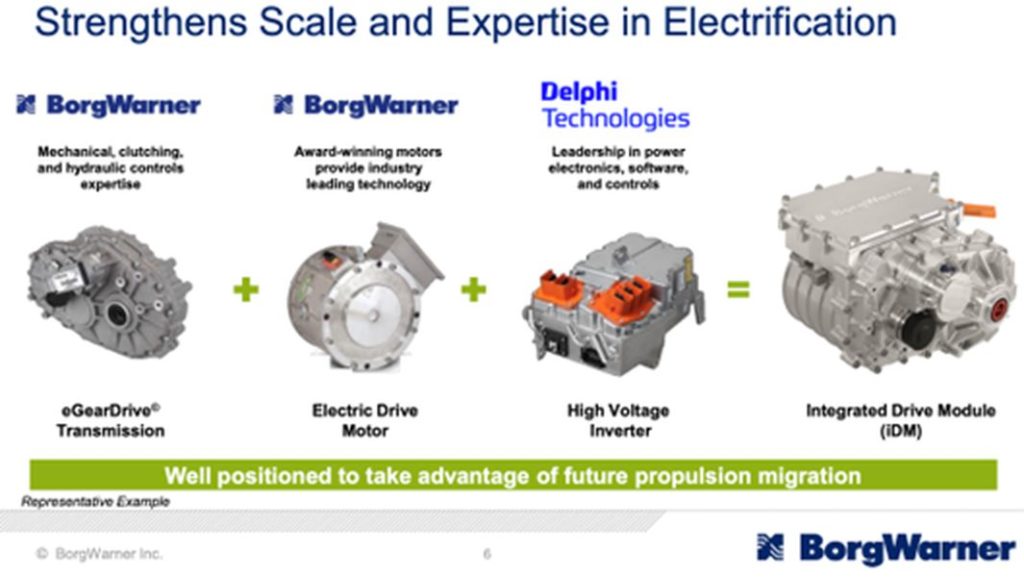
Charles Goulding and Andressa Bonafe look at the use of 3D printing by BorgWarner.
With $10.2 billion in revenue, American multinational automotive supplier BorgWarner employs nearly 50 thousand people in 24 countries worldwide. Continuously aiming to enhance its portfolio of industry-leading propulsion products and systems across combustion, hybrid, and electric vehicles, BorgWarner has completed important acquisitions over the past year.
In 2020, the Company acquired Delphi Technology, a provider of combustion systems, electrification products, and software and controls. The $3.3 billion takeover is expected to strengthen BorgWarner’s electronics and power electronics products, capabilities and scale, creating a leader in electrified propulsion systems.
According to the Green Car Congress, the combined company is expected to be one of the leading pure-play propulsion companies globally, serving light and commercial vehicle manufacturers and the aftermarket. It will also offer a unique, more comprehensive portfolio of industry-leading propulsion products and systems, resulting in greater content per vehicle.
More recently, BorgWarner further expanded its commercial vehicle electrification capabilities with the acquisition of AKASOL. The German designer and manufacturer of high-performance battery systems has developed a proprietary, cell-agnostic technology that provides low-cost, flexible solutions for a variety of applications, including buses, commercial vehicles, rail vehicles, industrial vehicles, ships and boats. This move echoes the efforts of other major automotive players, who are reimagining the future of cars and investing heavily in electric alternatives.
Additive manufacturing has been an important component of innovation for the automotive industry and BorgWarner in particular. The Company recently announced the expansion of 3D-printed prototypes in its Brazilian facility, as an effort to streamline processes and optimize production lines. 3D printing will enable a more efficient evaluation of products at each stage, which in turn allows for timely adjustments to meet the assembly and/or design needs.
In the words of Vitor Maiellaro, Emissions, Thermal and Turbo Systems Plant Manager in Brazil, “Ensuring the utmost quality, safety and efficiency of our products and processes is always at the core of what we do and using 3D printing for prototypes gives us another tool to ensure we are precise and efficient throughout the product development and manufacturing life cycle.”
In other BorgWarner facilities throughout the globe, 3D printing has enabled greater cost efficiency for short batch runs, including low volume items and parts that are no longer available. In 2020, the Company further advanced the use of additive manufacturing by sponsoring the 54th annual Louis Schwitzer Award, which was presented to eight engineers for the development of an Aeroscreen for INDYCAR. The innovative solution is designed to protect drivers from airborne debris and includes a 3D-printed titanium top frame, along with a titanium-reinforced carbon fiber lower frame and a clear laminated polycarbonate screen.
In the United States, 3D printing of automotive parts and similar activities can be supported by R&D tax credits, which are briefly described below.
The Research & Development Tax Credit
Enacted in 1981, the now permanent Federal Research and Development (R&D) Tax Credit allows a credit that typically ranges from 4%-7% of eligible spending for new and improved products and processes. Qualified research must meet the following four criteria:
- Must be technological in nature
- Must be a component of the taxpayer’s business
- Must represent R&D in the experimental sense and generally includes all such costs related to the development or improvement of a product or process
- Must eliminate uncertainty through a process of experimentation that considers one or more alternatives
Eligible costs include US employee wages, cost of supplies consumed in the R&D process, cost of pre-production testing, US contract research expenses, and certain costs associated with developing a patent.
On December 18, 2015, President Obama signed the PATH Act, making the R&D Tax Credit permanent. Beginning in 2016, the R&D credit can be used to offset Alternative Minimum tax for companies with revenue below $50MM and, startup businesses can obtain up to $250,000 per year in payroll tax cash rebates.
Conclusion
BorgWarner has intensified innovation through acquisitions and the use of 3D printing. Investments in flexible technology for electric vehicles and high-efficiency additive manufacturing are paving the way towards the future of the automotive industry. R&D tax credits are available to support these activities and accelerate the pace of innovation.