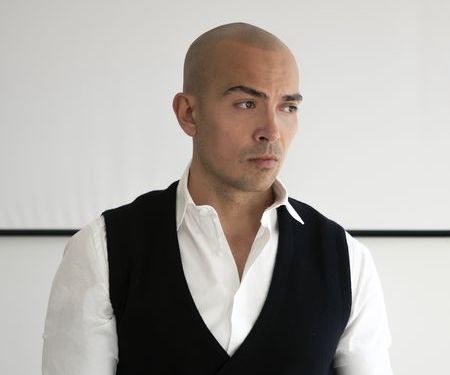
I spoke with Roboze CEO Alessio Lorusso recently and found out the current state of the Italian manufacturer of high-temperature 3D printers.
Via Zoom, Lorusso was excited about the company’s latest device, the massive Argo 1000 3D printer. It’s the culmination of a series of incremental improvements to their high-temperature technology that started only a few years ago.
High temperature 3D printers are somewhat rare in the AM industry, although there are more options slowly coming available. Roboze was one of the first to pursue this market, and also the first to develop means to 3D print high temperature materials in large formats. Lorusso describes the Argo 1000 as “Really huge!”
The benefit of high temperature 3D printers is the ability to produce unusual parts in engineering materials like PEEK. It is a very strong material, as strong as some metals, and offers very high heat resistance. This means it is possible to substitute PEEK parts for metal originals in some applications. This can dramatically reduce the weight of a system, be it an aircraft, vehicle or machine.
Announced last summer, the 2.5 tonne Argo 1000 is certainly the flagship device in Roboze’s line of 3D printers. But now as the market is becoming aware of the new Argo 1000 3D printer, Lorusso is finding many customers and prospects are finding unusual ways to make use of it.
Lorusso said:
“It’s being used by transportation, space and energy companies. We’ve found that customers already using our Argo 500 now are interested in part consolidation.”
The notion of part consolidation is a key driver for AM: instead of building a larger item by 3D printing multiple parts and assembling them, why not just 3D print the entire object at once? It is then possible to reduce weight even further by eliminating the need for bolts and lugs that would otherwise hold pieces together. That is what the Argo 1000 is all about: making very large metal-substitute parts with advanced designs.
Lorusso explained:
“The Argo 1000 allows customers for the first time to 3D print parts of one cubic meter, and it’s possible to 3D print unique geometries.
We are targeting weight-critical industries that can replace metal parts with PEEK parts. Lightweight parts are used in regulated industries, and PEEK can qualify for aviation, fire retardancy, etc., and offers the most aggressive chemical resistance. PEEK works in extreme environments.”
The company is looking for new clients in specific industries. For example, spare parts for railway companies is of particular interest, because a digital inventory can produce PEEK parts on demand rather than pre-making spares and storing them in an expensive warehouse. Many of these companies require parts made with certified materials, like PEEK.
Lorusso explained:
“Railway companies have a huge problem with spare parts. Trains are usually quite old. After ten years, there are no more spare parts suppliers.”
I asked Lorusso about the state of the company, and he provided an update:
“Currently there are more than 100 staff in both Italy and the US. We plan on hiring 70 more staff in the next 18 months, and are creating an in-house chemistry department. We already develop electronics, materials and chemistry in-house.”
The company now has dedicated around 40 staff to research and development, and another 30 for business development.
Lorusso described their growth to date:
“We are growing very, very fast in the US, and it’s now 50% of our global market. We’ve also opened a new office in Germany.”
One venture Lorusso is particular proud of is Roboze’s manufacturing network. Today they have more than 30 partners around the world using their equipment that can produce PEEK parts on demand. Lorusso said:
“It’s like having hundreds of micro-factories across the world.”
The network allows Roboze to receive requests to make parts, and they can dispatch them to the nearest and most appropriate partner for part production. The network also allows Roboze to arrange product demonstrations for prospective clients much more easily, as there is always a Roboze partner nearby.
Lorusso said they are seeing increasing numbers of partners interested in participating with Roboze’s manufacturing network.
With the coming explosion of AM interest, it seems that Roboze is well-positioned to take full advantage.
Via Roboze