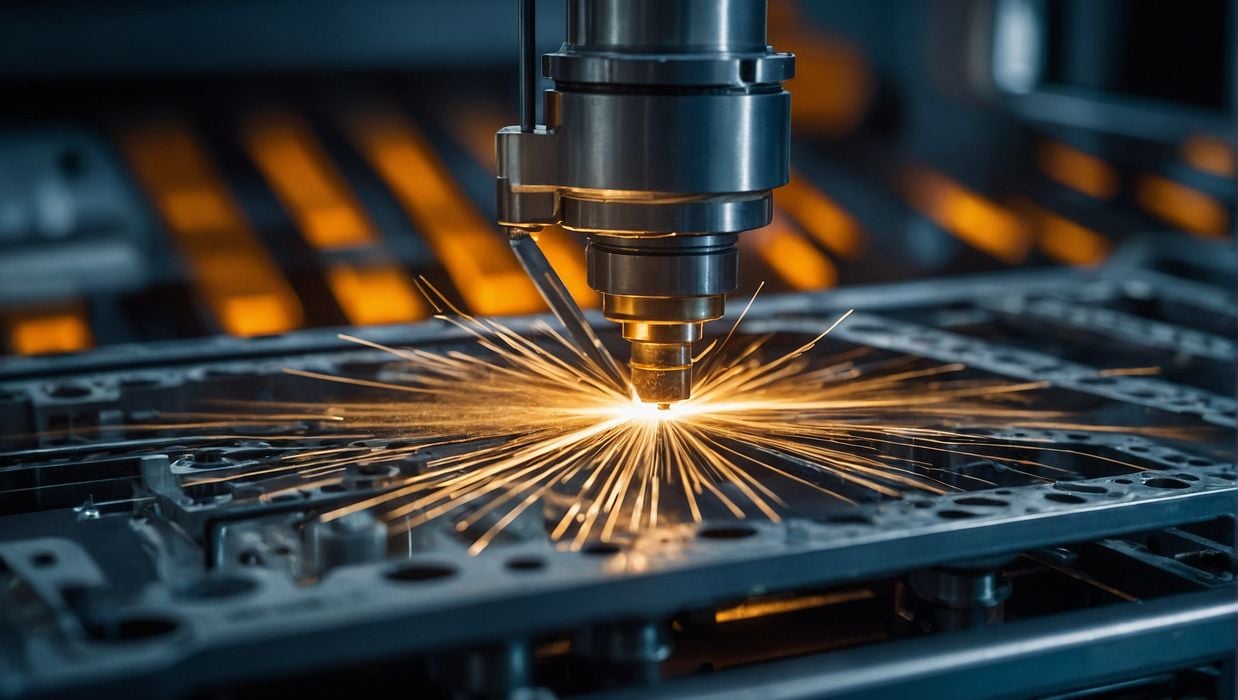
These four benefits of 3D printing should appeal to any engineer struggling with supply chain woes.
The COVID-19 pandemic made weaknesses in the supply chain painfully apparent but that wasn’t enough to solve them. Over the past few years, lead times on overseas tooling have ballooned from weeks to months or even years. Meanwhile, much of what used to be U.S. manufacturing’s sturdy and productive infrastructure has been shipped off to lower-cost countries or driven out of business.
At this point, the arguments for reshoring U.S. manufacturing go beyond the mere economic to the strategic as well. Almost a third of renewable energy comes from hydropower but much of that critical infrastructure is sorely in need of repair. To make matters worse, many of the shops that used to produce replacement parts no longer exist.
“We’ve seen over the past four years that the global supply chain is not as resilient as we thought,” says Fabian Alefeld, senior manager for academy and consulting at EOS North America and host of the Additive Snack podcast. “We built these complex supply chains starting in the ’70s and ’80s, and that push into globalization went well for a pretty long time. COVID obviously showed us the first disruption but we’ve seen more disruptions in the past two years due to natural disasters, wars and local conflicts, like the blockade in the Red Sea.”
Fortunately, additive manufacturing (AM) offers a ray of hope for reestablishing a robust and secure supply chain rooted in domestic manufacturing.
How additive manufacturing can help the supply chain
“I don’t think additive manufacturing is a magic bullet that will solve all our problems,” says Alefeld, “but it’s certainly one piece of the puzzle of building a more resilient supply chain.” He outlines four benefits of AM that should appeal to manufacturers struggling with supply-chain challenges:
- Rapid prototyping: “Obviously, this is where 3D printing got started. But if we want to bring manufacturing back, we also have to bring design and innovation back, and we know additive can help companies iterate.”
- Accelerating production: “We see this especially in the space industry, where they’re prototyping thrust chambers using additive and then that same technology gets used for production. That’s cutting lead times for production as well as innovation.”
- Increased flexibility: “If it’s difficult to build up a conventional supply chain or I don’t fully know the demand for my product, I can use AM until I hit a certain threshold and then switch over to machining, casting, whatever technology works best. Then, in my long tail, I can flip back to AM for aftermarket products or spare parts.”
- Cost efficiency for small or specialized jobs: “The last category is just complete direct printing of parts that may have lower volumes or are quite complex, where additive manufacturing is the only production technology you can use.”
Each of these reasons to adopt AM is compelling on its own but AM truly shines in applications where these benefits overlap.
Additive manufacturing applications in the supply chain
One good example of how AM can overcome supply-chain problems, says Alefeld, involved Daimler Buses. In 2017, the company’s spare-parts portfolio was reaching unsustainable numbers: “They had 300,000 spare parts they needed to have in stock, not only because it’s required by law in certain countries, but because it was a unique selling point of their products.”
EOS and Daimler worked together to establish a a directory of part files enabling the bus maker to print, finish and ship parts on demand. “It’s not even difficult to identify the best parts for additive,” Alefeld explains. “You look at typical demand over the past few years, compare that to your current inventory and the minimum order quantities your suppliers require you to buy. That last one is the reason you could end up with literally hundreds of years’ worth of stock in your warehouse.”
AM can also tackle supply-chain issues more directly by through increased adoption in the shipping and logistics industries. Take cargo crane manufacturing, another industry that largely moved to China but holds obvious strategic value for the U.S.
“Like the buses, there are components for cranes that need to be produced, but not in huge volumes,” says Alefeld. “Based on the tooling lead times, we think there’s an interesting case to be made not only for 3D printing interior cabin components, but also for die-casting tools and even direct printing.”
Read the rest of this story at ENGINEERING.com