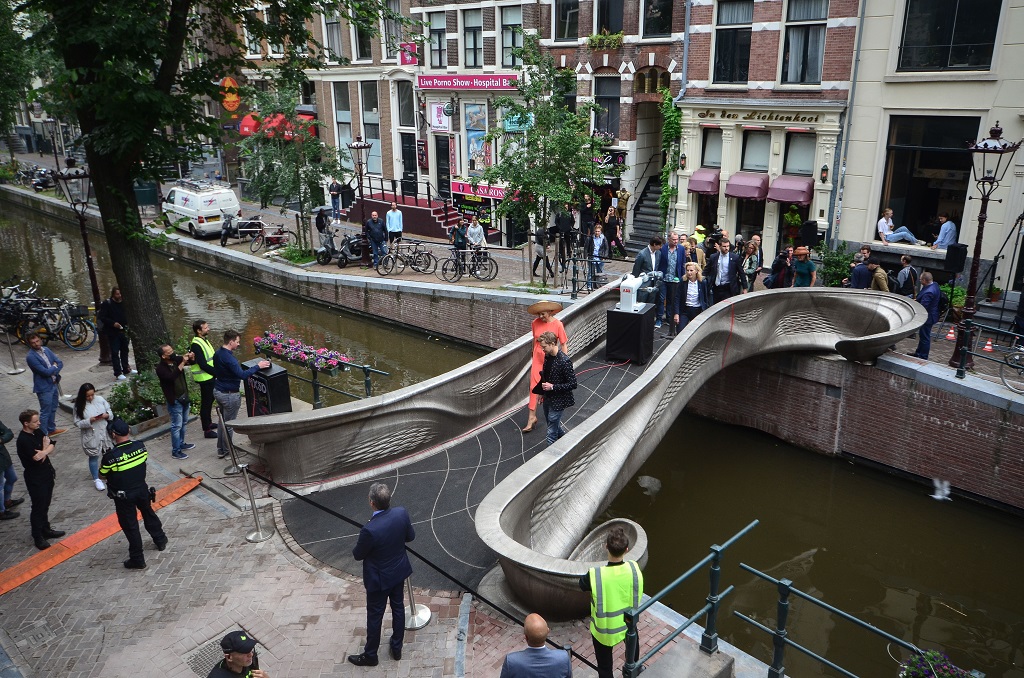
The long-anticipated stainless steel 3D printed Smart Bridge has finally been unveiled in Amsterdam’s Red Light District.
Planning the MX3D Bridge
In 2015, Dutch technology came to prominence with a bold plan to 3D print a smart stainless steel bridge that would span a canal in Amsterdam’s city center. Spearheaded by MX3D, the project drew a great deal of attention not only from the media, but from a large cast of collaborators.
“At the airport in San Francisco, on our way to discuss with our first main sponsor Autodesk their involvement in MX3D, we brainstormed about what the ultimate poster project would be for showcasing all of the facets of our technology. We reached the conclusion that a bridge over one of the old canals in Amsterdam would be a fantastic metaphor for connecting the technology of the future with the beautiful city’s past in a way that would reveal the best aspects of both worlds,” MX3D explains on its bridge timeline.
“It would look like it defies gravity; layer by layer we deposite [sic] metal that solidifies until the bridge is ready. The bridge project would, to a large extent, be a learning process; we don’t know how long it will take, but we are certain we can develop the software and hardware to make this project happen. In any case, it will be a great adventure and we are bound to discover new techniques. Autodesk, too, was thrilled to come aboard, and the project was born.”
Autodesk’s involvement was an early key for the bridge, as it was intended from the first to be “smart.” That is, sensors are integrated into the structure to read in real time the behavior of the pedestrians who cross it. Data about usage, weight, foot traffic patterns, and other real-world information is gathered for visualization. This is stored in the bridge’s digital twin, which can then monitor the health and performance of the bridge.
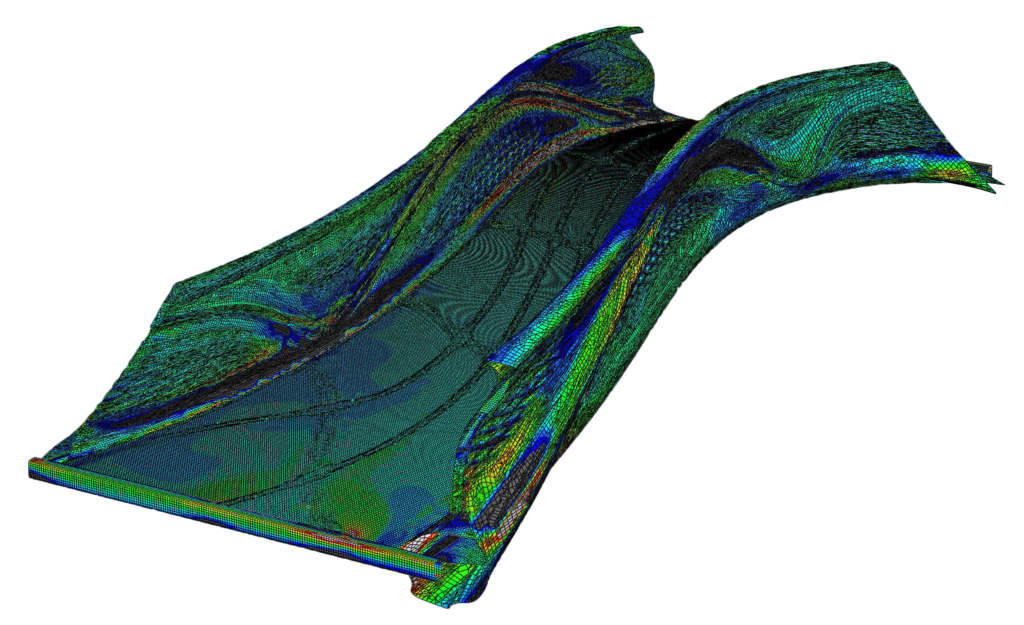
MX3D, Autodesk, the Alan Turing Institute, Arup, FORCE Technology, and the University of Twente all collaborated on the three-year development and installation of the advanced sensor network.
The bridge itself is a design from the renowned Joris Laarman Lab, with Arup serving as lead engineer. Additional partners included ABB (robotics), Air Liquide (welding gas), ArcelorMittal (material expert), AMS-3D Building Fieldlab (research), Amsterdam Institute for Advanced Metropolitan Solutions (research), FARO (scanning), HBM (sensor network hardware), Heijmans & Mous (construction expert), Imperial College London (material and structural analysis), Lenovo (computing), Oerlikon (welding hardware), and Plymovent (air cleaning hardware); also vital were support from the City of Amsterdam and funding from Lloyd’s Register Foundation.
Building the MX3D Bridge
To actually construct the bridge, four robots came together to 3D print more than 6,000kg of stainless steel. The actual structure was 3D printed in 2017 and 2018, with the first 3D printed section revealed in 2017. At Dutch Design Week 2018, more of the bridge was on public display.
Before it could be installed, a great deal of prototyping and testing, as well as permitting, had to happen. A structural element set to be placed in a highly-trafficked, high-tourism area requires substantial study and assurance of safety and viability — especially when it’s something made with wholly new construction techniques.
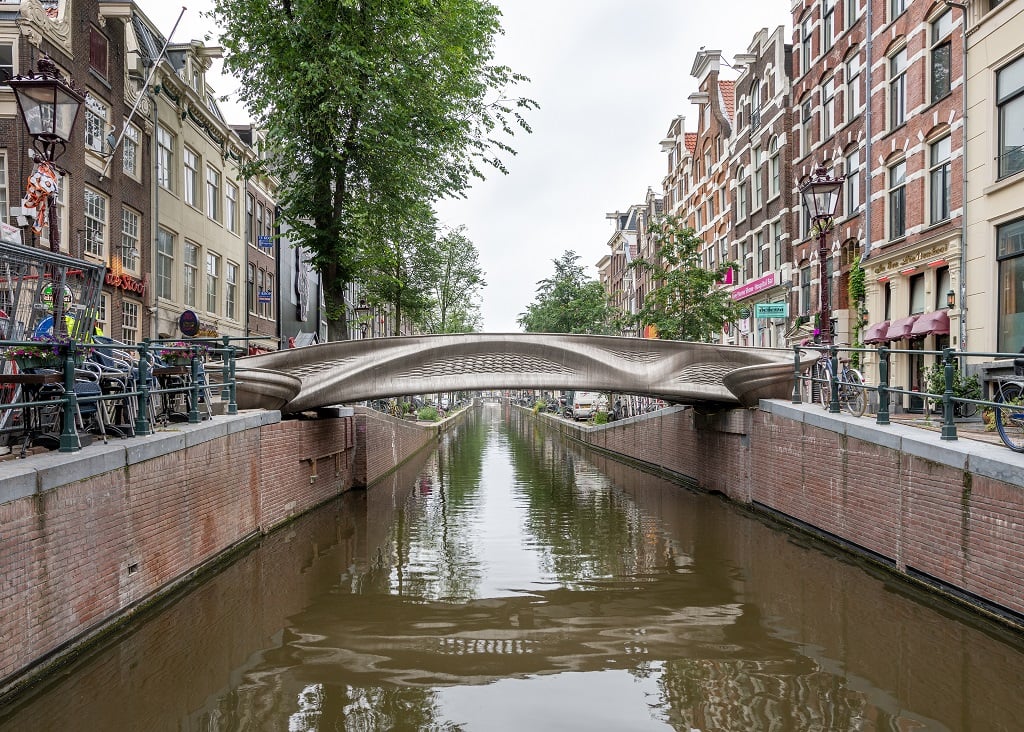
Those new techniques also raised questions of ethics. With the embedded sensor system gathering data, there’s a question about “open data, data ethics, and citizen ownership of city analytics,” MX3D’s announcement acknowledges. Gathering data to anonymously analyze the behaviors of crowds and understanding Red Light District tourism is an intriguing proposition, but not one without ethical questions about that data.
Those questions were part of a hold-up — again, the 3D printing was completed in 2018, and the project has been in process since 2015. It’s now mid-2021.
By 2019, many were wondering what was happening at MX3D and with the smart bridge project. The company was very busy, and the project never halted — but it was met with certain challenges that had to be addressed.
Load testing and material testing using the prototype form of the bridge’s sensor network proved out the capability of the structure. Testing from the Data Centric Engineering team at the Turing concluded that the bridge would be able to hold more than its ultimate design load, proved out for at least a 19.5 ton load.
The Turing remains involved, and will host the bridge’s data. The institute also conducted a “thorough ethics review of the project to ensure that the scientific goals of the project do not compromise the privacy of the public,” MX3D’s announcement notes.
Bridge sections moving down the canals of Amsterdam en route to installation [Source: MX3D / Photo by Merlin Moritz] The installed bridge ahead of its opening [Source: MX3D / Photo by Thijs Wolzak]
Ultimately, the City of Amsterdam granted the bridge a two-year permit for the bridge’s installation. That is: this beautiful, advanced bridge is not a permanent fixture. At least right now, as it is. But those two years mean a great deal of learning can take place.
Unveiling the MX3D Bridge
This week, the bridge was installed. Among the other hurdles overcome along the way was the physical preparation of its installation site. The masonry of the exact spot was not ready for the new bridge, and the final placement was postponed for almost two years while the canal walls were renovated to appropriately and safely hold the structure.
“We look forward to continuing this work as the project transitions from underpinning research to investigating the long-term behaviour of metal printed structures. Research into this new technology for the construction industry has huge potential for the future, in terms of aesthetics and highly optimised and efficient design, with reduced material usage. It has been fascinating and we are delighted that the structure is now ready to be used,” said Imperial co-contributor Dr Craig Buchanan, of the Department of Civil and Environmental Engineering.
To open the bridge, Her Majesty the Queen of the Netherlands, Máxima directed robotic arms to use scissors for a ceremonial ribbon cutting.
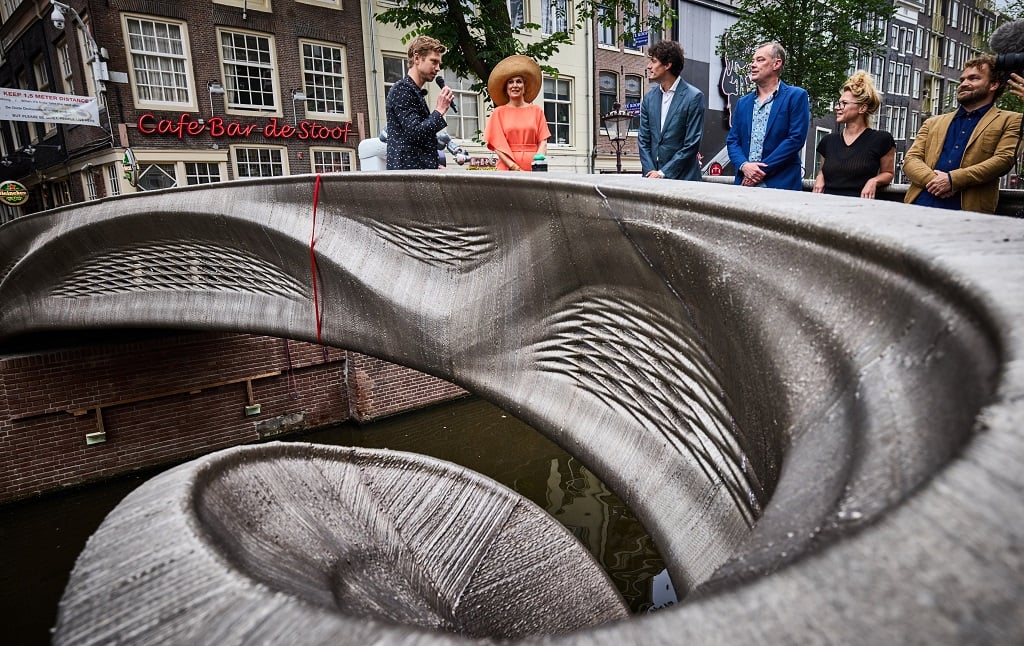
Now, the full 12.2-meter-long, 6.3-meter-wide, 2.1-meter-tall Smart Bridge is open and ready for foot traffic. For the next two years.
Via MX3D, Alan Turing Institute, and Imperial College London