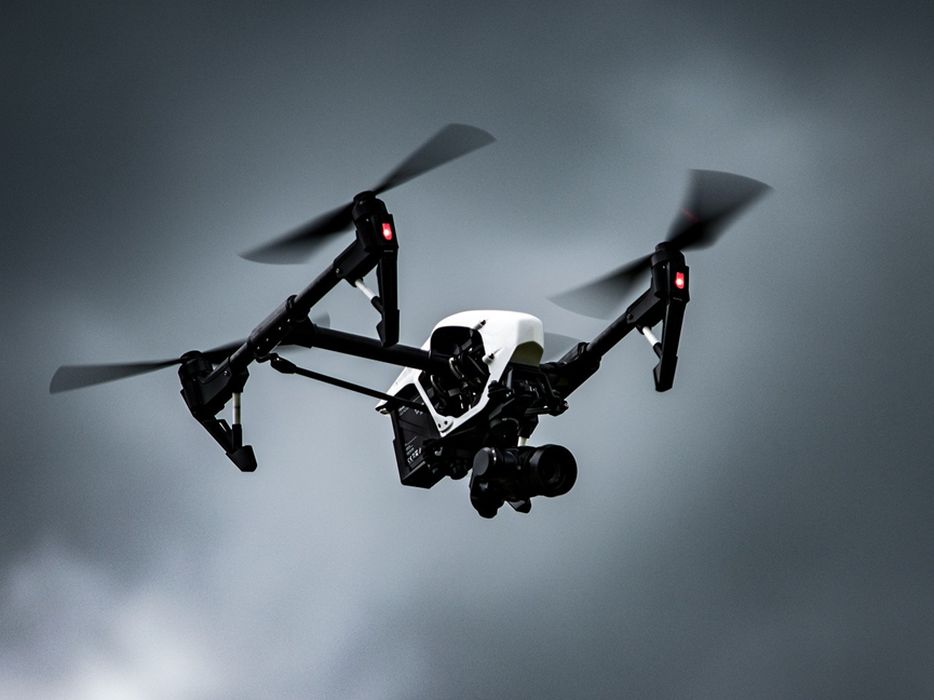
Charles R. Goulding and Preeti Sulibhavi discuss a Russian bakery’s transformative shift as it utilizes 3D printing technology to transition from baking to producing military drones.
The Tambov Bread Factory in central Russia has gotten a lot of attention because it converted from being a bakery to producing drones for the military, emphasizing that the key technology that enabled the transition was 3D printing. Allen Maggard, a Russian defense industry analyst at C4AFDS, a U.S. think tank, said “The combination of low acquisition cost 3D printers and the assurance of state subsidies might make transitioning to drone production an irresistible prospect for companies.” In fact, over 100 companies in Russia have transitioned to producing products for the Russian military’s Ukraine campaign.
Many companies in Ukraine are also using 3D printers to produce drones for the military, like Skyeton which uses large-scale 3D printers to produce fixed wing surveillance drones. Turkey’s companies like Baykar are also leveraging 3D printing to support drone manufacturing for Russia.
The Covid pandemic taught the world that 3D printers are a core technology to fight new enemies. Wars can usher in new technologies and set Vietnam on its way to becoming the modern-day manufacturing powerhouse it now is. Manufacturing guns with interchangeable parts created precision machining and metal fabrication industries in the U.S.
The U.S. has drained its stockpile of core conventional weapons to near zero levels with recent press articles emphasizing shortages for missiles, howitzers and tanks, all of which can benefit from current 3D printing design and production capabilities. Kongsberg, the Norwegian defense contractor that makes the NASAMS surface-to-air missile system enjoying a 100% success rate in Ukraine, currently takes 2 years to produce and involves over 1,500 suppliers. The company is looking for alternative, rapid production methods like 3D printing. It is also opening a new facility with the goal of improving production efficiency tenfold.
According to Kongsberg Maritime:
“The biggest advantage of 3D printing is its ability to create shapes that cannot be machined using traditional methods. For example, the fuselage of a drone is made up of a strong but light internal support structure that is far beyond anything we can achieve in composites today. Fantastic mechanics, moving parts, and electronics inside closed structures. For the engineer, 3D printing is a unique opportunity for new shapes, functions and innovation.”
3D printing technologies can serve as an alternative component supplier, and Kongsberg’s new plant should have the opportunity to integrate 3D printing for design and production. The technology allows for quicker prototyping, customization in design, and distributed manufacturing where components can be printed on-demand around the world.
“Design and production are very closely linked. 3D printing allows us to design products that up to now we have not been able to manufacture. As the technology gradually becomes more mature, the opportunities will begin to become more apparent. Then we will start to see ideas for products and components with properties that are completely different to those we are used to today,” said Alf Petterson, Technical Manager at Kongsberg Aerostructures.
It was recently announced that BAE Systems would restart production of the M777 Howitzer at the request of the U.S. Army. It is unusual to revive a terminated product line. The first restarted unit is expected to be completed in 2025. BAE has been increasing its 3DP capability which should be helpful for the revived Howitzer product line, to speed up traditionally slower artillery manufacturing.
Velo3D’s Sapphire XC 1MZ platform has been used to print the muzzle brake for a US Army howitzer that only took 11 days to print compared to waiting months or years.
Hopefully, the postwar civilian environment will benefit from all this 3D printing expertise. Using drones for drug delivery, forest fire identification and monitoring environmental conditions is much more desirable than hurting people and destroying buildings. Companies with defense experience like AeroVironment are well-positioned to transfer knowledge as they already produce small drones for both military and civilian use.
The Research & Development Tax Credit
The now permanent Research and Development (R&D) Tax Credit is available for companies developing new or improved products, processes and/or software.
3D printing can help boost a company’s R&D Tax Credits. Wages for technical employees creating, testing and revising 3D printed prototypes can be included as a percentage of eligible time spent for the R&D Tax Credit. Similarly, when used as a method of improving a process, time spent integrating 3D printing hardware and software counts as an eligible activity. Lastly, when used for modeling and preproduction, the costs of filaments consumed during the development process may also be recovered.
Whether it is used for creating and testing prototypes or for final production, 3D printing is a great indicator that R&D Credit eligible activities are taking place. Companies implementing this technology at any point should consider taking advantage of R&D Tax Credits.
Conclusion
Wartime spurs innovation, but the ultimate goals of rapid sustainable manufacturing, custom designed-products and distributed production around the world can be more impactful when applied to peaceful industries that raise the standard of living for more people. If the expertise gained from using 3D printing to quickly arm militaries can transfer to environmentally conscious mass customization of everyday goods, the next generation of manufacturing could emerge from the ashes of war rather than be fueled by it.