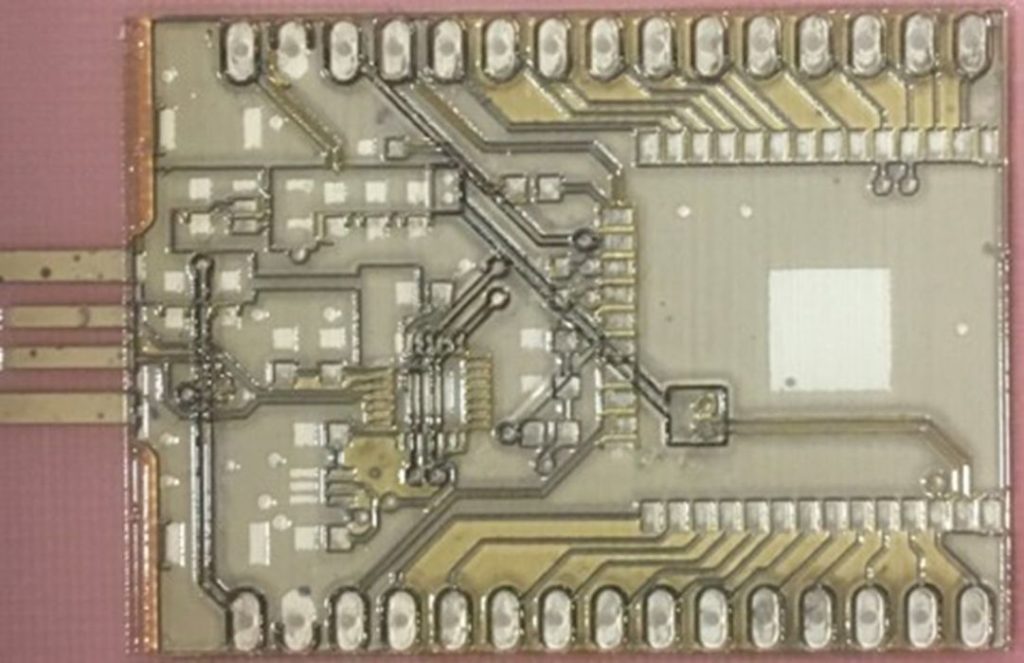
Charles R. Goulding and Preeti Sulibhavi interview Dr. Daniel Slep of ChemCubed.
On September 23, 2021, we had the opportunity to interview Daniel Slep, PhD, the CEO of ChemCubed located in Long Island, New York. ChemCubed produces 3D printer jettable nanocomposites that can be used to manufacture optical lenses, electronic components and other major verticals requiring structural applications including automotive, aerospace and defense.
We were particularly excited to perform this interview since Dr. Slep has a deep affiliation with Stony Brook University and five of our firm’s team members, myself included, are Stony Brook graduates. Daniel has a Bachelor of Science in Physics from the University of Connecticut, and a Ph.D. in Material Sciences from Stony Brook. He recently attended the Rapid 3D Event in Chicago, Illinois during mid-September and mentioned to us that he was glad to get back to visiting 3DP tradeshows.
For 3D printed electronics, ChemCubed is working closely with the NextFlex consortium, which is supported by the Air Force Research Laboratory (AFRL).
ChemCubed
ChemCubed is sponsored by Stony Brook University’s Advanced Energy Research and Technology Center (AERTC), where it is physically located. This affiliation with a major research university, including the AERTC, provides business support, collaborative projects, interns, and access to expensive instrumentation they might not otherwise be able to tap into.
The company creates materials for two primary vertical industry categories: electronics and mechanical parts.
Electrojet
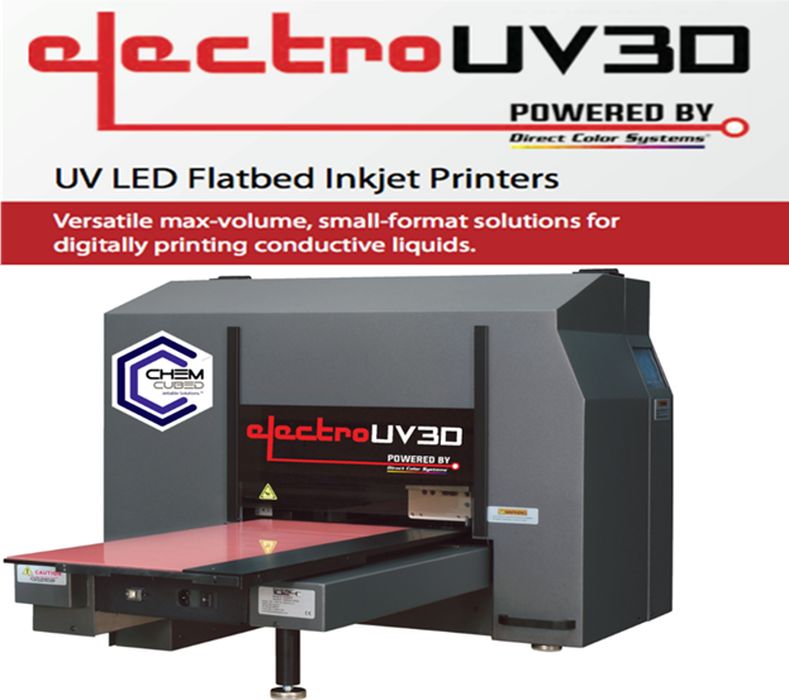
Electrojet is a material substrate used exclusively for 3D Printed electronics. This is a large market opportunity for the aerospace, defense, and automotive industries. ChemCubed materials are application-specific and made to order. ChemCubed has benefitted from working with the NextFlex consortium.
NextFlex is a consortium of companies, academic institutions, non-profits and state, local and federal government partners with the shared goal of advancing the manufacture of flexible hybrid electronics in the U.S. Since its formation in 2015, the NextFlex community of technologists, educators, problem solvers, and manufacturers have come together to collectively facilitate innovation, narrow the manufacturing workforce gap, and promote sustainable manufacturing ecosystems.
NextFlex is one of nine Manufacturing Innovation Institutes established by the DoD Manufacturing Technology Program as public-private partnerships and is funded through the AFRL Cooperative Agreement FA8650-20-2-5506. Among the 103 current consortium members are Lockheed, GE, BASF, Dupont, Raytheon, Saint-Gobain, and General Dynamics.
NanoCubed
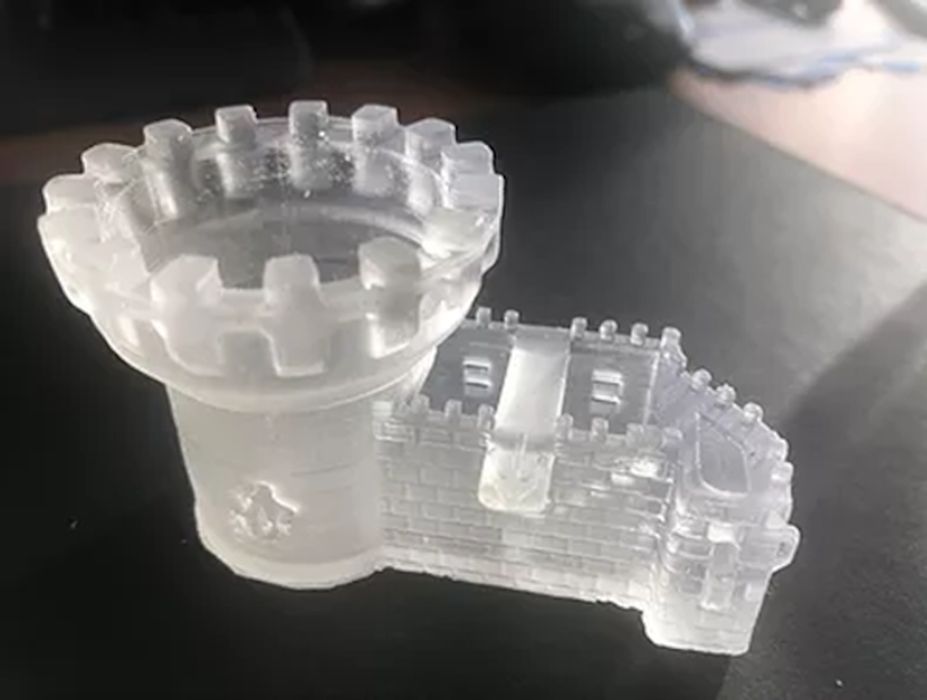
ChemCubed’s NanoCubed materials mimic the mechanical features of common polymers. Due to the high performance of these materials, they can be used for end-use applications rather than only prototyping and design. ChemCubed offers an array of custom-formulated resins with applications for the energy sector including fuel cells and batteries and for the health care sector. With these vertical markets, ChemCubed particularly benefits from its collaboration with Stony Brook’s Advanced Energy Research and Technology Center (AERTC).
Production Capability
ChemCubed has production capability and can supply materials, from small batches to large volumes of thousands of gallons of chemicals. ChemCubed is actually looking to scale up their production efforts.
The Research & Development Tax Credit
The now permanent Research and Development (R&D) Tax Credit is available for companies developing new or improved products, processes and/or software.
3D printing can help boost a company’s R&D Tax Credits. Wages for technical employees creating, testing, and revising 3D printed prototypes can be included as a percentage of eligible time spent for the R&D Tax Credit. Similarly, when used as a method of improving a process, time spent integrating 3D printing hardware and software counts as an eligible activity. Lastly, when used for modeling and preproduction, the costs of filaments consumed during the development process may also be recovered.
Whether it is used for creating and testing prototypes or for final production, 3D printing is a great indicator that R&D Credit eligible activities are taking place. Companies implementing this technology at any point should consider taking advantage of R&D Tax Credits.
Conclusion
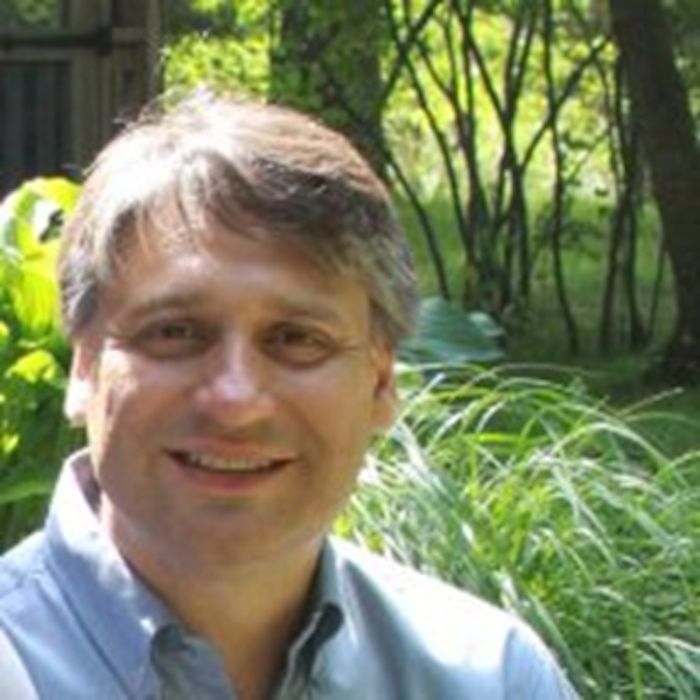
We were impressed by ChemCubed’s deep connection to a major University and its resources. Dr. Slep had only glowing remarks in terms of the good business support system Stony Brook University (SBU) has to offer. The collaborative efforts and use of post-doctorate fellows as interns before hiring them are great resources. Access to instrumentation via Core Laboratories at SBU offers reasonable pricing for use of the facilities. Especially with Covid, ChemCubed greatly benefitted from the use of SBU’s resources and collaboration.
Dan Slep, Ph.D. is married with three children. His wife is on the faculty at New York University (NYU) where his eldest will be entering the fall undergraduate class.