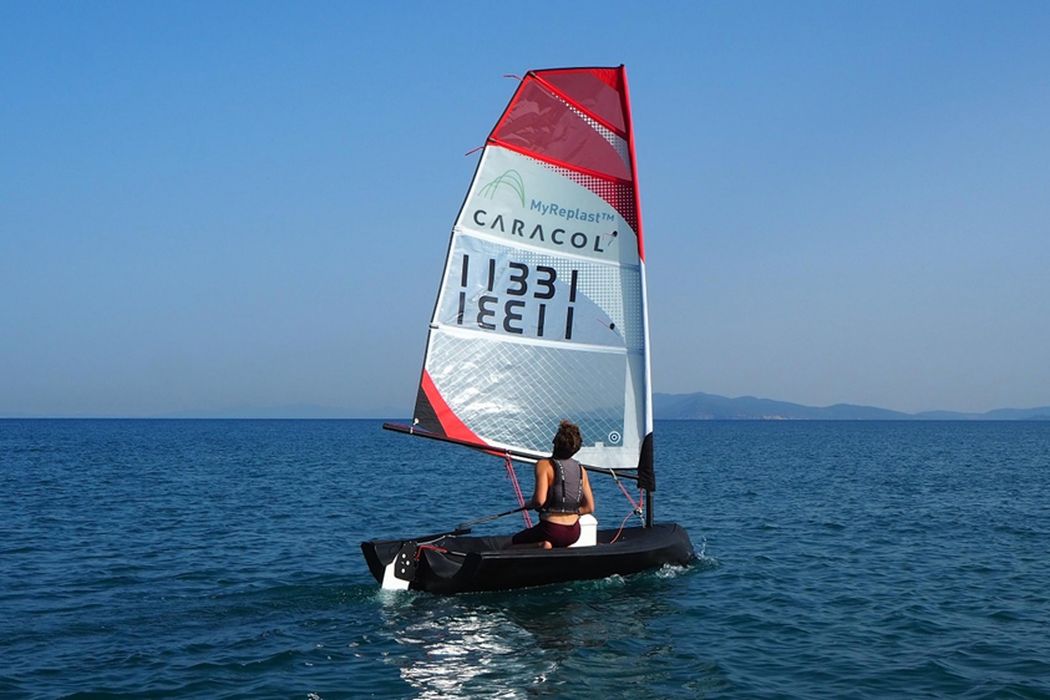
Charles R. Goulding and Fraser Lintott discuss how 3D printing can disrupt the sailboat industry.
The First 3D Printed Sailboat
Italy-based additive manufacturing company Caracol and sustainable chemical lab, NextChem also based in Italy, have partnered up to create the first 3D printed sailboat.
The small, single sail “Beluga” is printed entirely using an upcycled plastic polymer called MyReplast. Due to the size and intricacy of the massive single piece part, Caracol uses a 6-axis robotic arm 3D printer. This long and twisting printer, aptly named “Heron AM”, produces a final product that uses less material than traditional manufacturing methods, costs less, takes less time, and is better overall for the environment.
Sailing has traditionally been a sport available to few due to location and cost. The most basic of sailboats can cost over US$1,000. Because of cost savings with sustainable materials and additive manufacturing, “Beluga” points towards not only a more sustainable future for sailing but a more accessible one as well.
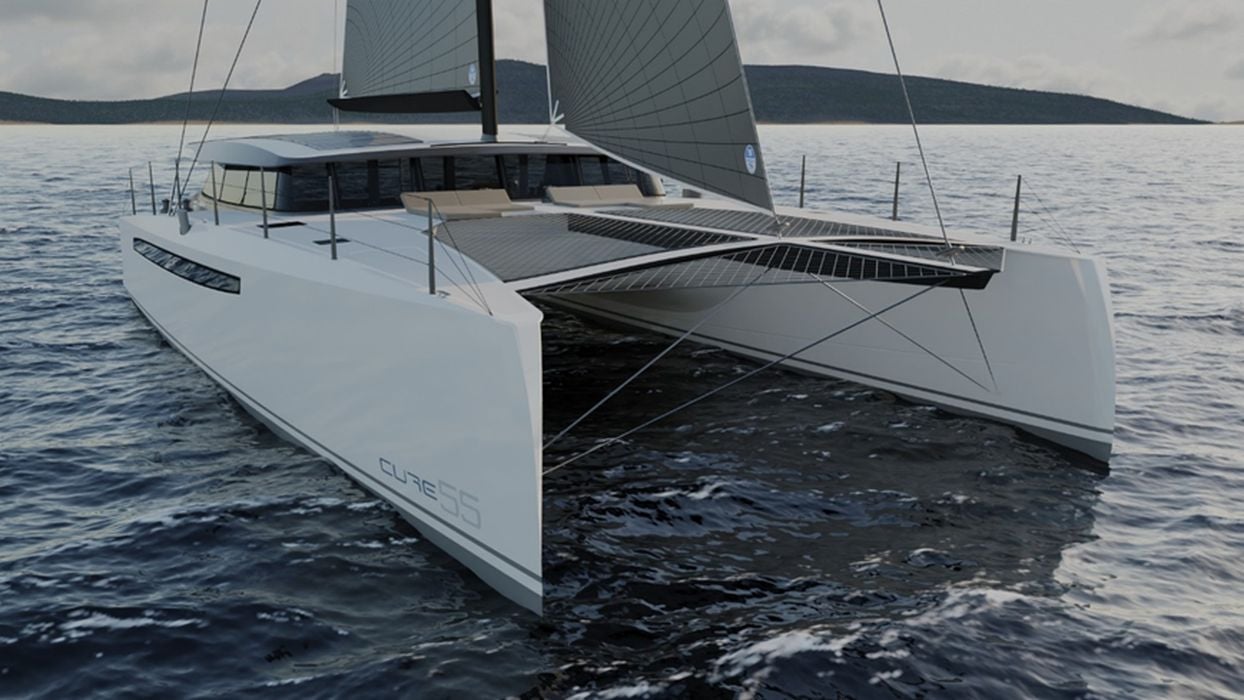
Now Make It Bigger
It is hard to believe but the yacht pictured above is also manufactured with 3D printing. Cure Marine on the Sunshine Coast of Australia has the biggest 3D printer in the southern hemisphere. The dimensions of the behemoth printer are 80 feet long by 25 feet wide and 10 feet high. The massive scale of the printer allows them to 3D print their entire boat hull in one piece. The printer also has a machining head and a sanding and polishing head that allow it to clean up the print once it is finished.
The final hull itself is not what is 3D printed. The final catamaran is made of fiberglass or carbon fiber, but in order to use these materials, you need to make a “plug” which is used to create molds. These plugs are 3D printed and there are huge advantages to this. Prototyping by hand can take a large amount of technical labor. 3D printing allows for iterative design changes until you create the desired product.
Another advantage of 3D printing is the precision. Cure Marine’s tolerance for error on their boats is less than half a millimeter. That is an extremely tight tolerance which is difficult to achieve by hand. A 3D printed plug makes for a perfect mold. These plugs can also be recycled after they are used to make a mold.
Cure Marine is driving the yacht manufacturing industry into the future. Their methods reduce lead times and prices, making them a formidable competitor in the market.
The Research & Development Tax Credit
The now permanent Research and Development (R&D) Tax Credit is available for companies developing new or improved products, processes and/or software.
3D printing can help boost a company’s R&D Tax Credits. Wages for technical employees creating, testing and revising 3D printed prototypes can be included as a percentage of eligible time spent for the R&D Tax Credit. Similarly, when used as a method of improving a process, time spent integrating 3D printing hardware and software counts as an eligible activity. Lastly, when used for modeling and preproduction, the costs of filaments consumed during the development process may also be recovered.
Whether it is used for creating and testing prototypes or for final production, 3D printing is a great indicator that R&D Credit eligible activities are taking place. Companies implementing this technology at any point should consider taking advantage of R&D Tax Credits.
Conclusion
3D printing continues to influence every industry globally. In sailing, not only does it reduce costs and lead-time for manufacturers, but it also provides a sustainable and accessible alternative to traditional boat building.