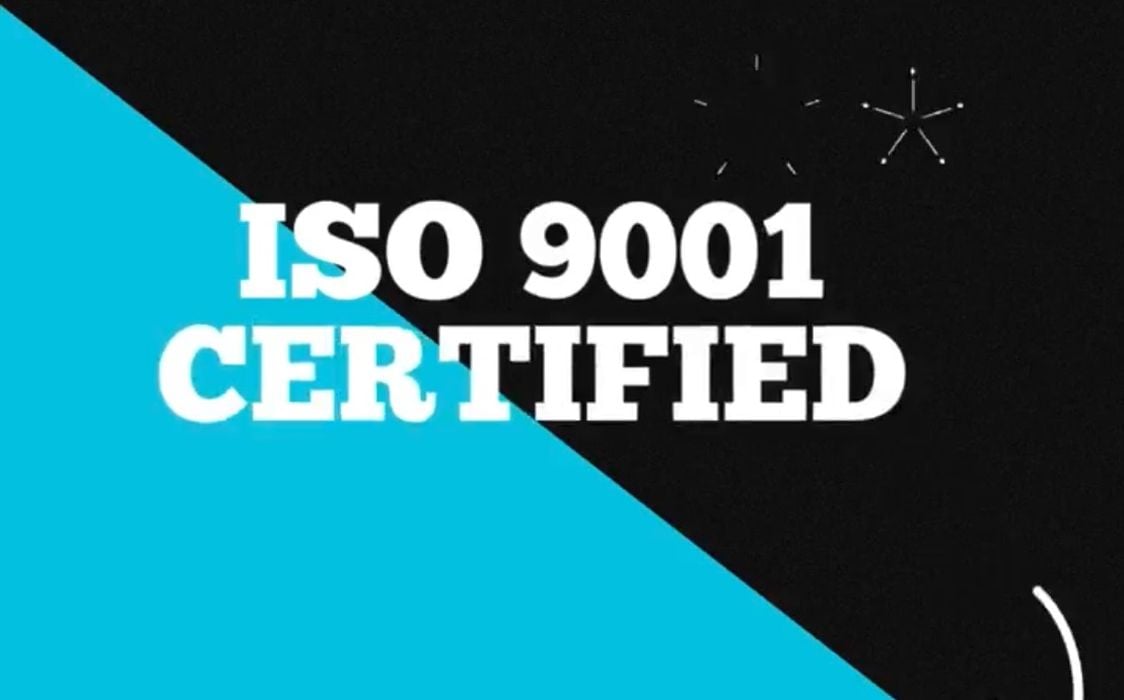
Aurora Labs has received a useful certification.
The Australia-based company has been rather quiet over the past couple of years, but they have been continuing to develop a very interesting high-volume metal 3D printing system.
Their concept is a twist on the usual one-layer-at-a-time LPBF approach used by so many metal 3D printer manufacturers. The layer-by-layer approach severely constrains the print speed as the job must continually wait for the toolhead and blade to sweep across the powder bed.
Aurora Labs’ approach is quite ingenious: they have devised a unique toolhead that deposits multiple layers in each pass, in a staggered fashion. As one layer goes down, it is fused with the laser, just as the second blade deposits a subsequent layer on top — all within the same toolhead pass. The toolhead has multiple layer capability.
This requires some tricky motion controls and requires the lasers to operate in a different way: they must continually ensure each zone is complete before more powder is laid down.
The result is a system that is theoretically capable of 3D printing one tonne of metal per day, a feat unattained in the industry, and highly desired by several heavy industries.
Over the past two years we’ve heard reports from Aurora Labs with experiments inching closer to that goal, and it seemed they will achieve it eventually. However, we haven’t heard of progress in that are recently.
Meanwhile, they have announced progress in another area: certifications. They wrote in a LinkedIn post:
“Aurora Labs is pleased to announce it has received its certification for its Quality Management System according to ISO 9001:2015.”
CEO Peter Snowsill said:
“This certification is a mandatory requirement for many of our partners, and we look forward to growing our AM Solutions business, leveraging our in-house developed metal 3D printing technologies.”
The ISO 9001:2015 standard relates to quality control, and specifically describes the management procedures and roles required to implement the quality management systems described in ISO 9000. The standards are generic and can be applied to any organization, regardless of business model or product being produced.
Organizations purchase the standard documents and then set up the required internal processes. When ready, a certified ISO auditor reviews their implementation and, hopefully, awards the official certification.
Why do this? ISO 9001:2015 not only cleans up internal processes to reduce problems, but also is a strong signal to external parties that the certified organization not only pays attention to quality control, but also has formally implemented recognized quality control methods.
Buyers of products can then have some additional level of assurance that the items acquired will have been produced using a reasonable quality control process.
Aurora Labs isn’t the first 3D print company to achieve ISO 9001:2015, but they are definitely not the last. There are plenty of companies that still do not have formal quality control processes in place.
Why don’t they?
Via LinkedIn