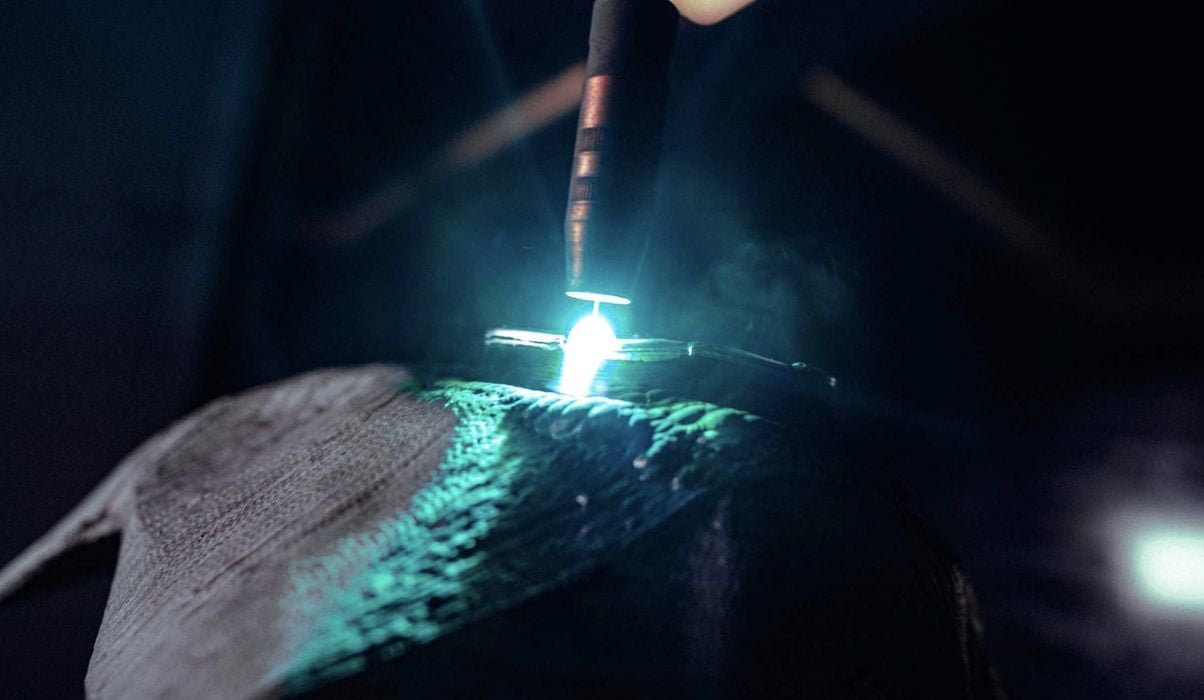
First vehicle trials of WAAM parts expected to begin next year.
Wire arc additive manufacturing (WAAM) offers many benefits over other forms of 3D printing, most significantly speed, with deposition rates 15-20 times that of powder bed fusion (PBF). The process is also exempt from issues with demouldability and, in the right circumstances, find the optimum ratio between weight and rigidity for hollow structures.
All of this means that WAAM is of great interest to the automotive industry, and perhaps no more so than at BMW. The company is currently bench testing WAAM at its Additive Manufacturing Campus in Oberschleißheim, Germany. BMW has been researching WAAM since 2015, establishing a cell for producing test components in 2021.
One example of a test part is a suspension strut, which is normally made with aluminium pressure die-casting. “In this early stage it is already clear that the WAAM process can result in lower emissions in the production process,” said Jens Ertel, head of BMW Additive Manufacturing, in a press release. “The lower weight of the components, their advantageous material usage ratio, and the option to use renewable energy means that the components can be produced more efficiently.”
Wider welding seams in the WAAM process result in rippled surfaces and hence require finishing in critical areas. However, BMW’s engineers also found that WAAM parts can tolerate high loads, including cyclical loads, without any post-processing surface treatment. Of course, this depends on optimized process parameters, which require careful coordination between the welding process and the robotic path planning.
BMW’s solution to the added complexities that come with using WAAM is another emerging technology: generative design. Interdisciplinary teams come up with specific design requirements which are then fed to evolutionary algorithms that output new component designs.
Read the rest of this story at ENGINEERING.com