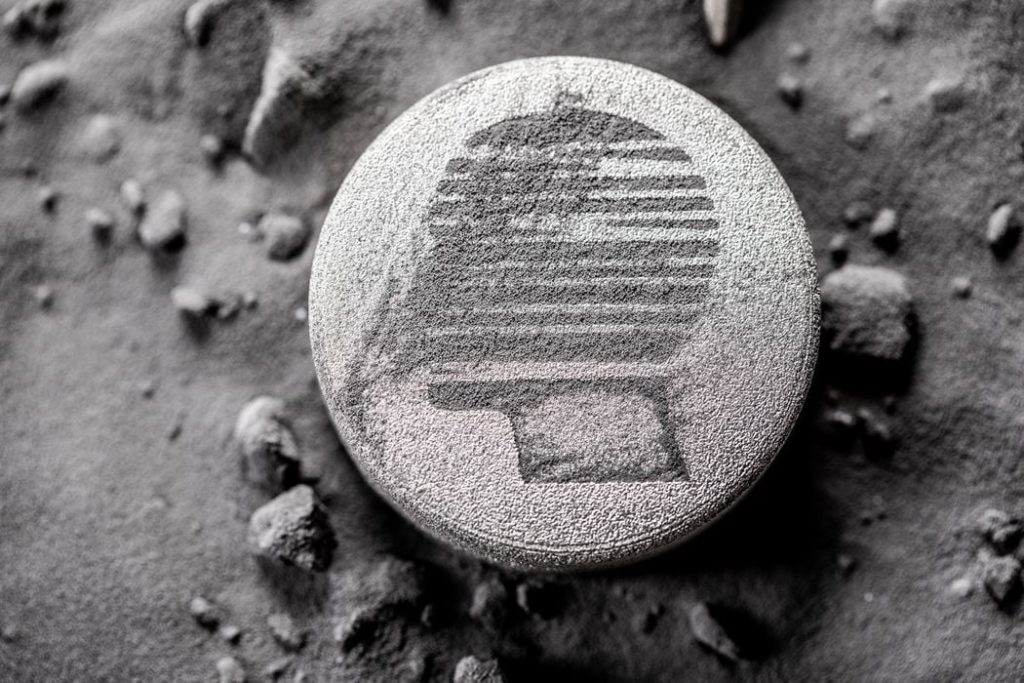
AM Ventures announced yet another AM startup in their portfolio: Headmade Materials.
This German startup is not well-known — yet — but could be if their ColdMetalFusion process catches on. It’s an unusual combination of polymer and metal 3D printing approaches that creates metal objects.
Rather than building a 3D printer of their own, they simply use existing SLS 3D printers for the ColdMetalFusion process. SLS 3D printers normally will selectively sinter layers of polymer powder to produce thermoplastic objects, most typically in nylons.
However, the ColdMetalFusion concept involves sintering their proprietary material rather than standard polymers. Headmade Materials offers several metal material options:
- Stainless Steel 316L
- Cobalt-Chrome
- Titanium Ti6Al4V
- Titanium CP-Ti (Grade 1)
- Tungsten
And under development they will also soon add:
- Stainless Steel 17/4PH
- Tool Steel
- Copper
- Super Alloy
Note that copper is one material that is extremely difficult or impossible to 3D print on typical LPBF metal 3D printers.
Headmade Materials explains their material capability:
“Our Cold Metal Fusion 3D printing process is less demanding because the primary metal powders are embedded in a plastic matrix. This enables us to make a wide range of metal powders available for 3D printing, including very fine or coarse as well as angular powders. And by binding the metal particles, the occupational health and safety requirements are reduced compared to pure metal powder.”
Once the “green” object is printed in the SLS device, it is easily removed and depowdered. Remember, the SLS process does not require any support structures because the surrounding loose powder holds up any overhangs.
Headmade Materials explained that in the green state the parts are easily milled, drilled or otherwise modified before being transformed into solid metal. This is an interesting step I haven’t seen leveraged by other metal 3D printing processes.
The green part then has the polymer binder removed with a solvent, and finally it is fired in a furnace to sinter the remaining metal particles together. Headmade Materials said parts will typically shrink slightly at this stage.
Using this process it would be possible to easily produce metal 3D printed parts at an accuracy and resolution equal to that of the SLS 3D printing system.
I do have some questions about this process, the most notable being safety factors. Many metals are toxic and some even explosive, and for this reason typical LPBF metal 3D printing systems have extensive atmospheric seals to ensure the fine powder doesn’t become airborne or exposed to oxygen. Typical SLS 3D printers are not designed in this way, and thus I’m wondering how Headmade Materials overcomes this issue.
Nevertheless, their approach appears quite powerful and scalable. This will surely attract investors, which have already funded the startup.
Now, however, they have organized a Series A investment round. A “Series A” is typically a large amount of cash to enable a proven technology to properly expand into new markets. This round was sourced from the European Innovation Council and AM Ventures.
AM Ventures is a growing venture capital firm specializing in additive providers and applications. Some of their investments include: 3YOURMIND, Lithoz, DyeMansion, Cubicure, Sintratec, and incus.
AM Ventures is providing €2.5M (US$2.9M) of the round, while the remainder is from the EIC.
Via Headmade Materials and AM Ventures