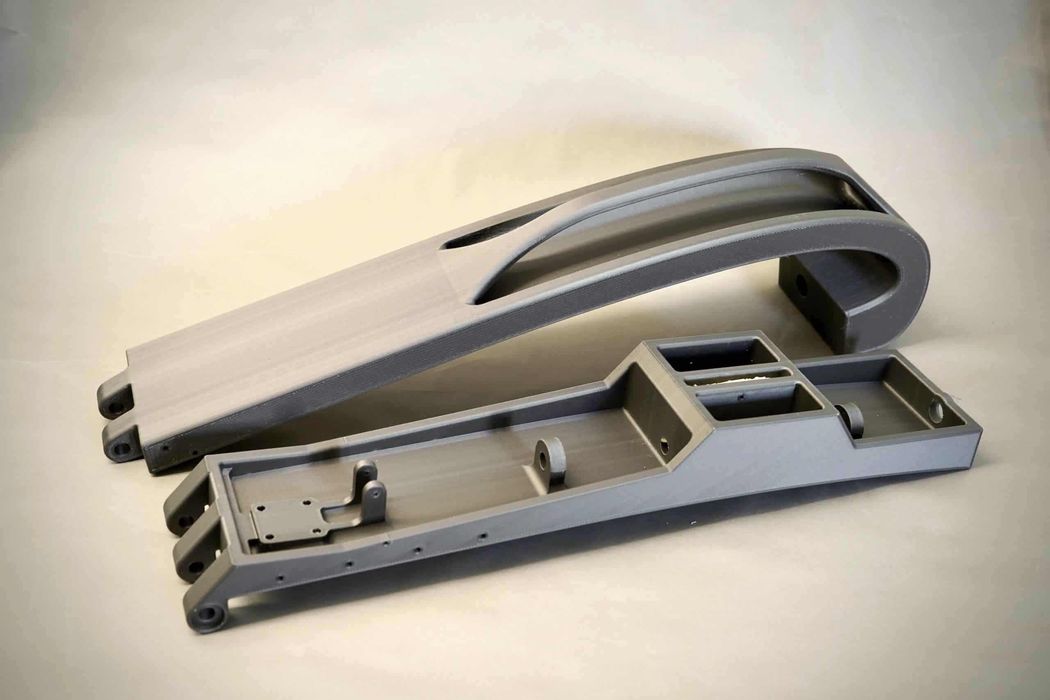
BigRep described very intriguing new application for 3D printing: Helicopter Blade Restraints.
If you’re not a navy helicopter pilot, you might not understand what a blade restraint system is all about. The problem is that when the helicopter is parked on a ship, it is subject to extreme weather conditions.
As you can imagine, ships can toss back and forth in waves, and there can be severe wind and spray. Of course, the helicopter is not flying in such circumstances, and it must be secured to the deck.
More importantly, the helicopter’s blades must be secured. These blades are literally designed to be in airflow, so they can be easily blown about by strong winds. The worst case would involve them striking something nearby or each other as they flap in the wind.
The solution is to release the clutch holding the blades in position, and move them around so that they overlap in a single cluster. To keep them clustered, a special device is used to hold them together: the helicopter blade restraint cradle.
Recently, SFM Technology was tasked with designing a new form of blade restraint due to issues with conventional versions. While many designers are still a bit itchy about using 3D printing for serious mechanical parts, the company decided to evaluate the possibilities.
They ended up working with BigRep to produce a new restraint cradle that should work far better at sea. BigRep was chosen as their equipment is sufficiently large to accommodate the massive print required to make the restraint.
There were other reasons under consideration, too. BigRep’s gear offered the right combination of print speed, quality and material choice.
It seems that for this application, SFM Technology used BigRep’s High Temperature CF material. This is quite an interesting choice because the carbon fiber content would produce extremely strong parts, which obviously would be desirable for this application.
The strength of the parts would be enormous considering their large size and the CF content.
The other interesting factor is that these 3D printed parts would be quite lightweight as compared to metal equivalents. In addition, they would be resistant to corrosion at sea, unlike many metal materials.
Note the mechanical stress this part is undergoing in this short video:
You can also imagine the huge helicopter blades being severely battered by gusts of wind at sea, with the ship rocking back and forth. That’s a pretty extreme environment for any 3D printed part.
Producing the part was done on BigRep 3D printers, and in this screenshot it appears that the print took only two days to complete. While that might be a long time for a desktop 3D printer, it is astonishing that such a huge part could be produced by a 3D printer in that time.
It’s an amazing application of 3D print technology, and further demonstrates the ability of the technology to address increasingly challenging situations in industry.
Via BigRep