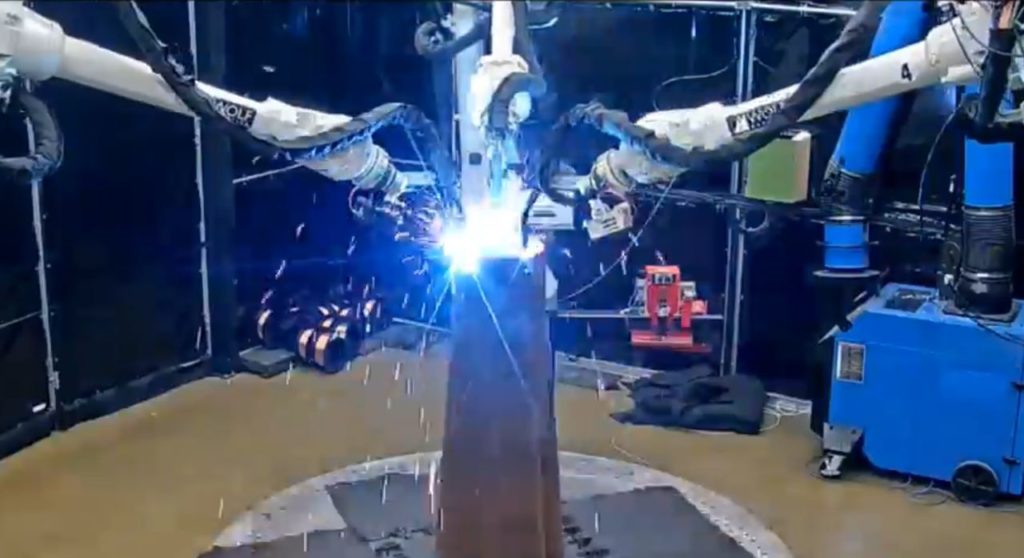
Researchers at the Oak Ridge National Laboratory seem to have developed a way to optimize printing with multiple toolheads.
This is something I’ve thought about for a long while. Today’s 3D print job duration are excessively long, with processing so slow that multiple application areas are unable to use the technology.
If only there were a way to speed up 3D printing.
Speeding Up 3D Printing
Many companies have attempted to speed up operations by increasing the capabilities of their existing designs. Perhaps this is done through the use of more advanced and robust components, faster controller boards, and similar moves.
Other companies attempt to speed up 3D printing by doing operations in parallel. 3D printers with independent dual extruders (IDEX) are often able to print two objects simultaneously in “copy mode”.
Some advanced LPBF systems speed up operations by using multiple lasers. However, these tend to be “zoned”, where each laser is assigned an area to operate within.
There’s one common element among all these approaches: only one item (or zone) is being built at a time. That’s a serious limitation on build speed. It’s like building a skyscraper, but only one worker can be on a floor at a time.
3D Print With Multiple Toolheads
The obvious solution would be to create a system in which multiple toolheads simultaneously work on a single object.
This really hasn’t been done because it’s far too complicated: how do you keep each of the toolheads from crashing into each other? What’s the optimal sequence of building to take place, and how is it split across different tools?
Now we may have a breakthrough in this area.
Dr. Andrzej Nycz is the Wire-Arc Metal AM Technical Lead in the Manufacturing Demonstration Facility at the Oak Ridge National Laboratory. In a recent LinkedIn post, Nycz posted this incredible video:
In the video you can see three independent WAAM toolheads simultaneously working on a metal 3D print. They’re not working on separate parts, but on the same part. This is a unique capability.
Somehow the ORNL researchers were able to develop a system to collaborate between the toolheads to avoid conflicts and produce the object at high speed. How fast is this system? Nycz said on LinkedIn that they can produce 50lbs per hour (23kg, or 545kg per day).
And that’s not all. Nycz said:
“We designed it in such a way that it works for ’n’ robots. It just happens to have three arms but really there is no strict limit.”
This means the concept is entirely scalable, and one could then imagine a squad of robotics very rapidly producing huge objects in a way that’s never been seen previously. In fact, Nycz said that the intended purpose of the system is to produce huge metal objects.
The comments in the video are quite intriguing. Evidently the toolpaths are assigned “dynamically”, which suggests they’re being adjusted based on sensors that examine the work progress according to a machine learning algorithm.
This is likely a critical part of the process, as metal 3D printing’s quality depends significantly on thermal management. Should the temperatures be messed up, portions of the print may have compromised internal crystallization and thus weaken the print. The ORNL system apparently handles this complexity, which is clearly a major breakthrough.
I’m very interested to see where this technology goes in the future. Aside from the increased number of robots, it may also be possible to move robots during the print operation. This would open up the concept of building extremely large objects with a swarm of mobile toolheads that would leapfrog each other. However, the thermal management on such a configuration would certainly be even more complex.
Finally, I have to say they’ve selected the perfect name for this system: “MedUSA”.