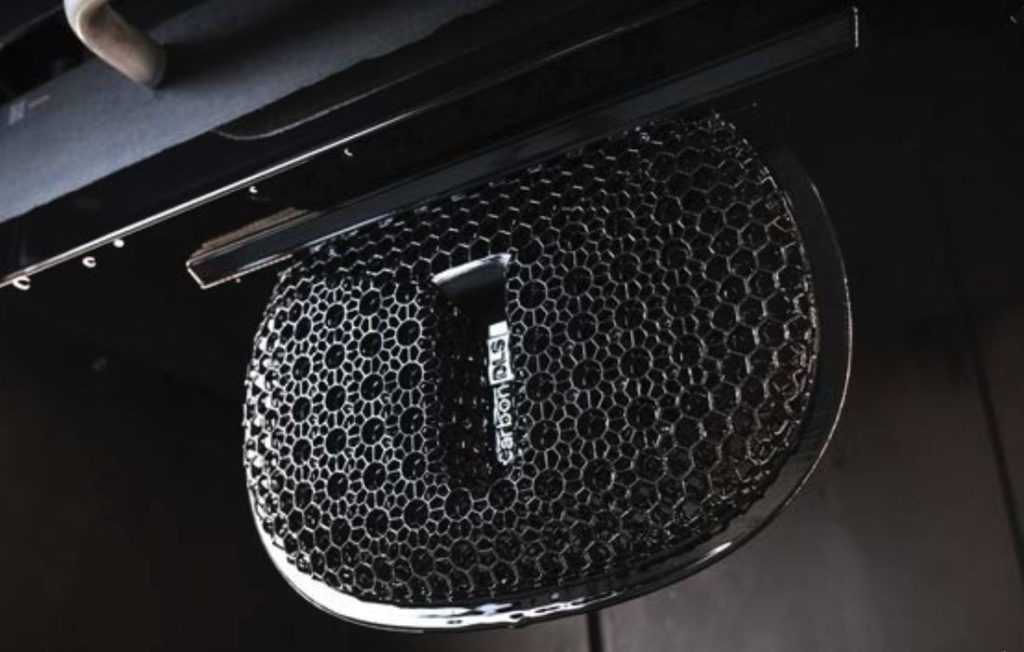
Carbon’s DLS 3D printing technology has made its way into another front-line consumer product.
Osprey is one of the world’s leading manufacturers of backpacks. The California-based company, founded nearly 50 years ago, produces an enormous variety of backpacks, specialized for many activities, including hiking, mountaineering, skiing, trail running, and much more.
Over the years the company has added a number of innovations to backpack science, making their products easy and comfortable to use.
The company’s website provides a “history” page where you can see in some detail their accomplishments for each year of their existence. New products and technologies are introduced, as well as corporate activities.
But now they may have another entry to add to their list of historic developments: 3D printed components.
The product in question is the Osprey UNLTD, an advanced, 21st century backpack design. Osprey explains:
“After nearly 50 years of innovation, Osprey is looking beyond traditional manufacturing technologies to bring you the ultimate backpacking experience through a new era of design and technology.”
The design of this product, which is pronounced “unlimited”, includes several very advanced features beyond 3D printing. This video explains what has been developed:
3D printing technology has been used in two parts of the UNLTD pack: a sophisticated lumbar support pad called the “Fitscape Lumbar”, and several points where the body-pack interface required better contact.
The lattice structure is ideal because it provides for much improved ventilation, is lightweight while still providing the mechanical lumbar support.
Carbon’s technology is quite appropriate for this application, as these pack parts are made from complex lattice structures. The lumbar pad in particular uses three different zones of firmness to provide not only suitable support, but also comfort.
Carbon’s Design Engine software was used to develop this complex 3D model, which was then produced on Carbon 3D printers for end use in the backpacks. Carbon has found the ability to create highly complex lattice structures is of specific use to certain consumer products where controllable function and lightweight parts are beneficial.
Their technology has previously been used in the production of complex midsoles for sneakers, as well as for shock-absorbers in sports helmets. The backpack is yet another implementation of this powerful technology that will directly benefit consumers.
Osprey believes the introduction of the new technology into the UNLTD series will eventually percolate down to other products over time. This could mean additional use of 3D printed components.
Carbon’s co-founder Phil DeSimone explained the project:
“Traditional manufacturing methods teach us that in order to push the boundaries of innovation, product development timelines need to be extended. The development of Osprey UNLTD proved the exact opposite. The entire process using Carbon DLS took about one year with only six months for us to iterate on the design, enabling Osprey to take this innovative product to market faster.”
While I initially looked to the product design for its 3D printed components, it turns out the UNLTD design is very sophisticated with a number of other features that deserve attention. If you are a backpack user, you’d better take a good look at the UNLTD line.
The new Osprey UNLTD design is provided in two styles, with mens’ and womens’ variations. The specific models are the Airspace 68 and the Anti-Gravity 64. The suggested price for these packs is £650 (US$850).