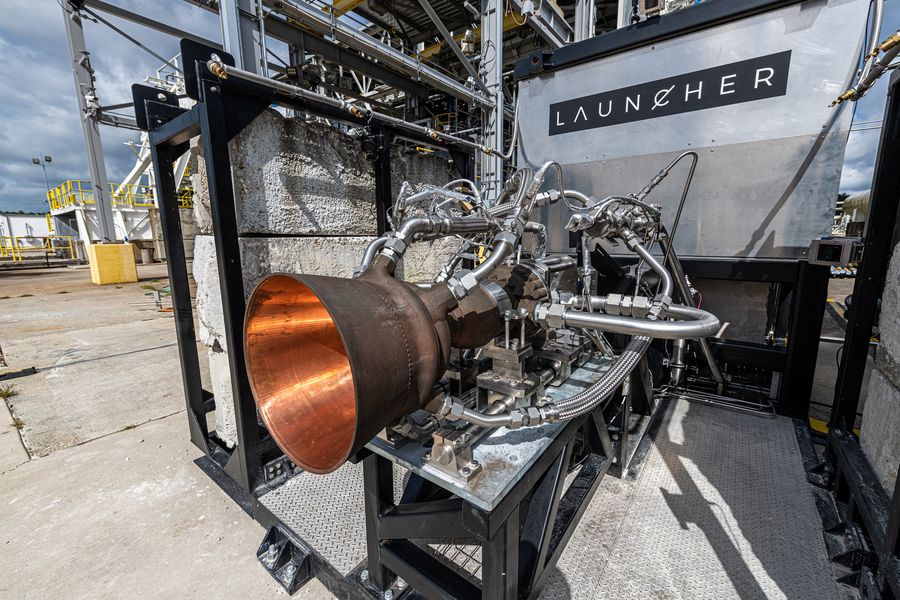
Rocket startup Launcher has acquired a massive custom-designed metal 3D printer from AMCM.
California-based Launcher hopes to build and launch a new small satellite rocker using a fully 3D printed engine, the E-2, which will produce 10 tonnes of thrust.
You might be wondering what the big deal is here, and there’s a bit of a story to explain things.
It turns out that rocket engines are far more complex than one would imagine. Visually, they appear to be a large bell with some plumbing on top. How hard could it be to 3D print, or even conventionally manufacture such a part?
However, there’s a significant problem with rocket engines: as they burn fuel and oxidizer, they generate tremendous amounts of heat. That is actually indirectly the goal, as more heat means more energy and thus operational efficiency.
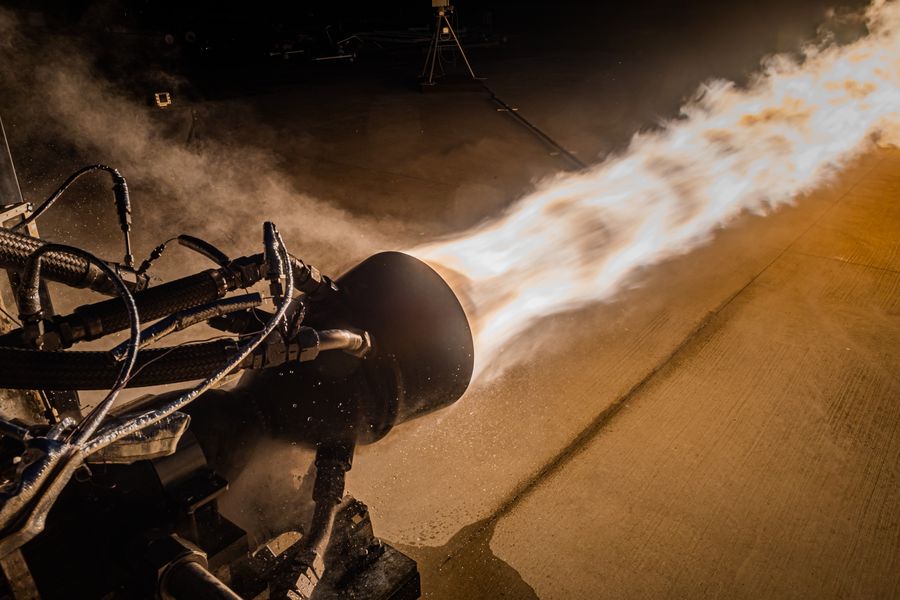
The problem is that there’s so much heat generated by the engine that it can literally melt the engine itself. To achieve maximum efficiency, rocket designers must push the envelope on all possible aspects of the engine design.
The usual solution to the heat problem is to circulate the relatively cool input fuel through the engine components, like the bell, before they enter the combustion chamber. This circulation is done through a very complex series of channels that carry supercooled fluids through critical areas. Sometimes you can actually see this complexity on rocket engine bells if you look closely.
Now, imagine manufacturing such a complex structure using conventional approaches. That’s why many of today’s leading rocket engine manufacturers are looking to 3D printing as the solution: arbitrarily complex geometries can easily be produced.
That all sounds great, but there’s more problems.
First, let’s say your rocket engine is large. Perhaps it’s larger than the build volume of commonly available metal 3D printers. While there are massive building-sized metal 3D printers on the market, they don’t offer the necessary accuracy, resolution or materials for rocket production.
There’s another problem: heat transfer. As you might imagine, it’s critically important to pull as much heat as possible from the metal engine components during flight, and this is best done with a material that is highly heat conductive.
A common material that fits the bill is copper. However, copper is a very difficult metal to 3D print because its very heat conductivity tends to bleed heat into surrounding powder, sometimes fouling the print quality.
With all these constraints and problems, what is a rocket engine manufacturer to do?
In the case of Launcher, they turned to AMCM, a spin off unit of EOS, which takes on unusual projects such as this. Their approach is to develop a custom AM solution for the client that encompasses not only the 3D printer, but also the materials and process involved. The “CM” in AMCM stands for “Custom Machines”.
Previous projects from AMCM include medical tablet printing with Merck, and another rocket engine for Orbex.
Recently Launcher and AMCM unveiled the solution to their project’s needs, and it’s a whopper: the M 4K AM System.
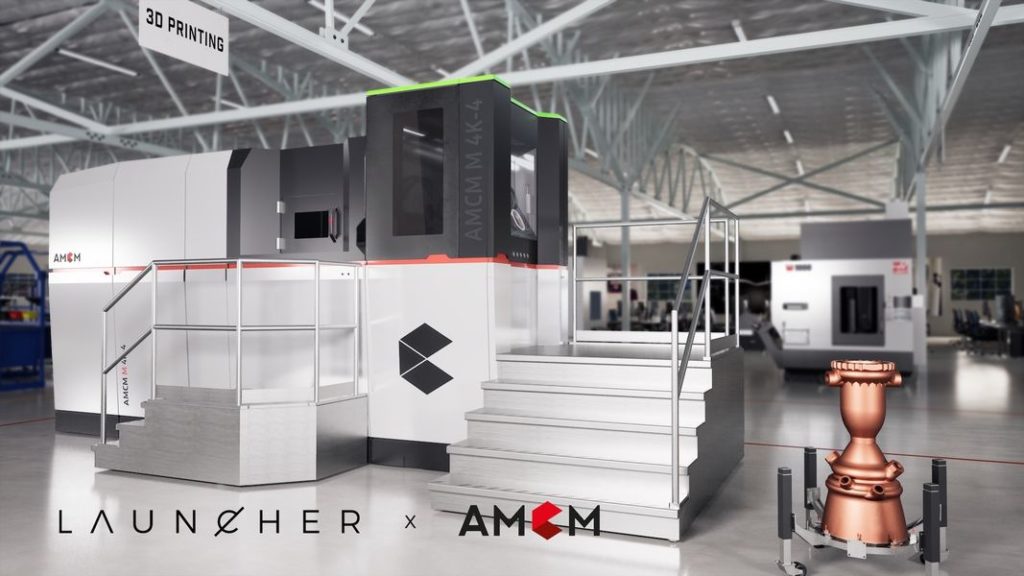
This is a beast of a machine, sporting a massive build volume of 450 x 450 x 1000 mm, and equipped with no less than four high-power lasers to very quickly complete 3D print jobs.
But perhaps the most interesting feature of the M 4K AM System is that it is designed to support copper alloy. This makes it the ideal machine to produce efficient rocket engines, and Launcher will be using it to build E-2 engines.
AMCM explains:
“Most companies building 3D printed liquid rocket engines have been forced to design smaller engines or produce multi-part combustion chambers to fit within the limited construction volume constraints of commercial 3D printers. With Launcher’s commitment to the industry’s highest propulsion performance benchmarks, it needed to 3D print its E-2 engine combustion chamber as a single part, enabling optimal cooling channel design, fewer parts, simpler processes, and lower overall production costs. In addition, while most companies developing 3D printed liquid rocket engine rely on Inconel alloy as their combustion chamber material, copper alloy is the best material for liquid rocket engine combustion chambers due to its optimal thermal conductivity properties, which enable more effective regenerative cooling. Informed by NASA research on 3D printed copper, Launcher requested copper alloy support in 2017 for the AMCM M 4K machine from AMCM and EOS.”
This is, I believe, a significant development, as it now places on the market a very large format metal 3D printer capable of producing copper objects.
Copper is an incredibly useful material that has not yet had it’s full abilities exposed to 3D print technology due to the reasons above. I speculated in 2020 that copper would soon break through and become a highly desired material, and it now appears that’s becoming true.
The M 4K AM System isn’t for everyone, but for some, it’s the exact machine required.
Via AMCM