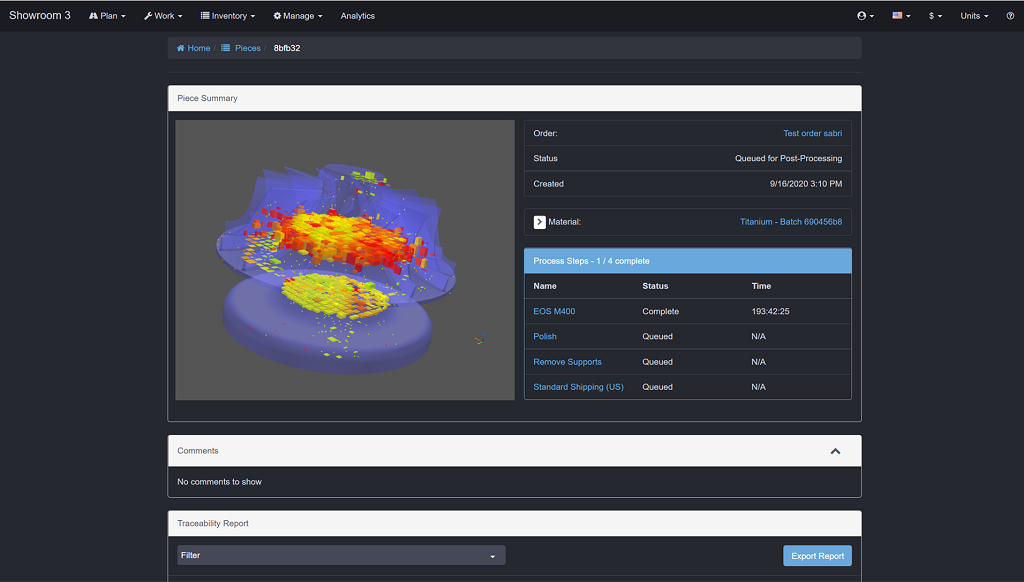
Authentise continues to expand its additive manufacturing workflow, introducing an integration of nebumind’s digital twin tools.
The Authentise Manufacturing Execution System (AMES) has seen a fair few expansions over the years. Most recently, this has included a new Material Management workflow and in-processing monitoring, the latter through an integration with Addiguru.
Authentise Integrations
Integrations are important to the future of the additive manufacturing industry, as we often discuss. No one company will ever have all the solutions, and collaborating can often produce stronger results for every partner involved.
For Authentise, integrating outside solutions into its additive manufacturing-focused offerings has proven a sound strategy already. The company has worked with other software companies– including Microsoft, Autodesk, and Prosper3D — as well as directly with 3D printer manufacturers.
Authentise x nebumind
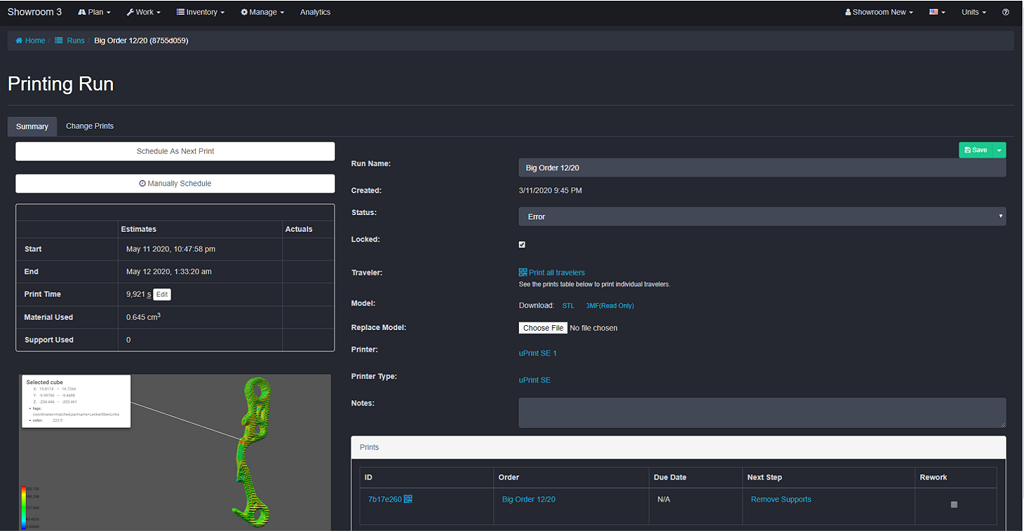
The latest integration is with nebumind. The Munich-based company describes itself on LinkedIn as “The first software visualizing manufacturing data as digital product twins to improve product quality & process stability.” That is, nebumind provides visualization and analytics tools for manufacturing data — including digital twin visualizations.
The concept of the digital twin is both simple and profound. Simply put, a digital twin is a digital likeness of a physical thing, be it a finished component or a manufacturing floor. More profoundly, it offers the capability to digitally interact with the physical — before anything is actually made, or simulating effects that would be seen in differing conditions in the physical twin.
In nebumind’s case, its digital twin visualizations “fuse machine parameters and sensor data with the original part geometry,” the announcement notes. It continues:
“The integration of these visualizations with AMES will help users identify problem zones of each part more easily and lead to less time intensive and more accurate inspections. In addition, real-time alerts generated by the nebumind system inside AMES will help the user address any deviations during the process, reducing waste. Since AMES already captures data from the machines and manages the printable geometry, the system passes this information on to nebumind automatically, saving the user from locating and uploading this information separately. The insight generated is appended to the existing AMES part report to ensure end-to-end traceability.”

Data-at-a-glance, especially real-time data from additive manufacturing processes, can substantially reduce the occurrence of failure. With 3D printing increasingly coming into play in high-value industries, failure can be a costly thing. That goes beyond simply losing out on expensive materials and valuable time; as a nascent technology, 3D printing is essentially still proving itself in real-world manufacturing environments. The technology is capable of end-part production, but doing so reliably in the field may be another question.
Using a digital twin, in the way that nebumind conceptualizes it, offers precise insights into exactly what’s happening. And, in the AMES workflow, that can mean instant understanding.
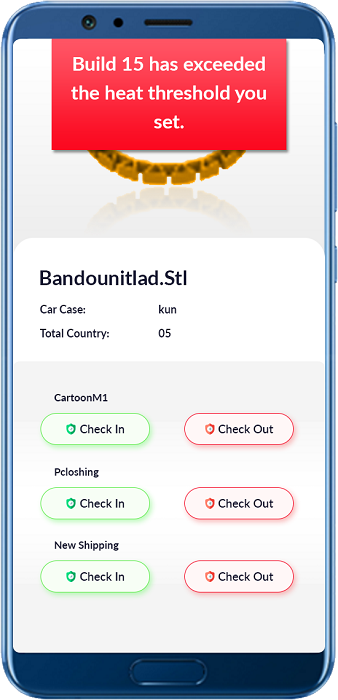
For Authentise CEO Andre Wegner, that capability is of vital importance. He tells us:
“I love working with partners like nebumind. Together the startups in the industry leave the behemoths in their wake. This integration embodies this perfectly — without nebumind you’d still be reading raw log files (if the machines will give you access to them); without this integration you’d still be trying to find the right log files, upload them to nebumind together with the right geometry to get a post- production assessment with no real-time alerting. With the integration the data gets sent automatically from Authentise to nebumind and the users get alerted in the web or mobile apps the instant something goes wrong.”
In the release, nebumind Co-CEO Franz Engel concurs:
“Additive users need to be able to review data at a single glance. To date all they are given is long and complex tables of sensor data that are difficult to make head or tail of. Thanks to the integration with AMES, we can get this data automatically and fuse it with the shape being produced. That way the user can see an instant heatmap of potential problem areas, and deep dive into every voxel to understand the underlying data if necessary. This view can help customers identify rework needs up to 10 times faster and reduce production rejects by up to 90%. Integrating this view with AMES makes sense, since that’s where production is managed, and data is held. We’re excited to be collaborating with Authentise to make the additive process more seamless and reliable for users.”
Having all the data in one place, both immediately accessible and, importantly, easily understandable, offers another step toward a seamless workflow.
In discussing the new integration with Wegner, the enthusiasm for the release was palpable even through a computer screen. He delightfully concluded our exchange by noting:
“It’s like stepping from the stone age, to the 21st century, into sci-fi territory in a nanosecond.
You probably shouldn’t quote that last sentence because it sounds dorky — but then I’m just excited!”
We are, too, Andre. This integration is another promising step forward for Authentise — and for additive manufacturing.
Via Authentise and nebumind