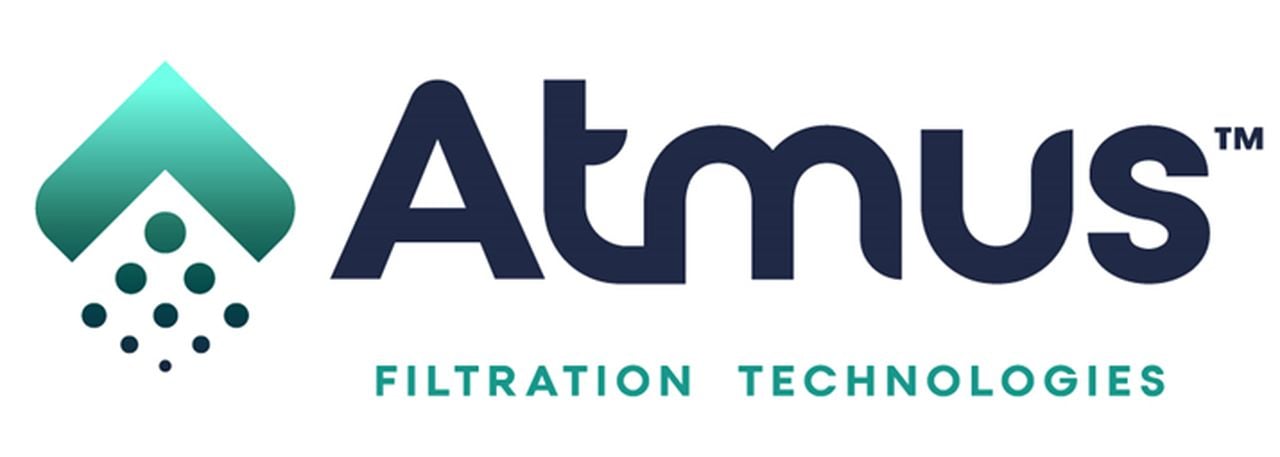
Charles Goulding and Valentina Alzate consider the potential for 3D printing in filtration technology.
At the commencement of the 2023 Memorial Day holiday weekend, Cummins, a renowned name in the diesel engine industry, announced the Initial Public Offering (IPO) of Atmus Filtration Technologies. This announcement carries significant weight, given the lack of IPOs and the scarcity of dedicated filter manufacturers in the industry.
Pall Corporation held the title as the largest dedicated filter manufacturer before being acquired by Danaher in 2015 for a staggering US$13.8B. Another standout in the industry was CUNO, a filter-only corporation that was sold to 3M in 2006 for US$1.35B. Today, one of the remaining noteworthy companies in this niche is Donaldson Corporation, which, along with Danaher, identifies the biotech space as a promising avenue for growth.
By leaving the captive Cummins OEM space, Atmus is poised to explore fresh opportunities in the industry. As a global entity, Atmus boasts an impressive 80% of sales originating from the aftermarket sector. According to the Atmus IPO, the aftermarket includes “sales of consumable or replacement products such as replacement filter elements, service parts, chemicals and coolant”. Atmus offers a range of different filter products including “fuel filters, lube filters, air filters, crankcase ventilation, hydraulic filters” and more. The company’s notable clientele includes prestigious names such as John Deere, Paccar, Volvo, Navistar, CNH Industrial, and Doosan.
With its market position and client base, we assert that Atmus Filtration Technologies is well-positioned to adopt and adapt to emerging 3D printing technology trends. In the IPO, the company notes 3d printing efforts as one of its four main pillars for first-fit growth opportunities. Specifically, the company notes they are “leveraging in-house 3D printing capabilities, utilizing powerful simulation tools and applying machine learning tools” to “Accelerate new product development”.
One way in which Atmus can adapt 3D printing technology can be by leveraging new innovative foam printing methods. A research team from the Skolkovo Institute of Science and Technology in Russia has modified the direct energy deposition printing technique to print metal foam. Metal foam is typically used in filters for oil and gas. The team’s printing technique involves using “a much lower laser power and a fine-tuned powder feed rate”. This new 3D printing method could help reduce the costs for metal foam, as well as improve the efficiency of filtration.
The Research & Development Tax Credit
The now permanent Research and Development (R&D) Tax Credit is available for companies developing new or improved products, processes and/or software.
3D printing can help boost a company’s R&D Tax Credits. Wages for technical employees creating, testing and revising 3D printed prototypes can be included as a percentage of eligible time spent for the R&D Tax Credit. Similarly, when used as a method of improving a process, time spent integrating 3D printing hardware and software counts as an eligible activity. Lastly, when used for modeling and preproduction, the costs of filaments consumed during the development process may also be recovered.
Whether it is used for creating and testing prototypes or for final production, 3D printing is a great indicator that R&D Credit eligible activities are taking place. Companies implementing this technology at any point should consider taking advantage of R&D Tax Credits.
Conclusion
As a cornerstone of various industrial processes, filters have found rising prominence in various industries including the biotechnical industry. The growth and expansion of 3D printing technology has opened the door to promising opportunities for revolutionizing and improving the filter industry. With the ability to tailor design parameters and streamline production, innovative 3D printed filter technologies can transform the landscape of the filter business sector by adding greater efficiency and precision.