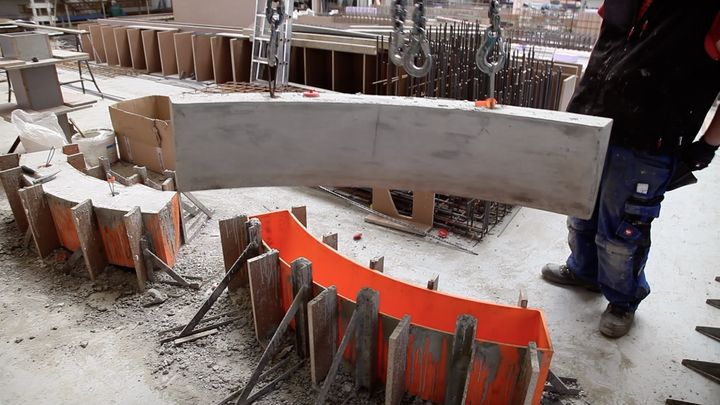
BigRep announced a step into an unusal field for the company: construction 3D printing.
Berlin-based BigRep is already well-known for their ability to 3D print large objects, but construction projects are an order of magnitude larger. That is the science of 3D printing concrete in functional shapes for building projects, typically foundations, floors and walls.
Construction 3D Printing
The field of construction 3D printers today is dominated by a series of machines that are effectively concrete extruders mounted on either giant RepRap-style gantries or robotic arms.
Is BigRep developing a concrete 3D printer as well?
It turns out they are not, and they’re taking a slightly different approach to construction 3D printing. Rather than 3D printing the concrete, they are instead focusing on the formworks.
Concrete Formworks
If you’re not familiar with concrete construction terminology, a formwork is essentially an in-situ mold where concrete can be cast into a desired shape. Typically formworks are made with sheets of plywood that temporarily hold the concrete in place until it sets.
For a foundation this is usually a straightforward exercise: build a rectangular mold for the foundation’s straight walls.
However, when you get into a design that requires curves, then things get a lot more complex. The concrete workers will have to painstakingly construct curved molds, and as everyone knows, curves cost money.
There’s a hybrid approach in which the molds are 3D printed, and then concrete is poured into them when placed in position. This allows the concrete work to be done rapidly, but also gain the ability to create relatively complex molds at the same time. Of course, the molds must be designed so that they can be removed from the concrete easily, so designs must take into account draft angles and overhangs.
This “formwork” approach is not new; I first encountered it being used in 2016 in the Philippines by a 3D print entrepreneur that mysteriously disappeared. That project allowed construction companies to avoid using unreliable human labor by substituting automation to construct the formworks.
BigRep Formworks
Now BigRep is taking the same approach. Since their existing equipment is certainly large enough to consider 3D printing construction formworks segments, it should be a straightforward application. However, it turns out to be not quite so simple.
While it has been possible to 3D print formworks in this way for a while with BigRep equipment, the company has partnered with BASF’s Foward AM unit to create a specialized 3D printer filament just for this application: “CONCRETE FORMWORK”.
BigRep describes the new material’s properties:
“BigRep Concrete Formwork is an engineering-grade filament that is made for high quality formwork with a smooth surface and high geometrical accuracy. With exceptional dimensional stability and low moisture absorption, it’s the perfect match for printing complex geometries for casting. With its stiffness and heat resistance above 100 °C, Concrete Formwork is ideal for functional, performance applications.”
This is another example of a highly specialized material for a specific application. BigRep will certainly recommend using it on formworks projects, and as these prints are typically large — up to 1m in length — they will sell plenty of the huge 8kg spools.
Formwork 3D Printing
What could be done with this technology?
One thing to emphasize here is that we cannot expect 3D printed formworks to replace traditional formworks for commonly shaped structures, as it would be too expensive to do so. Expect to see plywood formworks used for flat structures into the foreseeable future.
The best use of 3D printed formworks will be for curvy structures, and in particular pieces that will be repeatedly produced. In this video from BigRep you can see a good example of this, where a curved window segment is cast over and over to produce all the pieces for a project:
That’s a straightforward example, but much more complex pieces can be contemplated. For example, one of BigRep’s clients designed an incredible concrete staircase that uses the same step piece repeatedly. The resulting staircase is said to be significantly less weight than traditional concrete stairs — and it certainly looks a lot more interesting.
Because of this it is likely that a prime application for this material is to produce concrete molds at a central location where pieces will be cast in advance of their use.
Another way to apply this technology is to assembly many 3D printed segments together to form a larger-scale mold. This might be useful for larger construction pieces, or for artistic sculptures that can be cast on site.
Either way, this is an exciting step by BigRep into a new world of 3D print application.
Via BigRep