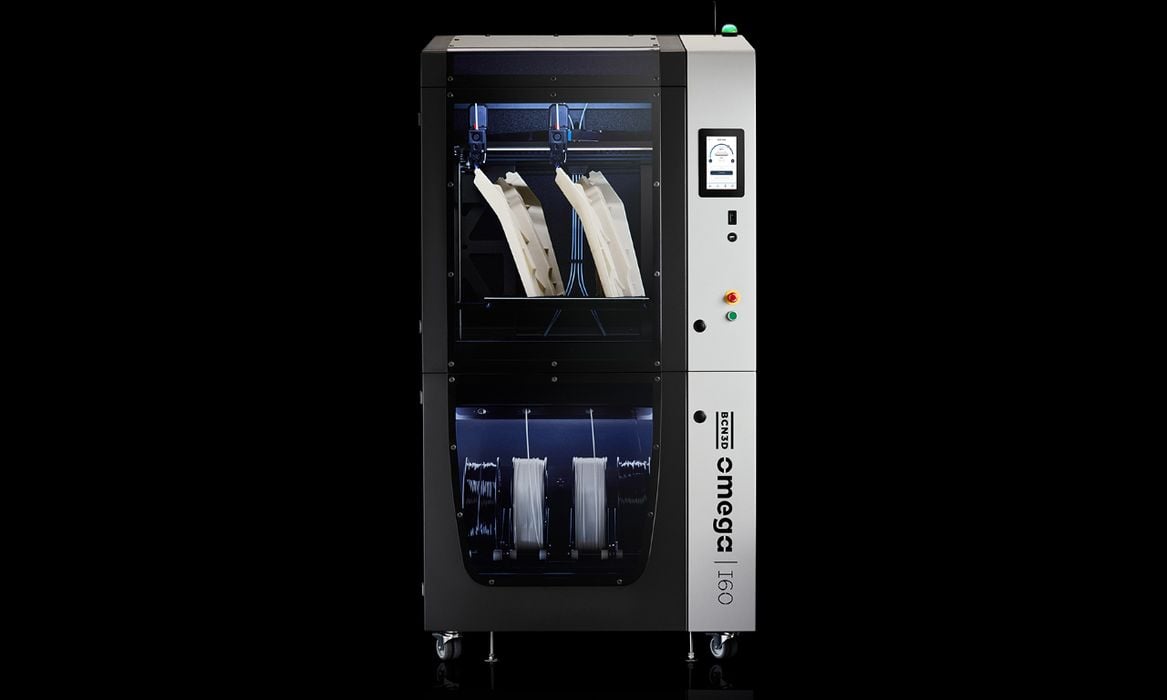
BCN3D announced new and rather interesting production FFF 3D printer, the Omega I60.
The device is targeted at industry and is intended to produce “strong prototypes”, but also end-use parts. BCN3D expects the I60 to be frequently used to produce jigs and fixtures in factory settings to improve efficiency.
BCN3D announced the I60 in an online event:
The I60’s specifications are impressive:
- Massive build volume of 450 x 300 x 450 mm
- High speed 3D printing (up to 300mm/s)
- Fully automated calibration
- 32-bit controller board
- Actively heated build chamber (up to 70C)
- Heated print surface (up to 120C)
- Dual independent extruders (IDEX)
- E3D Revo quick-swap nozzles
- On board dry filament storage with pre-loading capability
- Dual Z axes
- HEPA / Activated Carbon filtering
- Emergency stop button for factory use
- UPS system
- Color touchscreen interface
- Networking via wired or wireless
One of the most interesting features is the motion system. In recent months we’ve seen a number of 3D printer manufacturers release high speed 3D printers. Typically these use the CoreXY motion system design, which is less susceptible to vibration and can be cranked up to higher speeds.
However, the standard CoreXY motion system design allows for only one extruder. The I60 has two with its IDEX system.
While BCN3D could have simply used the standard motion system designs, they would not have succeeded as well at higher speeds. They chose to use what’s called the “HAQ-XY Kinematic” system.
I had not heard of this approach previously, but it appears to be a variation on the CoreXY concept that permits use of two extruders. A lengthy post on Hackaday in 2017 describes how this system works, and also indicates that a variation is being used by Markforged.
BCN3D describes the HAQ-XY system:
“This motion architecture is considered one of the best systems for dual 3D printers and CNC machines, as it provides a lightweight, robust and precise approach. BCN3D Omega I60 utilizes an improved version of this kinematic system by placing the pulleys in a more optimal position. As a result, the system experiences a significant reduction in torsional moments along the X axis during the printing process. These torsional moments are highly undesirable as they can have detrimental effects on the system’s performance and potentially lead to undesired deformations in the X axis, thereby directly impacting the quality of the printed parts.”
In other words, better parts at higher speeds, and that’s what everyone is seeking these days.
Another interesting feature is the materials storage system, which BCN3D calls the Material Operations System (“MOS”). It’s not a passive system, nor a basic heating system. Instead it’s an intelligently controlled system that can vary not only heat but also humidity. This allows operators to select the precise conditions for specific materials. The I60 will read barcodes on spools to instantly set up MOS appropriately.
Even better, the MOS actually will swap spools for you automatically, should one run out. This allows for unattended operation on long jobs in that huge build chamber.
The I60 is a very interesting industrial 3D printer that seems to have all the features one might require.
Via BCN3D