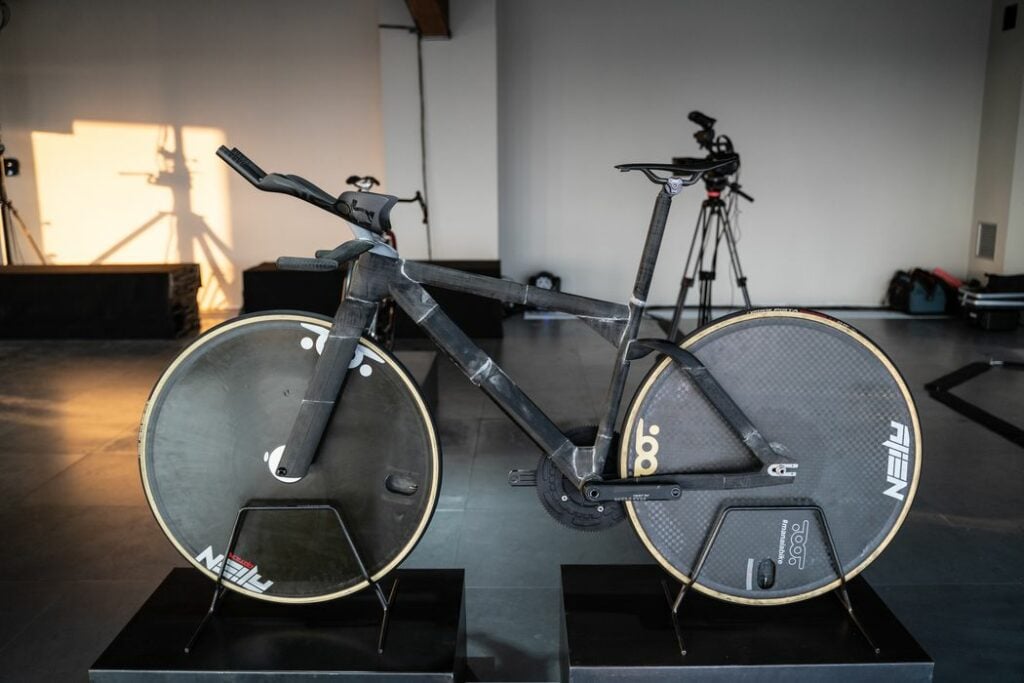
SPONSORED CONTENT
Is it possible to 3D print a high performance bike with an inexpensive 3D printer? It turns out you can — but indirectly.
Bicycles take a lot of mechanical stress, and they must always be made from very strong materials like metals or carbon fiber. Thus, you would not expect to be able to 3D print them with a desktop 3D printer that is not able to access those materials.
But you CAN use a desktop 3D printer to develop prototypes for the bike parts that can later be transformed into final production parts.
That’s been happening in industry for years: 3D printers have been used to make part prototypes. The reason for this approach is that no special tooling is required to make the prototype part: you just print it, without delay.
The issue is that in the course of part development, you must print many iterations of the part to tune the design. Each iteration might increase safety, performance or decrease weight, and dozens may be attempted before the “perfect” part design is achieved.
Normally this is done with the use of professional-level 3D printers that are somewhat expensive. These machines can reliably print parts with accurate dimensions, which is critical for prototypes undergoing testing.
This has been the practice of Italian bike manufacturer TºRED Bikes, which has been producing high-end products since 2013. They’ve been using 3D printing for projects, and have a mission to increase its use going forward.
Recently the company has been deep into a new project they call “Falcon”. It’s an exploration of new custom bike design and also new ways to manufacture bikes, with a relationship to the upcoming Paris Olympics occurring in 2024.
For the Falcon project, the TºRED team decided to use the Anycubic Kobra Max, a larger format desktop unit that’s available at far lower cost. This is quite a departure for prototyping that normally occurs on much higher cost professional 3D printers.
TºRED techs found they could easily produce useful prototypes on the Kobra Max — sometimes as many as five per print job.
In these images you can see how they broke down the parts into printable segments, and then assembled them together into the full bike design.
This enabled TºRED to quickly develop new bike designs. The parts could be fit tested, and the entire bike could be tested in a wind tunnel to measure performance gains, which are mission-critical for a high performance bike manufacturer. Note that the parts have been smoothed after printing for this purpose.
According to Anycubic, most of the bike parts were made in common PLA, except for the seat and a portion of the handlebar, which were made in a carbon-fiber composite material (3DXTech’s PLA-CF).
The rapid workflow allowed TºRED to quickly develop an optimal design, which could then be taken for 3D printing in metals for production.
TºRED’s designer Romolo Stanco said:
“What fascinates me about this 3D printed bike is that it has been the way to see, test, and try many different solutions. For some parts that need a larger printer to be printed, the Kobra Max has been the perfect choice to quickly create the particulars in our labs. After development and tests in our laboratory and in the wind tunnel, we could print out the final parts in metal additive manufacturing (Scalmalloy or Titanium). For us, it is essential to use rapid tools, the automatic printed calibration system. for example, it allows you to be immediately operational and have precision in executing even substantial pieces.”
What does all this mean? Simply that it’s possible for high-end prototyping to occur on devices like the Anycubic Kobra Max, and that’s a machine that’s affordable by every design shop.
Via Anycubic