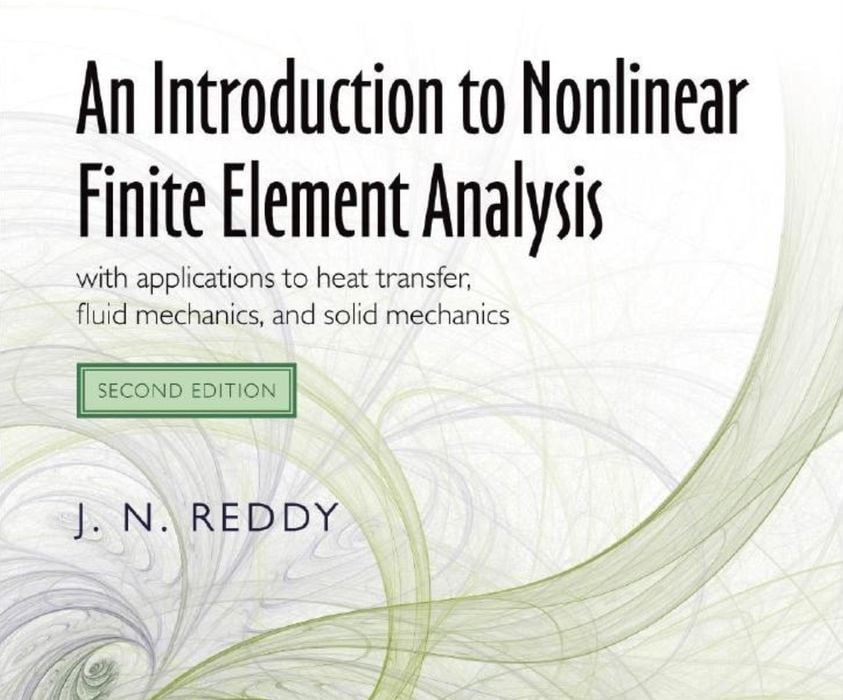
This week’s selection is “An Introduction to Nonlinear Finite Element Analysis” by J. N. Reddy.
Finite Element Analysis, or “FEA”, is a science that should gain considerable interest to the 3D print community. It’s the study of how forces and other factors affect a part of given design, and is increasingly seen as a feature of modern CAD tools.
The problem is simple: if a part is designed, will it survive the conditions of use if made? In years past this was a paper exercise, where engineers used advanced analysis techniques to arrive at rudimentary conclusions.
Today, however, that’s all changed as software makers have developed insanely powerful FEA systems that can revolutionize the design of parts.
The game for part design is often to use as little material as possible. This makes the part not only lightweight, but also less expensive as less material is consumed.
3D printing these parts is highly desirable, because the technology is easily able to handle the complex geometries of an optimized, or “lightweighted” part.
However, there’s a question: what exactly is the optimal geometry for a part? It’s easy to make a part strong: just bulk up the parts. However, it’s far more difficult to “remove” material to lessen the weight while maintaining part strength.
That’s where FEA comes in. It is effectively a simulation of various forces on a part that show where zones of maximum stress will likely appear, using a combination of mathematics and the physical laws involved in a scenario. Designers simply input the expected range of forces and directions, and a computational engine will work out what could happen in real life.
This results in a kind of iterative design process, where designs are tweaked repeatedly in order to optimize the stress results. Can we shave a bit more off this segment? Yes — or no, will be the answer from the FEA system.
Some highly advanced CAD systems will actually use FEA to drive the design itself. In these systems, the required touchpoints and forces are identified, and then the tool generates a design to meet those conditions.
Either way, FEA is a very powerful tool for part designers.
This book provides a detailed overview of FEA and how it works. It begins with an exploration of the mathematical models involved, as well as simulation.
Reviewed are vectors and tensors, functional analysis concepts, and more. The physical mechanisms are explored, including motion, deformation, strain, stress, and the mathematical theories used in FEA. Put together, it’s called the Finite Element Method.
Examples of FEM appear, including bending of beams, two-dimensional problems, elastic plates & shells, solid modeling, and much more.
If you’re looking for an introduction to FEA and theory behind it, this is an easier-to-read book on the subject.
We’re an Amazon Associate and earn a small fee from qualifying purchases. Help support our 3D print news service by checking out this book!
Via Amazon