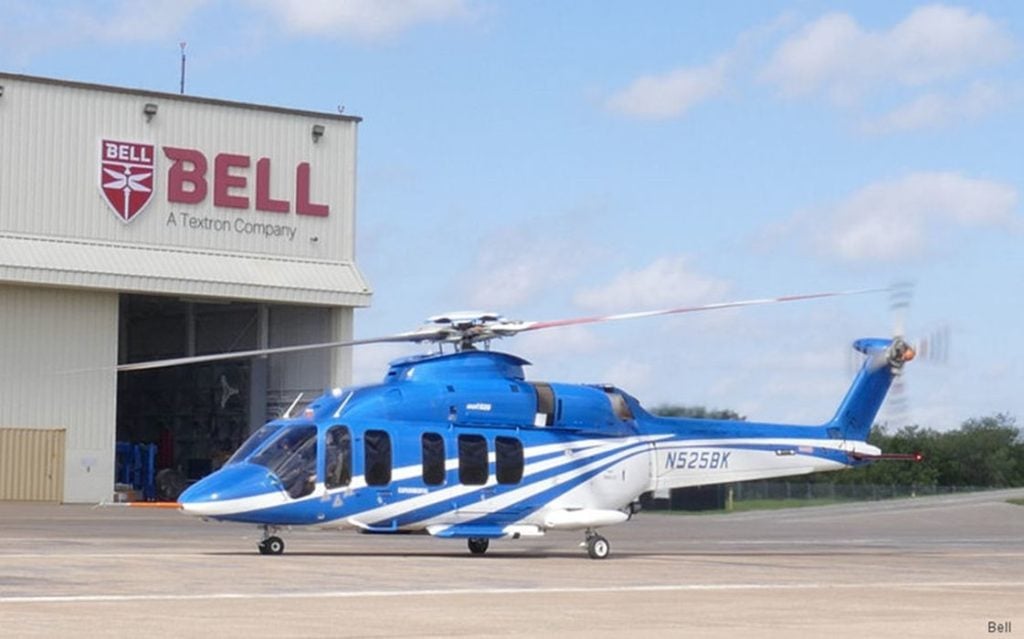
Charles R. Goulding and Preeti Sulibhavi look at how Bell have used a variety of 3D printing technologies and services to make parts for their helicopters.
Based out of Fort Worth, Texas, Bell (a subsidiary of Textron) was a part of NASA’s first lunar mission and has strategic locations around the world. Bell delivers exceptional aircraft products and experiences in a consistent and safe manner.
The first company to certify a commercial helicopter and break the sound barrier, Bell goes above and beyond to define the future of on-demand mobility. In our recent Fabbaloo article about Australia’s Blackhawk helicopter purchase, we mentioned the helicopter twinning process as well.
To top it all off, Bell is an avid user of 3D printing technology. Bell has collaborated with various companies in the 3D printing industry. Some projects are described here.
Thermwood
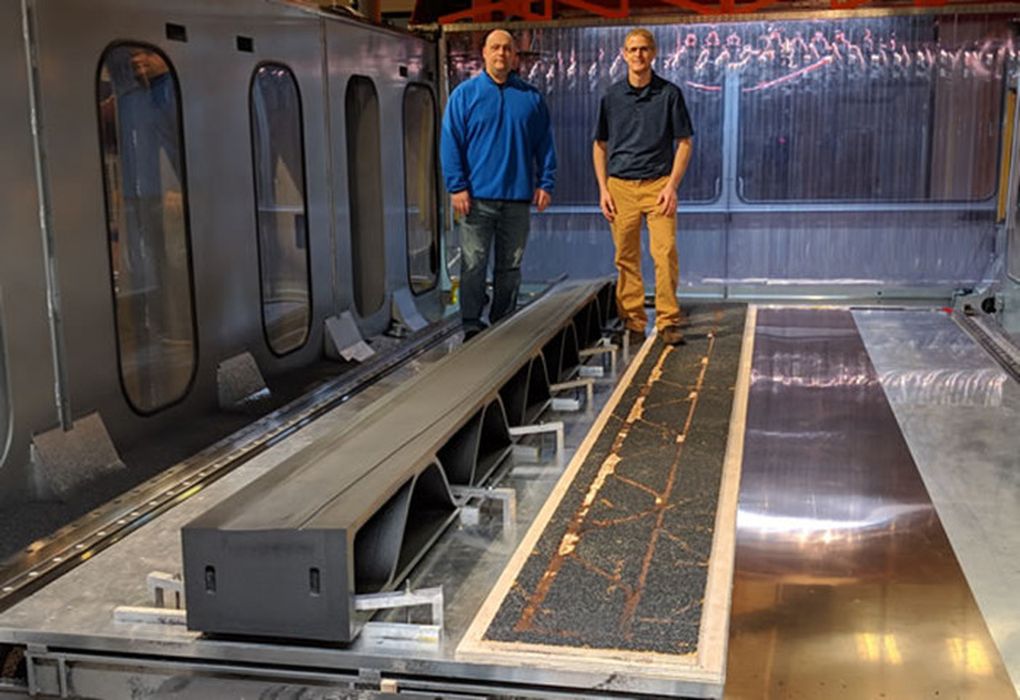
Thermwood Corporation, an Indiana-based service provider of CNC routers and large-scale additive equipment, has produced what some may deem the largest 3D printed autoclave tool for a helicopter to date. The project, brought to life through a partnership with Bell, utilized Thermwood’s LSAM 60 mm melt core technology and reinforces additive manufacturing’s applications in mold production.
To resolve the long-standing technical challenge in the aerospace industry in regards to extended-lead time tooling that is also expensive, Thermwood and Bell utilized 3D printed molds to quickly and affordably manufacture large bond tooling.
Ingersoll
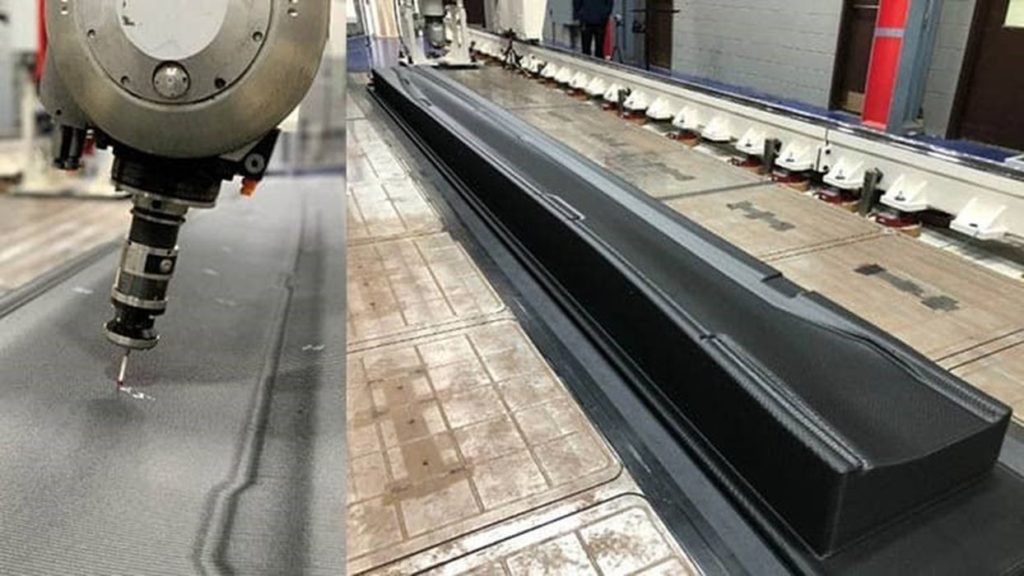
There are other 3D printed applications that Bell has applied to helicopter design and development. Bell has utilized the Ingersoll MasterPrint 3D printer to manufacture 22 ft long vacuum trim tool and produced main rotor blade components as well as tooling.
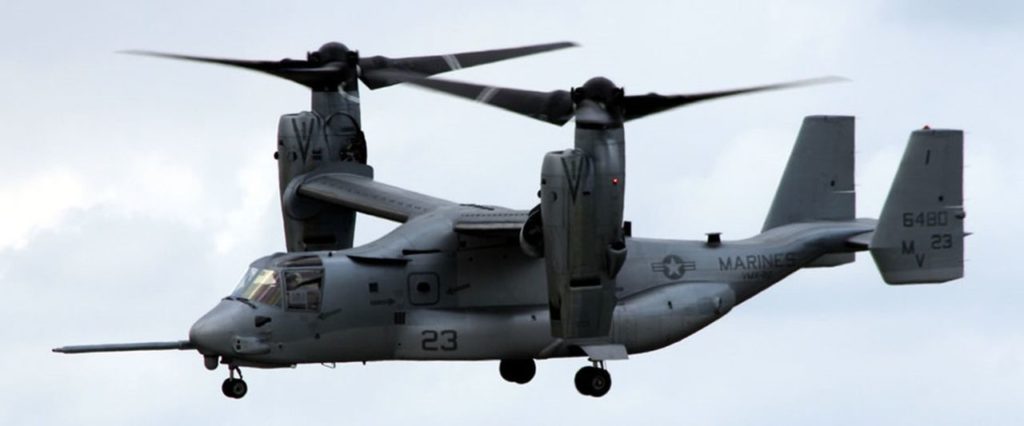
The 3D printing process was completed as a single part in a continuous 75-hour operation. After printing, the mold surfaced, and tooling location features were machined to finished dimensions by replacing the print module for the 5-axis milling head which is changeable on the MasterPrint machine. The Ingersoll machine uses the Siemens 840D CNC control system for controlling both the machining and the 3D printing.
Stratasys
Bell has benefitted from 3D printing technology in other ways as well. When the Bell Osprey had to undergo experimental tail wiring upgrades, engineers at the rapid prototyping lab at Bell Xworx used a Stratasys Fortus FMD Production System to build tough polycarbonate wiring conduits. The conduit was built for one stabilizer and it was installed on the mock-up. Once successful a second set for another stabilizer was initiated, and so on. The Fortus system allowed the Bell team to keep control of the project in-house and saved them six weeks time in prototype development and testing.
The Research & Development Tax Credit
The now permanent Research and Development (R&D) Tax Credit is available for companies developing new or improved products, processes and/or software.
3D printing can help boost a company’s R&D Tax Credits. Wages for technical employees creating, testing, and revising 3D printed prototypes can be included as a percentage of eligible time spent for the R&D Tax Credit. Similarly, when used as a method of improving a process, time spent integrating 3D printing hardware and software counts as an eligible activity. Lastly, when used for modeling and preproduction, the costs of filaments consumed during the development process may also be recovered.
Whether it is used for creating and testing prototypes or for final production, 3D printing is a great indicator that R&D Credit eligible activities are taking place. Companies implementing this technology at any point should consider taking advantage of R&D Tax Credits.
Conclusion
Helicopters are critical players in commercial air travel as well as defense operations. Ensuring they are built tough and safe to fly is critical. 3D printing can help ensure that these benchmarks are met with flying colors.