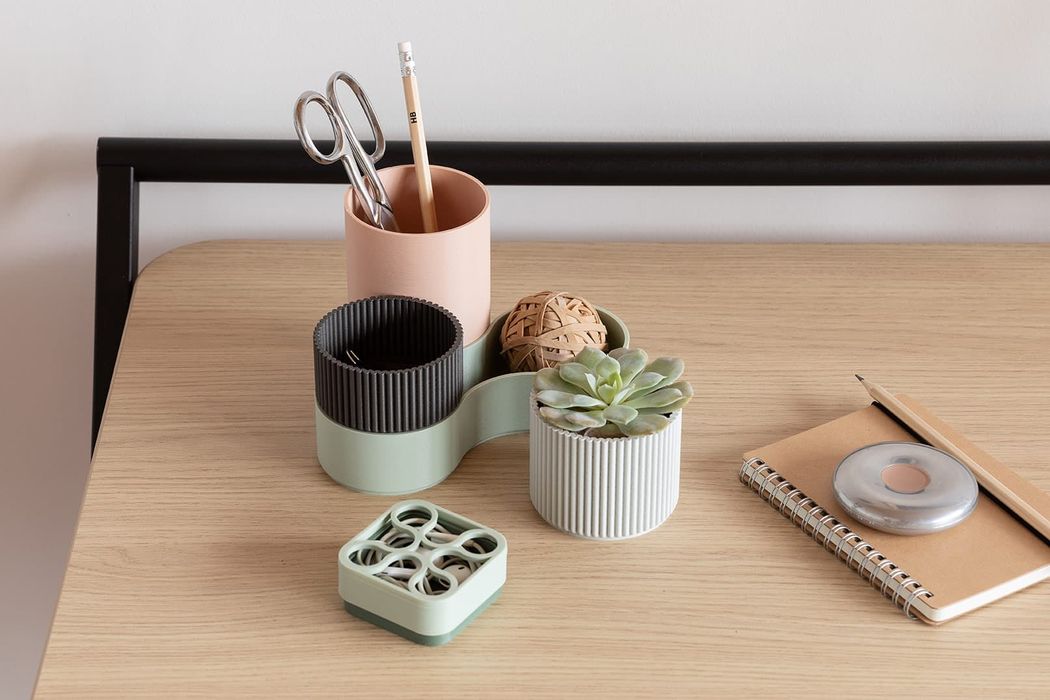
We were directed to check out Batch.Works, a startup company leveraging 3D printing to achieve sustainability.
There are plenty of design firms that leverage 3D printing to create unusual custom products, but Batch.Works seems to be a bit different. Instead of simply taking customer requirements and developing a creative solution, they also ensure the products are sustainable.
They say they are the “future of manufacturing”, and adopt eight key strategies:
- Circular Materials: All of the material we use is 100% recycled from traceable sources. Our focus is making small local material loops a reality.
- On Demand: Digital production means that we only ever make what’s needed, when it’s needed, where it’s needed.
- Re-Manufacture: We take responsibility for the things we make. Taking things back and finding new uses for them is part of our service.
- Short Supply Chains: Local production creates short supply chains that offer: reduced transportation costs, improved transparency, and increased agility in responding to customer demand.
- Digital Warehousing: By keeping inventory online there are no storage fees and no emissions created by shipping stock around the world.
- Digital Manufacturing: By embracing new technology we are low risk and agile. Our production methods reduce waste, and improve quality while maintaining cost-effectiveness.
- AI Quality Control: Systems provided by Matta Labs ↗ offer consistent inspection processes. Maintaining the highest quality standards and minimising production waste.
- Material ID: We are developing unique technology that enables part and material tracking, helping to reduce waste and improve supply chain efficiency.
This diagram shows their general workflow on projects:
As you can see, it is indeed circular. Of particular interest is the “re-making” stage, which is typically absent in normal production flows. There it seems they are re-using the made parts, either directly or through material recycling.
The company has apparently produced over 100,000 parts thus far, and recycled over five tonnes of material, so this isn’t just a concept. It’s quite real. They list a number of customer engagements that demonstrate these capabilities.
I’m wondering how this concept will play out in the future. It’s quite possible that the projects produced by Batch.Works may be somewhat more expensive than “normal” projects, but on the other hand there is increasing interest in sustainability.
The climate emergency, microplastics epidemic and other factors will all combine to provide a strong push towards sustainability for everyone and every operation.
Could it be that Batch.Works is pioneering a manufacturing approach that will become normal in the future? Will we see a world in which it would be shocking to see that a manufacturing operation is not circular?
That’s not the case today, but it just might happen in years to come.
Via Batch.Works