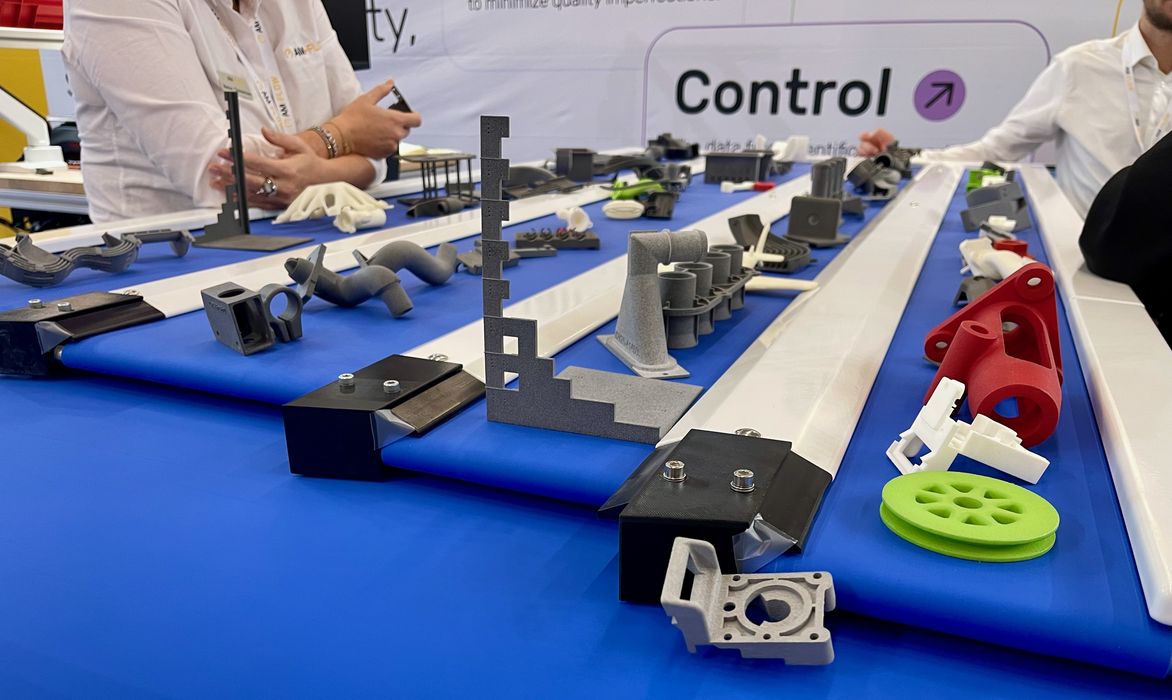
AM-FLOW has an interesting concept for handling completed 3D prints that beats the robots.
AM-FLOW focuses on the post-printing steps required in additive manufacturing. No, they don’t do part polishing or painting, but instead handle the “flow” of parts.
Imagine a large 3D print farm running 24/7: there will be a constant stream of parts being produced, often of different types. While there may sometimes be consistent identical parts being produced, often there will be a variety required for different clients.
This means that someone must sort out the pile of parts that are being constantly produced and ensure they are handled properly during post processing.
That’s where AM-FLOW comes in. They’ve developed a series of highly interesting mechanisms that can collect, move and sort 3D printed parts efficiently and without much need for human intervention.
Their systems can accept a series of parts and by using 3D scanning systems can identify a part within five seconds. Having that identification then allows them to route the part through their conveyor system to an appropriate stop.
Those stops might be a box for collection, or it could be a queue for painting or other post processing treatments. They even offer an automated bagging and labeling system.
I recently had a chat with their team and learned of yet another interesting innovation.
They’ve found that it can take a considerable amount of time for operators to place prints on the belt system. The prints must be spaced apart so that the scanning unit can properly see them, and that takes some effort to do.
It seems that AM-FLOW experimented with a robotic solution to take the human out of the equation, but it was unsuccessful: the parts would get tangled up together when picked up by the robot, and there was difficulty handling arbitrary shapes.
Remember that the print farm is producing tons of potentially different objects all the time.
Eventually, AM-FLOW concluded that the robotic approach did not work due to a high number of rejections for the above reasons.
Instead they developed an alternative approach to reduce operator time that is quite ingenious, and yet simple at the same time. If you look at the above image you can get a sense for how this works.
The operator collects completed prints from the 3D printers, and literally keeps them loose in a box or bin. The bin is then taken to the strange conveyor system shown at top, and the operator simply dumps them all out in a pile.
The only step for the operator then is to, with their hands, push the parts out across the various belts in a loose an informal manner.
Then the conveyor system takes over. Each of the conveyor belts moves at different speeds and times, all slowly moving the parts towards the main belt at the bottom.
By the time the parts reach the main belt, they are sufficiently separated. The main belt moves much faster than the other belts for this purpose.
It’s quite fascinating to watch in action, and it really does seem to work, at least for parts that fit this system. I’m sure, however, that it would be possible to scale up the concept for larger parts.
The result of this system is that it dramatically reduces operator time. While the main AM-FLOW system does all the sorting, this new input belt system almost eliminates the need for the operator to provide input for the AM-FLOW system: you just dump a pile of parts on the belts.
This is quite an ingenious system that should be of great interest to AM-FLOW customers.
Via AM-FLOW